In response, as shown in Fig.8, the current turbine blade angle in MET turbochargers has been changed to provide greater surface area. Blade shape is the same as for the turbine blades used in the former MET-SE model turbocharger, which has established an extensive performance record. The effect on the vibratory strength of the blades induced by this change in angle was considered by means of 3D FEM calculation, and it was confirmed to be virtually unchanged. Thus, turbine blade reliability is demonstrated by the performance record of the many MET-SE model turbochargers in operation.
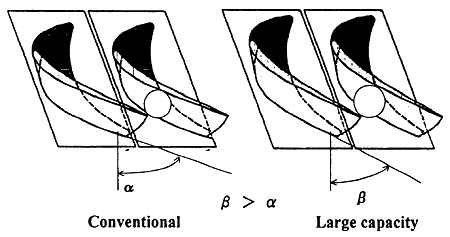
Fig.8 Conventional and large capacity turbine blades
Turbine capacity and rotor thrust force are compared in Fig.9 for conventional turbine blades and large capacity blades. The numbers 5, 6, 7, and 8 indicate nozzle size, with an increase of 1 representing a 4% rise in turbine equivalent area. Comparing a conventional turbine blade (K) with specifications for the same reaction, the large capacity turbine blade shows capacity expansion of approximately 14%.
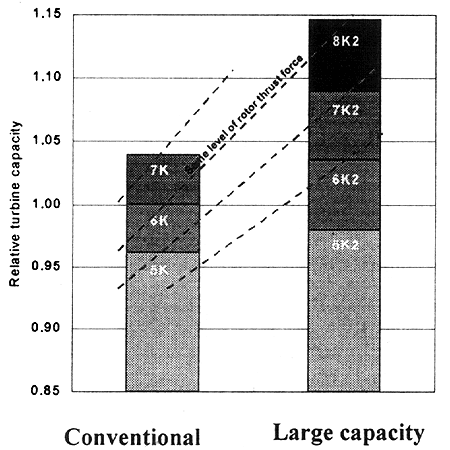
Fig.9 Turbine capacity and rotor thrust force
3.4 Rotor
The structure of the torque transmission portion is illustrated in Fig.10. Rotor shaft torque increases with expanding turbine capacity.
Torque from the turbine is transmitted via the interfit between the claw clutch and the friction force provided by the impeller wheel clamp between the sleeve and the impeller wheel. In order to increase transmittable torque and to obtain sufficient play with respect to the increased torque, the number of claws for the new large capacity turbine was increased from two to four in comparison with conventional models.
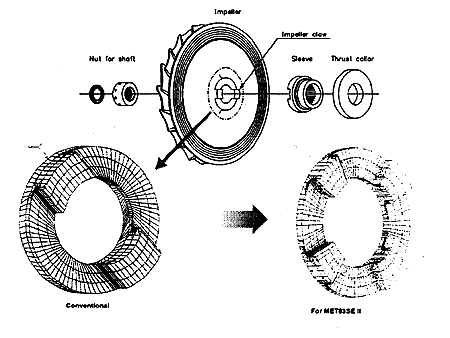
Fig.10 Rotor shaft torque transfer
3.5 Tachometer
In place of the conventional rotation detector consisting of a magnet attached to the end of the shaft and an electromagnetic pickup, a change was made to an eddy current gap sensor with accompanying calculation of the number of impeller blades. This is illustrated in Fig.10. The new method eliminates the need for a support to secure the conventional electromagnetic pickup, thereby reducing exciting force on the compressor impeller blades.
BACK CONTENTS NEXT