6−10. 改質装置の熱交換性
従来提案されている燃料改質装置は、燃料改質の触媒担体と受熱エレメントの熱流について十分に検討されていなかった。即ち、一般にはパイプの内側に触媒装置を封入し、外側に高温ガスを通すような方式の改質装置であった。この方式では受熱側ではパイプの外側から熱が伝わり、内側の触媒装置を空気などの気体を通して加熱するのでその効率はすこぶる悪い。この方式では熱通過率は20W/m2・K程度であり、非常に大きな熱通過面積を必要とする。そこで本計画では熱通過率を10倍以上に改善し、それに伴って本体の容積を大幅に減少させようとするものである。
改質装置は熱交換器の性能如何によって、大きさが大幅に異なるので、その熱交換性能を検討する必要がある。これまでに多孔質材の熱伝達率についての計算を実施し、排気ガス流速が25m/sでは熱伝達率が170W/m2・K、流速10m/sでは95W/m2・Kであることを確かめた。
大きさを出来る限り小型にするために流速25m/sになる様に通路面積を決めると、改質器の熱通過率は250W/m2・K程度となる。多孔質材を熱交換エレメントに用いると、受・放熱側の温度差が小さくなるので、排ガス側と改質側の温度差50℃とすると、CO2改質部の伝熱量55.6kWを熱交換するため必要な伝熱面積Aは次の通りとなる。
55.6×1000(W)=250×50×A
A=4.45m2
この伝熱面積をX枚のプレートでまかなうとして1枚のプレートを550mm×400mmとし、その枚数を計算するとX=20枚(改質器幅:420mm〜310mm)となる。
従って、改質器の熱交換部はプレート面積が十分満足していれば良く、改質器のエレメント部の厚さを5mm、熱交換エレメントの厚さ5mm、隔壁厚さを0.5mmとすると改質器の全幅は220mmとなる。
一方、長さ方向、高さ方向をそれぞれ450mm、250mmと小さくすると40枚必要となり、全幅は420mmとなる。
一方、水蒸気側について計算すると、伝熱量:26.7kW、熱通過率:250W/m2・k、受・放熱側温度差:50℃とし、熱通過面積を計算すると必要熱通過面積は2.13m2となり、1つのエレメント幅:10.5mmでは、プレート長さ:260mm、幅:400mm材を20枚積層する事になる。エレメント厚さ:15.5mmでは、長さ方向を200mmとする事が出来る。エレメント厚さ:10.5mmではプレート長さ:200mm、高さ:250mm、幅:420mmとなる。
エレメント厚さ |
CO2改質器 |
H2O |
全長 |
熱交換器:10mm
改質器:10mm |
長さ:550×高さ:440×幅:420 |
長さ:260×高さ:400×幅:420 |
810mm |
熱交換器:5mm
改質器:10mm |
長さ:550×高さ:440×幅:310 |
長さ:200×高さ:400×幅:420 |
750mm |
熱交換器:5mm
改質器:5mm |
長さ:450×高さ:250×幅:420 |
長さ:200×高さ:250×幅:420 |
650mm |
|
6−11. 改質装置の触媒機能について
従来の研究よりCO2 改質のSV値は10000h−1以下である事が知られている。
流入ガス量はCH4:36m3、CO2:56m3、合計:92m3であるので、必要な触媒容積は、0.0092m3である。
熱交換器として検討したエレメント厚さ:5mm×450mm×250mm40枚での触媒容積は0.0225m3でSV値の2.5倍となり、触媒量は十分な値を持ち得る。
逆にこの触媒装置ではSV値を4000h−1 まで小さく出来る可能性がある。
H2O改質器の容積は従来用いられているSV値が115000h−1であるので、メタン流量とH2O流量をそれぞれメタン:18m3、H2O:38m3とすると、触媒は4.9×10−4m3が必要量であり、熱交換器で求めた触媒容器の大きさが0.01m3であるので、約20倍と大きく、触媒装置としては十分な大きさである。逆に触媒のSV値は5750h−1まで小さく出来ることになる。
6−12. まとめ
連続式改質装置を成立させるために種々の検討を実施した。本改質装置は出来るだけコンパクトに製作したい、エネルギーの有効活用を図りたい、改質効率を向上させたい、機能を簡素化したい、等の要求特性を満たすための検討を進めた。その結果以下のことが判った。
