A major leap forward was made by using the fire ring or anti-polishing ring. The concept of a smaller diameter ring at the top of the liner being installed to remove the carbon from the crown goes back some 30 years but it is only in the last five years that it has become almost universally adopted by the medium speed HFO marine engines. By removing the carbon the problem of bore polishing is largely overcome so that the liner retains its honing pattern and its oil film. Thus, wear is reduced and so is the likelihood of piston scuffing but a dramatic improvement is also made in the lubricating oil consumption. Figure 2 shows an illustration of a fire ring and its method of operation.
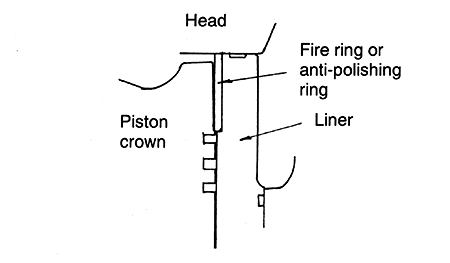
Figure 2 - Fire ring serves to remove carbon from piston crown
Another major cause of reduced ring and liner life was cold corrosion caused by the sulphur in the fuel. It is not economic to remove sulphur from the fuel but, once the mechanism had been understood with the amount of the sulphur products depending upon cylinder pressure, then solutions could be applied. Previously all efforts had been made to reduce ring and liner temperatures to improve ring life but then it was realised that the temperature must be kept above about 180℃ if this problem were to be avoided. Figure 3 shows the obvious but difficult balance which must be maintained between oil consumption and the additive reserve which controls the alkalinity of the oil that combats corrosion [2].
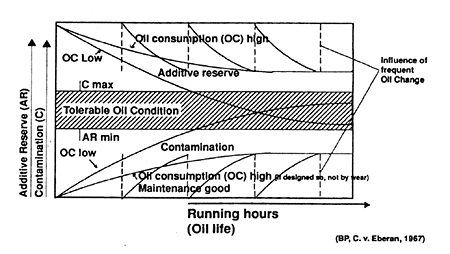
Figure 3 - Balance between oil consumption additive reserve and contaminants (CIMAC No/3)
Each of the above steps has improved ring and liner wear but engine designers have made other changes. Chrome ceramic piston ring coatings are very widely used to reduce both wear and scuffing while nitrided or laser-hardened liners have played their part, too [3]. Furthermore finite element techniques have shown us how to design cylinder bores which are nearer to the true cylindrical shape when they are in the running condition and have shown that it is not necessary to cool the liner much below the position of the ring pack at top dead centre.
Measurements and calculations of the oil film thickness between the ring and liner have made it easier for us to optimise the ring pack. Figure 4 shows the oil film thickness left on the liner by the ring pack. The film thickness between the top ring and the liner is about double this value. It can be seen that the hydrodynamic film provides a healthy thickness for much of the stroke but squeeze film conditions operate at top and bottom dead centre, so these are the critical wear points. If the film thickness is maintained to a suitable level then it has been found that chrome ceramic rings running against an unhardened liner will provide a very adequate life.
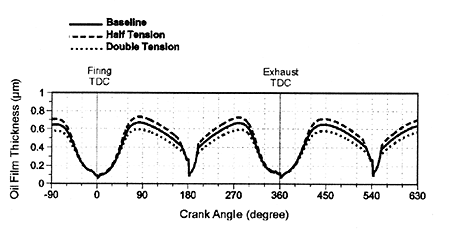
Figure 4 - Thickness of oil film left on liner wall of diesel engine - variation of ring tension at oil ring
2.2 Crankshaft and bearings
Another cause of concern has been that hard particles become embedded in the bearing material and provide an abrasive action against the crankshaft, thus causing it to wear. The traditional solution of thick soft overlays was only effective for lower bearing loads. With the drive to reduce engine size and cost engines were designed with higher bearing loads so overlays of any significant thickness started to suffer failure by fatigue. A considerable improvement has been made by providing a soft layer which is supported by a harder layer [4, 5] so that wear can be reduced even with highly loaded bearings carrying thin oil films (fig. 5). It is equally possible to design an engine with thicker oil films but this invariably involves a size and engine cost penalty.
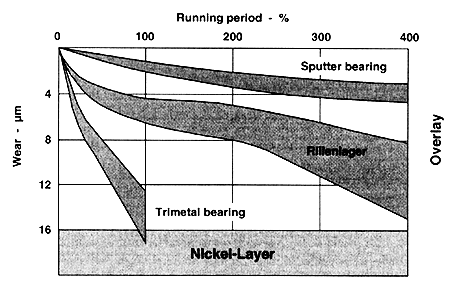
Figure 5 - Wear results of three different bearing materials
2.3 Exhaust valves
Perhaps the most frustrating problem for HFO medium speed engines was the failure of exhaust valves. The symptoms of guttering, blow-by, head overheating and eventually valve breakage delighted the turbocharger manufacturers because the turbine at least had to be replaced because the smaller parts had passed through the nozzle ring and damaged the wheel.
BACK CONTENTS NEXT