海水雰囲気中における表面被覆材の調査研究
ミカローム工業株式会社
1. 調査研究の目的
海水ポンプ、プロペラ、舵等、海水環境中で部材が摺動する機器においては、腐食の他に摩耗対策を講ずる必要がある。しかし、海水中の腐食摩耗に関する研究はほとんどなく、このため従来から実機では使用実績をもとに材料選択を行っている。この予備的研究を行った結果、(1)材料の種類により摺動中の腐食と機械的摩耗の相乗作用が摩耗損傷を拡大すること、(2)最近注目されているセラミックスコーテイング材は、耐食性はあるが膜厚が10μm以下と薄く長期間の耐摩耗性に問題があること等が分かってきた。本調査研究では、これらの研究結果をもとに表面被覆材を採用し、(1)海水中で優れた耐腐食摩耗性と低摩擦を示す表面被覆材を評価選定、(2)その損傷メカニズムを調査検討、(3)高級ステンレス鋼やTi合金に代わる安価な表面被覆材料の用途拡張を実現するため、新しい耐腐食摩耗技術の確立と舶用工業製品への実用化を目的とする。
2. 実施経過
2.1 実施項目
本調査研究では、以下の項目について実施した。
(1)海水浸漬試験
(2)往復式海水中腐食摩耗試験
(3)回転式海水中腐食摩耗試験
2.2 実施期間
開始:平成13年4月1日
終了:平成14年1月31日
2.3 実施場所
実施場所を以下に示す。
表1 調査研究の実施場所
項目 |
実施場所 |
海水浸漬試験 |
ミカローム工業株式会社 |
往復式海水中腐食摩耗試験 |
ミカローム工業株式会社 |
回転式海水中腐食摩耗試験 |
長崎大学工学部 |
|
3. 実施内容
3.1 海水浸漬試験
表2の下部ディスクの表面被覆試験片と基材のSUJ2を人工海水中に約3ヶ月浸漬し、純粋な化学腐食を調査・評価した。その結果、基材を除き、表面被覆材の腐食の程度は小さく、耐食性が良好であることを確認した。基材は腐食により試験前の表面のミクロ突起がとれて、表面粗さが平滑になっていることが観察された。
表2 試験片の材料特性及び被膜厚さ
|
試験片材料 |
硬さ(Hv) |
自然電位 |
被膜厚さ |
備考 |
(mVvs.SCE) |
(μm) |
上部球 |
Al2O3(アルミナ) |
1800 |
|
|
すべり相手材 |
下部
ディスク |
SUJ2(軸受鋼) |
200 |
-500 |
|
基材:焼鈍材 |
Niめっき |
350 |
-240 |
138 |
スルファミン酸浴 |
無電解Ni−Pめっき |
830 |
-250 |
100 |
無電解めっき浴 |
Crめっき |
1100 |
-300 |
130 |
ワット浴 |
Ni−Crめっき |
1080 |
-300 |
Cr44/Ni50 |
ワット浴 |
WC−17%Co溶射材 |
1300 |
-460 |
300 |
フレーム溶射 |
|
3.2 海水中腐食摩耗試験
海水中腐食摩耗試験は往復式と回転式の2種類のすべり摩耗試験装置を用いて実験を行ったため、下記の項目別に試験結果を報告する。
・往復式海水中腐食摩耗試験(自然電位、カソード防食電位、腐食電位)
・回転式海水中腐食摩耗試験(自然電位)
3.2.1 往復式海水中腐食摩耗試験
本試験では、すべり振幅10mmの往復すべり試験装置を使用し、試験片の片あたりを防ぐためにBall on Disk型とした。図1に示すように、参照電極は飽和カロメル電極(SCE)、対極には白金を使用し、試験電位はポテンショスタットにより制御した。上部試験片のBallは直径19.05mmのAl2O3を用い、下部試験片のDiskには厚さ5.5mm、直径40mmの表面被覆材と基材のSUJ2を用いた。なお、WC−17%Co溶射材は予備試験において表面粗さが大きく、上部のAl2O3の損傷が激しいことが確認されたので、本試験からは除外した。
腐食溶液は、300ccの3%NaCl溶液(人工海水)を使用した。試験電位は各試験片の自然電位ELP(Φn)を基準に、カソード防食電位CAP(Φn−500mV)、腐食電位COP(Φn+500mV)の3種類とした。試験後の下部試験片の摩耗量は、表面粗さ計によって測定した摩耗痕の断面積から求めた。摩耗痕部の表面生成勿の分析には、SEM、EDXおよびXPSを用いた。表3に往復式海水中腐食摩耗試験の試験条件を示す。