(1) |
改質装置を出来るだけ簡素化させるためにはCO2の吸着、離脱装置を2個並列に並べ、改質装置は連続作動させるように単一容器とする方法が望ましいことが判った。そこで以下の項目では上記装置を前提に検討した結果を述べる。 |
(2) |
CO2を排気ガスから吸着するためには吸着、離脱の2つの動作を反復させなければならず装置の2連化が必要である。 |
(3) |
CO2の吸着のためにはCO2
吸着材の量が吸着器の大きさを決め、吸着のサイクルを3〜5分に設定するとその吸着器全体の大きさは長さ460mm×幅250mm×高さ300mmとなる。 |
(4) |
CO2改質装置の大きさは熱交換器の隔壁面積で決まり、最小に設定出来ても長さ450mm×高さ250mm×幅420mmとなる。この時、SV値は4000h−1と、極めて小さな値となり、性能の向上が期待できる。 |
(5) |
H2O改質器の大きさは熱交換器の隔壁面積で決まり、最小大きさで長さ200mm×高さ250mm×幅420mmとなる。この時、SV値は5750h−1となり、通常値の1/20となる。 |
(6) |
CO2吸着は350℃〜500℃ほどで化学反応させ、700℃で離脱させる。吸着時間は4分ほどで離脱は温度上昇に40秒、離脱に3分ほどの時間を要する。 |
(7) |
排気ガスの熱エネルギーは改質装置の作動に十分でなく、必要に応じてタービン仕事の一部の熱を回すことになる。 |
(8) |
改質装置の構造は平板の両面に多孔質材を溶着させ改質層側はアルミナコーティングと改質触媒を付着させ、熱交換側は銅、銀等のメッキを行うと効果的である。 |
(9) |
改質層側は2つの多孔質板を重ね合わせ、隔壁を延長させて包みこむ箱型構造とし、改質ガスはこの密封箱の中を行き来する。 |
(10) |
CO2離脱サイクルで必要とされる昇温熱は排気ガスの吸着時に排気ガス側に流入するが後流にある熱交換器で利用されるので損失にならない。 |
(11) |
改質装置の最小大きさは長さ1500mm×幅575mm×高さ400mmに納まる。 |
以上の設計検討を基に設計図面の作成を行った。本設計図面は従来の回転式と異なり、バルブ切り替え式改質器とした。図面の概要構造について下記に説明する。(図6−7)
1. |
排気ガスは熱回収タービン装置より出て、CO2吸着、離脱装置II側の集熱エレメントを通り、高温の熱エネルギーを伝熱し、ジルコニウム酸リチウムのコーティング層に熱を移動させ、CO2
の吸着された多孔質体からCO2を分離させる。 |
2. |
CO2吸着器を出た排気ガスは燃料改質装置の排気ガス通路側に流れ込み、改質により熱エネルギーを奪われ、改質装置の下流から流出し、逆流してCO2吸着装置I側のCO2吸着層側に入る。CO2吸着が終了した排気ガスは改質装置の出口に流れ、熱交換器に流れ出る。 |
3. |
CO2吸着装置IIの吸着層側ではCO2が分離され、充満しているのでCO2導入弁が開放され、遠心ポンプによりCO2が改質装置の上流側に流れ込む。 |
4. |
CO2流入部にはCNG導入口が設けられていて、CNGも同時に改質触媒層に流れ込み、改質反応が進行する。 |
5. |
改質装置では排気ガス通路から移動してきた熱流により改質が進行し、下流に設けられたH2O改質層に未反応CNG、CO、H2、CO2の混合ガスが移動する。 |
6. |
H2O改質装置には300℃程に過熱された水蒸気が導入され、未反応CNGと触媒の作用により反応し、改質される。 |
7. |
改質された燃料の成分は未反応CNG、CO、H2、CO2、H2Oの混合体としてエンジン側に送られる。エンジンでは吸気管を通ってホモジニアス混合気としてシリンダーに供給される。 |
8. |
CO2吸着器の動作は所定時間毎に排気ガス導入弁の作動によって切り替えられる。 |
以上の動作によって燃料は連続的に改質される。
(拡大画面:85KB) |
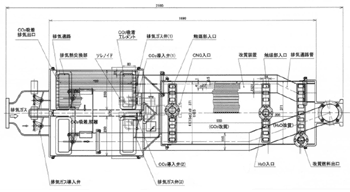 |
図6−7 CNGの連続改質装置の設計図
|