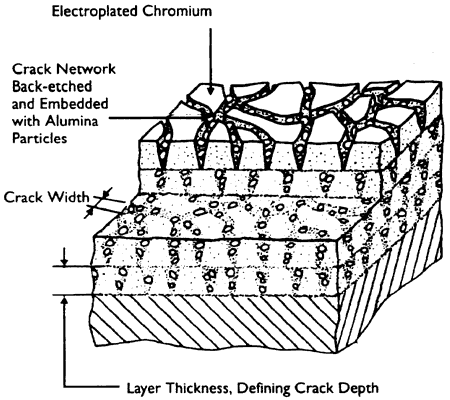
fig. 14 Structure of Chromium-Ceramic Coating CKS 36
The wear behaviour of the chromium-ceramic coating is su-perior to that of conventional chromium by a factor of at least two, while the cylinder wear is only marginally higher than the low values produced by conventional hard chromium coatings. The higher loading capacity of the chromium-ceramic coating is demonstrated in (Fig 15). Both coatings were tested in scuff-prone engines normally equipped with molybdenum or plasma sprayed rings.
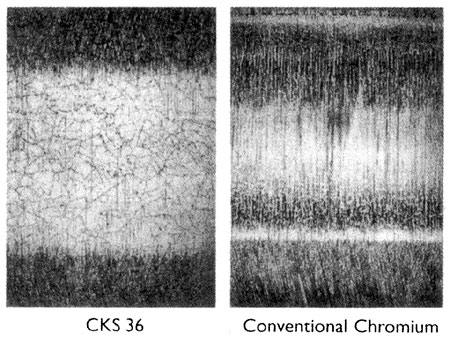
Fig. 15 Surface Appearance of the Chromium-Ceramic Coating CKS 36 after 100 hours Hot Test
Scuffing is clearly visible on the conventional chromium coating, whereas the chromium-ceramic coating shows only faint signs of scoring.
Since the relatively recent introduction of rings with the CKS 36 coating, more than 50 engine approvals have been obtained with such rings in the top groove, which are now in series pro-duction for bore sizes between 165 and 640 min.
It is interesting to report that CKS 36 rings have successfully displaced plasma sprayed rings in many engines.
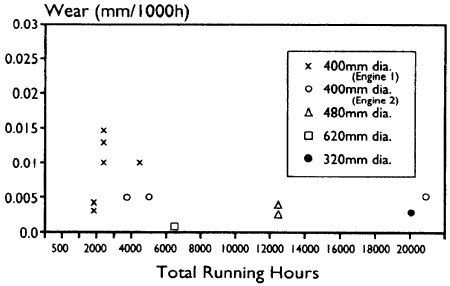
Fig. 16 Wear of CKS 36 Rings in Heavy Fuel Operation
Typical wear values in heavy fuel operation are plotted in (Fig 16) and a direct comparison with plasma sprayed coatings is shown in (Fig 17).
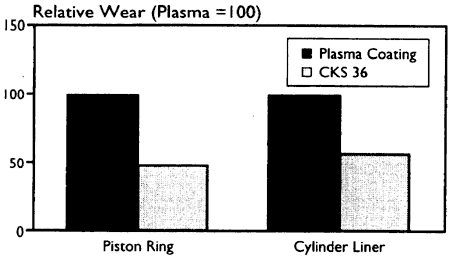
Fig. 17 Comparative Wear of Plasma Sprayed and CKS 36 Rings in Heavy Fuel Operation
Further results from MAN, showing wear results with the CKS 36 coating in a field test, are summarised in (Fig 18).
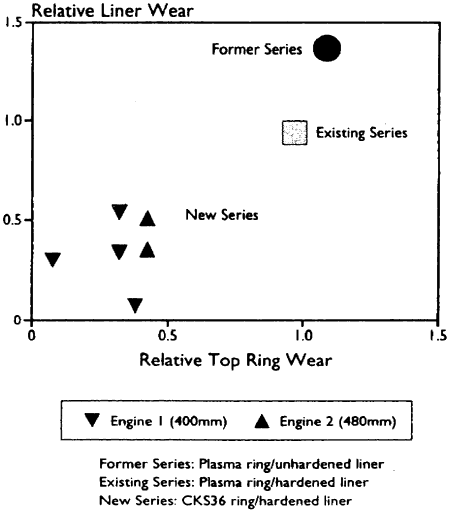
Fig. 18 CKS 36 Ring Wear Results in Field Tests
(Reproduced with permission of MAN B&W)
BACK CONTENTS NEXT