2. OIL CONTROL RINGS
Flexible chromium plated profile ground oil control ring designs are now used in medium speed engines without exception. The coil spring backed oil ring has proved to be the best technical solution because of the following properties:
- a high degree of flexibility and thus conformability,
- a flat spring characteristic, ie a small decrease in wall pressure during wear,
- uniform oil film distribution over the cylinder,
- wide choice of radial pressure - reduced secondary wear by the use of centerless ground springs
The land width tolerance has been halved since introducing profile grinding of the lands (Fig 10), which significantly reduces the spread in wall pressure and oil consumption. The ring lands are chromium plated and the springs machined by centreless grinding to increase life; the specified wall pressure lies between 0.5 and 1.5 MPa. For high life time demands chrom ceramic lands have shown excellent results.
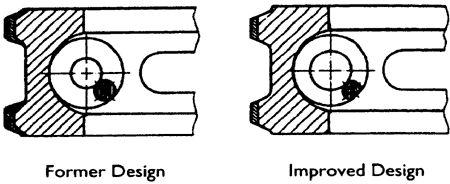
Fig. 10 Improvement of Coil Spring Backed Oil Control Ring by Profile Grinding
3. RING MATERIALS
3.1 Base Materials
The most usual base material for the top compression ring is an unalloyed flake cast iron (designated LP7), but when greater strength is needed, for example for very high peak pressures in gas engines, ductile iron (designated KV 1) satisfies all require-ments; standard cast iron is used for the other rings. Alloyed cast irons (eg F 14) are available for special applications, for example in chromium plated bores, but steel is not used at all for rings in medium speed engines. The mechanical properties and microstructures are shown in (Table 11) and (Fig 12).
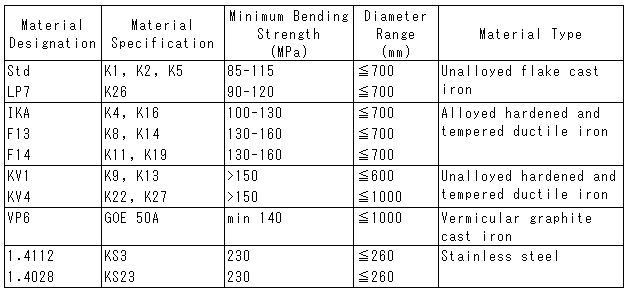
fig. 11 Mechanical Properties of Piston Ring Materials
3.2 Coatings
The base material must be protected on the running surfaces by a wear resistant coating in order to survive the hostile operat- ing conditions encountered in medium speed engines. Electro-deposited hard chromium coating is generally preferred, unless scuffing necessitates the use of HVOF or ceramic coatings.
3.2.1 Chromium Coating
In the tribological piston ring/cylinder wall system, hard chromium coatings on ring peripheries are noted for their high inherent wear resistance and the low generation of cylinder wear, so long as the thermal and/or mechanical loading does not exceed certain limits. If these limits are exceeded the formation of the oil film between the piston ring and the cylinder wall can become critical, in which situation adhesive wear (scuffing) and/or fa-tigue related spalling (the 'peel and polish' phenomenon) can take place.
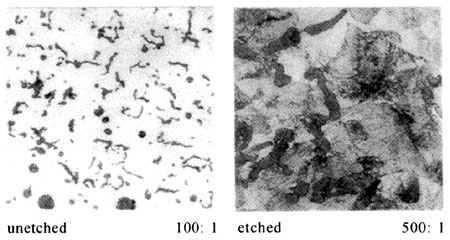
fig. 12 Microstructure of Piston Ring Materials
Scuffing occurs predominantly in the running-in phases, so AE Goetze have developed special surface topographies, par-ticularly the special lapped surface finish, which improve oil film formation during running-in and shift the application limit for chromium plated ring towards higher loads (Fig 13). Special lapping is particularly effective in raising the scuffing threshold.
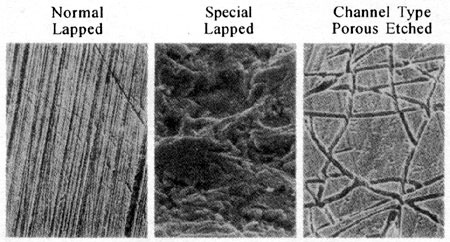
Fig. 13 Topographies of Chromium Plated Peripheries
3.2.2. Chromium-Ceramic Coatings CKS 36
Further development of chromium coatings has been pur-sued with the object of extending the application of chromium into more hostile operating conditions and/or extending the ser-vice life. The new chromium-ceramic coating CKS 36 meets these requirements for the full thickness of the coating [5].
Firmly embedded in the CKS 36 coating, throughout its whole volume, are ceramic particles (aluminium oxide) which confer a superior loading capacity and wear resistance to the coating. A schematic diagram of the structure of CKS 36 is shown in (Fig 14), which illustrates the repetitive process steps consisting of chromium deposition, opening of the micro-crack network, inclusion of the ceramic particles, embedment of the ceramic particles, closing of the micro-cracks and build-up of the next layer of the coating.
BACK CONTENTS NEXT