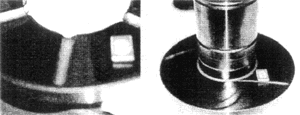
Fig.10: Floating disk (left) and thrust collar (right) after 12,000 operating hours on an HFO operated 4-stroke engine
2.2 Turbocharger
The thermodynamic performance of the TPL..-B components has been described above. A representative efficiency characteristic for a TPL..-B turbocharger is shown in Fig.11, the measurements having been performed on a TPL85-B12 turbocharger on one of the ABB burner test rigs. The efficiency level for high compression ratios is above 70%, which leads to low fuel consumption at full load operation. This level can be maintained even at low compression ratios providing the part-load performance is good, resulting in low component temperatures on the engine side. The efficiency level of the TPL85-B12 is achieved in parallel with a very high specific volume flow.

Fig.11: Turbocharger efficiency measured with a TPL85-B12 on burner test rig
The new filter-silencer used with the TPL..-B turbocharger series causes only a very small pressure drop even with high volume flows, as shown in Fig.11.
A lubrication oil emergency gravity tank has been developed that ensures safe run-out of the turbocharger in the event of a possible shut down of the engine lube oil supply. This system is a part of the turbocharger itself, so that no additional installation is necessary on the engine. The system's design minimises any risk of malfunction or leakage. Also, no active components are used. An extensive series of tests carried out on a burner rig as well as on a two-stroke engine has verified the reliability of the system even with the turbocharger in an inclined position. No signs of metal to metal contact in the bearings could be observed after the tests.
2.3 Test Procedure
New technology is essential to the development of a new turbocharger. A new and successful turbocharger implies, besides technology, reliability and robustness too. The consequence of this is that the TPL..-B has to satisfy nineteen qualification tests, ranging from high-cycle resonance endurance tests to the practical try-out of all service tools. The objective of this qualification procedure is to simulate the projected operating, and even worst case conditions. For example, the rotating parts are put through vibration and low cycle fatigue tests. Blade vibration measurements are performed not only on a burner test rig but also on a two-stroke engine. A thermal cycling test is as much a part of the test procedure as shaft motion measurements or oil and gas leaking tests.
3. ENGINE EXPERIENCE
The first engine applications for the TPL..-B were the 3xTPL85-Bll units installed on the new 7K98MC engine and 2xTPL80-B12 units fitted to the 7RTA84C engine, see Fig.12. The shop tests were successful, as were the sea-trials. These vessels have been in operation since beginning of 2000. There have been no problems to date, and the turbochargers have come up to expectations.
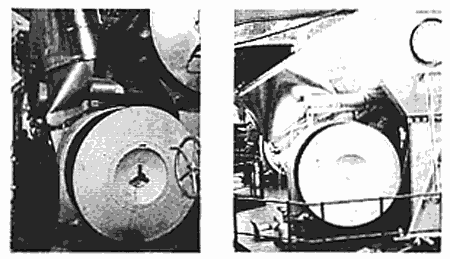
Fig.12: Engine applications. TPL85-B11 on a 7K98MC and TPL80-B12 on a 7RTA84C
An overview on engine measurements in Fig.13 and 14 shows the high achievable efficiency level as well as the flexibility with regard to the efficiency characteristic.
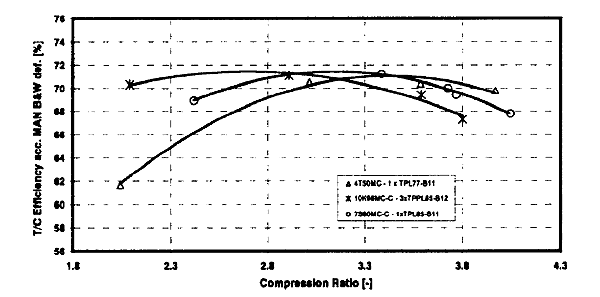
Fig.13: TPL..-B performance measured on MAN B&W engines
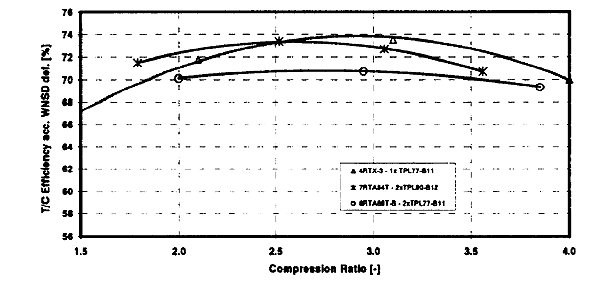
Fig.14: TPL..-B performance measured on WNSD engines
At the present time, orders for far over one hundred TPL..-B turbochargers have been received. Any reference to engine experience has to include the almost 2 million running hours accumulated by more than 1,000 TPL turbochargers, covering all frame sizes, already delivered. The first one for 2-stroke engines was delivered in 1997 and has already been successfully in service for more than 10,000 operating hours.
BACK CONTENTS NEXT