Further improvements in fuel consumption have been obtained by increasing fuel line pressure so that the fuel can be atomized, evaporated, mixed with air and burnt in a much shorter time period without increasing smoke or particulates. Unit injectors provide a high mean fuel line pressure without an increase in maximum pressure. However they are unlikely to be adopted on future marine diesel engines because of the high cost of a very high level camshaft and the unacceptable flexibility of a long valve train with a low level camshaft. The common rail system, which also has a high mean pressure for a relatively modest maximum pressure, is a better approach and this will be adopted on more engines as the FIE manufacturers continue their development. Maximum fuel line pressures of 1600 bar are now relatively common and increased pressures will be used in the future.
Improved turbochargers can claim credit for continued improvement in fuel consumption and they have made increases in BMEP possible without resort to two stage turbocharging. We can now expect further improvements using variable geometry turbochargers and variable valve timing.
4. THE DEMAND FOR REDUCED COST
The market price of medium speed engines has been reducing and in some areas the price reduced by as much as 20% in a single year. The main reason for this is over-capacity in the engine industry and hence increasing competition. As a result manufacturers have been making lower profits but some have also been very successful in reducing manufacturing costs.
Some 80% of the cost of an engine is in 20% of the components. The cost of these can mostly be affected at the design stage. Today's engines are made up of fewer components as a result of standardisation and of combining the function of various components. Subassemblies [8] or completely integrated front ends as shown in figure 9 [9] can reduce cost but also provide a more leak and trouble-free design. Flexible machining centres are now commonly used to produce most major engine components. These save cost, reduce batch quantities and aid the just-in-time principle. Furthermore, where subassemblies can be supplied complete to the engine erection shop, then engine assembly times and costs can be reduced.
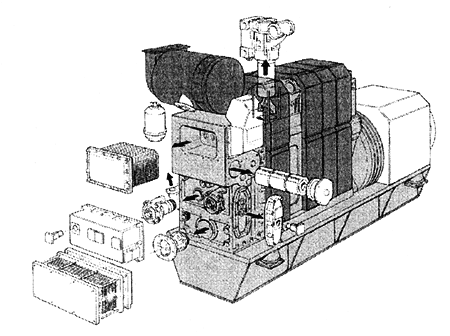
Figure 9 - Integrated front end
Another area where cost reductions are being made is by designing engines wherever possible for a single market. This can give a cost and performance advantage over competitors in the chosen market. This can more than compensate for the fact that the engine is somewhat less competitive in other markets.
As a guide figure 10 shows a typical break-down of component costs for a medium speed engine.
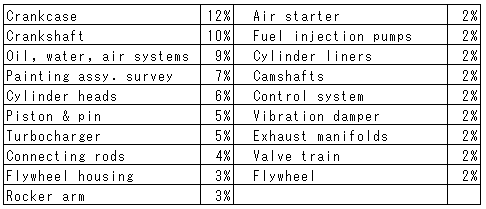
Figure 10 - Typical cost breakdown of heavy fuel engine
Development costs have also been reduced in real terms as a result of improved computer aided design and computer aided engineering. Many engines are designed today in 3D. This is slower during the initial stage, but it can reduce time and cost considerably during subsequent stages of finite element mesh generation, CFD cooling and combustion studies and in application engineering. The cost of assembly drawings and parts and instruction manuals is also considerably reduced because use can be made of this library of 3D design files.
5. THE DEMAND FOR REDUCED EMISSIONS
2000 is the first year in which all marine engines have in effect had to comply with emissions regulations, though manufacturers have been working on this issue for many years because of regulations for stationary engines. NOx reduction is covered elsewhere in this conference but we should consider the effect that this legislation will have upon the use of heavy fuel. The main consideration is SOx and particulates. In regions of heavy traffic close to land such as the English channel, the Baltic sea and Tokyo bay there is concern about sulphur emissions from ships and there is pressure to reduce them. Since it is not really economic to remove the sulphur from residual fuel, ocean-going vessels may be forced either to install scrubbers to remove it from the exhaust or to switch to MDO in certain waters. The effect of exhaust particulates on human health is still not fully understood [10] but, since particulates from ships are generally deposited into the sea within a short distance, it is hard to see that these will be a major problem off-shore. The type of HFO has a much greater effect on particulates than on NOx, HC or CO, as is shown in Figure 11 [11]. If particulates do become a matter of serious concern there may be some justification in banning certain types of HFO but not to ban its use altogether.
BACK CONTENTS NEXT