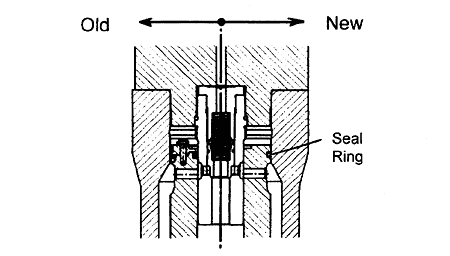
Fig.5 Modification of Seal Ring
The gas injection valve (Gas valve) is very reliable. The experienced trouble (three times) was combustion gas leakage through the seat between the gas valve and the cylinder cover. By applying an adequate grinding tool to the seat, this was solved.
3.2 Cylinder condition
Due to the sulphur-free fuel (both gas and oil), we were concerned about the matching of fuel type and lube oil characteristics to ensure a good cylinder condition. In the first operating year (1994) we experienced scuffing problems 10 times. Many cylinder oils - of four different brands and with TBN numbers between 10 to 70 - were tested and finally a TBN 40 was selected irrespective of cylinder oil brand. Since then, the scuffing problem was reduced remarkably as shown below:

As can be seen, still from time to time scuffing appears sporadically. However, we expect that this will be completely solved by introducing Piston Cleaning Rings, which are today standard for big size MC-engines. The cause of scuffing appears to be deposits from burnt cylinder oil on the piston top land that wipes off the lube oil and thus may destroy the oil film on the sliding surface.
Apart from the sporadic scuffing problems, the general cylinder condition is very good. Cylinder liner wear rate and piston ring wear rates are shown in Fig.6. The average liner wear rate is 0.039 mm/1000 hrs and the piston ring (normal uncoated piston ring) wear rate is 0.065 mm/1000 hrs. This is much lower than typical data of normal marine engines (average liner wear rate 0.06 mm/1000 hrs and piston ring wear rate 0.25 mm/1000 hrs).
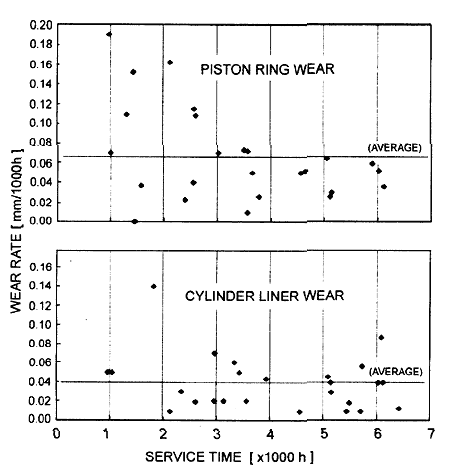
Fig.6 Wear Rate of 12K80MC-GI-S
3.3 Gas compressor
The gas compressor is a 4thstage reciprocating compressor driven by an electrical motor (1,650 kW). The total running hours was 13,600 hours at the end of March 2000.
The lower pressure stages from 1 to 3 have had no trouble at all. At the 4th stage we have experienced following troubles: Excessive piston ring wear was experienced at 1,400 service hours. Since then, the piston ring design and material was changed, and a lifetime of more than 6,000 hours was obtained.
Stuffing ring also had excessive wear at 2,000 service hours, but after a material change, more than 10,000 hours life time has been obtained.
O-ring breakage was also experienced. The lifetime was 1,200 hours but after a material change 2,000 service hours has been obtained. The 4th stage (highest pressure) section of the gas compressor is shown in Fig.7. The obtained performance is shown in Table 3.
Table 3 Gas Compressor Performance
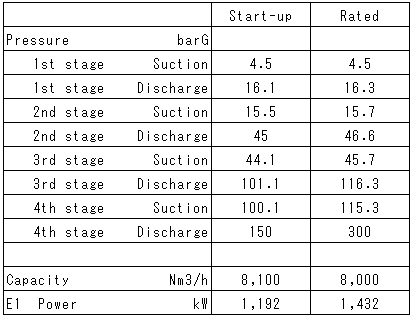
4. DeNOx SCR SYSTEM
The environmental conditions for the plant were defined in a 'Detail agreement to protect environment' among Chiba prefecture, Ichihara city and Mitsui Chiba works. This deals mainly with emissions of SOx, NOx and dust. The plant is equipped with an SCR system for NOx reduction, while there is no need for additional equipment in order to reduce SOx and dust because those values in GIDE are essentially much lower than the regulation values.
BACK CONTENTS NEXT