4.2 材料の破損の法則
1)静荷重のもとにおける破損
材料の破損の定義は、その機器の使用目的によって異なる。形状の変化が許されない場合には応力が降伏応力に達したところで破損が始まると考えるべきであろう。しかし、多少の変形は問題ではなく、とにかく破断しなければよいというのなら、応力が抗張力に達するまでは破損しないと考えてよい。機器の設計に当たっては、外力の見積もりの不確かさや材料の不均一性などの不確定要素を吸収するために、安全率というものを考え、基準強さを安全率で割った許容応力、すなわち、許容応力=(基準強さ/安全率)、を使用する。基準強さには、降伏応力、抗張力あるいは後に述べる疲労限度などのうちから、目的に応じた選択を行う。
軟鋼やアルミ合金のような工業材料は、破断するまでに大きい塑性変形を伴うのであって、このような材料は延性材料と呼ばれる。他方、鋳鉄のような材料は脆性材料と呼ばれ、破断までにほとんど塑性変形を伴わない。しかし、軟鋼のような延性材料でも、たとえば、極めて低温の環境においては、脆性破壊を示すことがある。したがって、延性材料とか脆性材料とかいう分類は本質的なものでないことに注意すべきである。
さて、軟鋼のような延性の材料では、すべり面における相対的な変位によって塑性変形が生じ、さらにすべり面の分離によって破壊に至ることから、最大せん断応力が材料固有の一定の値に達すると最大せん断応力面で破損が起こると考えてよい。すなわち、延性材料にたいしては、最大せん断応力が基準になる。これにたいして、鋳鉄やガラスのような脆い材料では、塑性変形をほとんど伴わずに破壊に至る。この場合は、最大主応力が材料固有の強度、すなわち、抗張力に達すれば、最大主応力面で破断することが知られている。このように、脆性破壊においては最大主応力が基準になる。脆性破壊において破壊に費やされるエネルギは、延性破壊のそれにくらべてはるかに小さい。以上より、延性材料および脆性材料の丸棒が引張りを受ける場合の破断の様式は補・45図に示すようになることがわかる。同様に、それらが捩りモーメントを受ける場合の破断の様式を補・46図に示す。
補・45図 引張り力をつける丸棒の破壊
(拡大画面:14KB) |
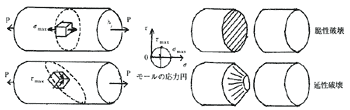 |
補・46図 ねじリモーメントをうける丸棒の破壊
(拡大画面:16KB) |
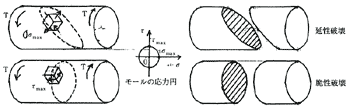 |
現実の機器には、多くの場合、孔、キー溝、フィレット、切り欠きといった形状的な不均一性が存在する。このように形状が不連続的に、あるいは急激に変化する所では応力集中が起こる。たとえば、無限遠方で一様な応力σを一方向に受けている無限平板中に、引張り方向に垂直に長径2aを持つ楕円孔が存在する場合、楕円の長軸を延長した線上の応力の分布は補・47図に示すようになり、その最大応力σmaxは次式で与えられる。
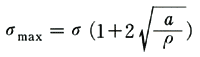 ・・・(14)
ここで、ρは楕円孔先端の曲率半径である。また、次式で与えられる係数αを応力集中係数という。
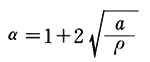 ・・・(14)
円孔の場合には、a=ρ〔mm〕であるから、応力集中係数は3となる。
補・47図 楕円孔の応力集中
(拡大画面:24KB) |
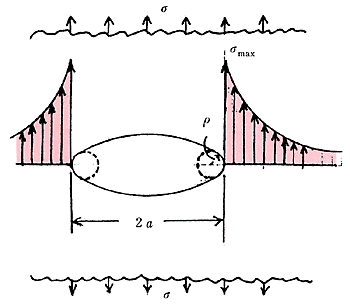 |
2)疲労およびクリープによる破壊
静的な応力としては降伏応力以下の値であっても、その応力を長期にわたって繰り返し受ける事により機器が破壊に至る事がある。これを疲労破壊という。平均応力σmの両側に応力振幅σaで繰り返して負荷を与える疲労試験を行い、試験片が破壊したときの繰り返し数を横軸に、応力振幅を縦軸にとってプロットした線をS−N線図という。鋼材にたいしては補・48図に示すように、右下がりの傾いた線と水平線とからなる場合が多い。この水平線より下の応力ではいくら繰り返しても破壊は起こらないのであって、この水平線にあたる応力σwを疲労限度という。傾いた線が水平線に移る限界の繰り返し数はおよそ107回といわれている。しかし、材料によって、また、環境によっては疲労限界が存在しない場合がある。
金属材料が高温で長時間一定の引張り荷重をうけると、補・49図に示すように、ひずみは、時間とともに始めは急速に、次に一定のひずみ速度で、最後に再び急速に増加にて、ついには破断にいたる。このように一定の荷重のもとで時間と共にひずみが増加する現象をクリープという。
補・48図 S−N線図
補・49図 クリープ曲線
3)フラクトグラフィ
機器が破壊した場合、その破面には破壊の様式に特有な幾何学的模様が残されている。この模様から破壊の様式やその原因を調査する方法をフラクトグラフィという。破面を観察する手段としては、肉眼、虫眼鏡、金属顕微鏡から電子顕微鏡にいたるあらゆる観測手段が利用される。
まず、脆性破壊を起こした破面には、ヘリングボーン(鰊の骨)パターンあるいはシェブロン(山形)パターンと呼ばれる模様が亀裂伝ぱ方向に形成される場合が多い。その一例を補・50図に示す。
延性破壊においては、すべり面の分離や微小空洞が合体して破面が形成されるが、微視的には、補・51図に示すような、ディンプルと称する多数の微少な窪みが観察される。
最後に、疲労破壊では、亀裂の進展の過程における荷重の変動によって、補・52図に示すように、ビーチ・マークと呼ばれる貝殻状の縞模様が現れる場合がある。
補・50図 鋭い隅部(矢印)から発生した破壊のジェブロン・パターン
Fracture initiated at the location indicated by the arrow, where the corner of a snap-ring slot was specified to have a zero minimum radius. Fracture surface is that of a forging of AMS 6434 (vanadium-modified 4335) steel that was heat treated to a yield strength of 190,000 psi.
Fig. 3. Fracture surface exhibiting a chevron pattern (at left) pointing toward
fracture origin, at a sharp corner. |
補・51図 引張りで破断した1020鋼のディンプル、大きいディンプルは更に小さいディンプルを含む
Fig. 2. Equiaxed dimples on the flat-face fracture of 1020 steel specimen broken in tension. Note large dimples than contain smaller dimoles. (SEM fractograph; 100×) |
補・52図 連続して進展して行くき裂面の位置を示すビーチ・マーク
Fig. 17. A classic fatigue-fracture surface, showing progression marks (beach
marks) that indicate successive positions of the advancing crack front. (J. Schijve) |
補・50、51、52図は
METALS HANDBOOK,Vol.10 Failure Analysis and provention Editor,Howard E.Boyer,8th Edition 1975
AMERICAN SOCIETY FOR METALS
による。
|