図1 往復すべり試験装置(試験片部)
表3 往復式海水中腐食摩耗試験の試験条件
Test piece |
Ball |
Al2O3 |
Disk |
SUJ2, Ni, Ni−P, Ni−Cr, Cr |
Normalload(N) |
30 |
Sliding speed(mm/S) |
13.3 |
Sliding distance(m) |
160 |
Amplitude(mm) |
10 |
Environment |
Solution of 3%NaCl |
Amount of solution(cc) |
300 |
Temperature(℃) |
25 |
|
図2には下部試験片別及び試験電位別の比摩耗量のグラフと摩耗痕断面を示す。比摩耗量Wsは摩耗体積を垂直荷重とすべり距離で除したもので、単位荷重、単位距離当たりの摩耗量を表す。図2より次のことが分かる。
(1) |
Ni−Crめっきを除き、いずれも下部片の比摩耗量は防食電位≦自然電位≦腐食電位の順となる。即ち、腐食電流を流すと腐食によりめっき材の摩耗が加速増大し、逆に防食電流を流すと摩耗が抑制される。 |
(2) |
実用上は自然電位での使用が最も多くなるが、自然電位ではNiめっきと無電解Ni−Pめっきが優れた耐腐食摩耗性を示し実用的である。一方、Ni−Crめっき及びCrめっきは基材のSUJ2よりも摩耗が大きく実用的とは言えない。 |
(3) |
上部片のAl2O3、の摩耗に注目すると、下部片がNiめっきのときに硬いAl2O3の摩耗が見られる。 |
次に摩耗の要因について考察すると、
(1) |
一般に「摩耗量は硬さの増加とともに減少する。」と言われているが、図3に示すように今回の試験では、めっき硬さと比摩耗量には相関関係が見られない。自然電位と腐食電位の摩耗量の傾向が同じであることを考えると、めっきの耐食性及び上部片とめっきの凝着性が今回のすべり摩耗の主要因と考えられる。 |
(2) |
Niめっきの耐腐食摩耗性がCrめっきよりも良好であった原因としては、
(1) |
耐食性がCrよりも高いこと。例えば、今回の実験において耐食性を示す自然電位がNiめっきφn=−200mV、Crめっきφn=−300mV(vs、SCE)で前者がより高い耐食性を示す。文献によると、Niのφn=−10mV、Crは不動態膜が生成すると−34mVであるが、Cr自体は−673mvで耐食性がNiより劣ることが示されている。また、Crの場合は例え不動態膜が表面に生成しても、上部片とのすべり接触で膜が除去されてCr自体が容易に海水に露出することが考えられる。これは不動態膜の生成速度とすべり速度との関係にも大きく影響を受ける。 |
(2) |
Niめっきの方がCrめっきよりも上部片Al2O3との凝着性が低いため優れた耐腐食摩耗性を示した。このことは図4の摩擦係数のグラフからも明らかである。本図に注目すると、各電位においてNiの摩擦係数めっきは0.1〜0.15範囲にあるが、Crめっきは0.3〜0.4と明瞭に高く、前者の凝着性が低いことを裏付けている。 |
(3) |
めっき浴の違いも原因の一つと考えられる。即ち、Niめっきはスルファミン酸浴を用してめっき処理を行ったが、Crめっき及びNi−Crめっきはワット浴を使用している。その電着応力を比較してみると、前者は3.5(MPa)、後者は126(MPa)とスルファミン酸浴が著しく低く、発生する内部応力も低くき裂等の損傷が生じにくい。従って、微小き裂から発生する摩耗も小さいと推定される。 |
|
(拡大画面:101KB) |
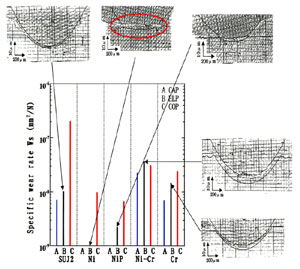 |
図2 往復すべり試験における比磨耗量と磨耗痕断面
注:CAP=カソード防食電位、ELP=自然電位、COP=腐食電位
図3 往復すべり試験における表面硬度と比摩耗量の関係
(a)at CAP
(b)at ELP
(c)at COP
図4 往復すべり試験におけるすべり距離と摩擦係数の関係
|