目的の関数は重量で、拘束するものは、DNV規則(1995年)による最大許容応力であった。最適化する変数は、外板の厚さ(t)、高さ(h)、リングの厚さ(tr)及びリングフレーム間の距離(L)であった。
最適解は142kg/mの重量で、その時、Lは0.11mであった。しかし、0.11mという値は、技術的及び経済的にあまりにも小さすぎるので、Lの最小値を0.29mと設定して、新しい解を求めた。結果として、164kg/mという満足すべき重量が得られた。最終形状は、種々の部位に対する応力集中をチェックするため有限要素法で解析された。
組立工程は、チタンの持つ高反応性及び選定された合金(6Al-4V)の持つ高強度性が形成工程を困難にさせるため、製作者と一緒に注意深く検討された。半球状のドームは熱を加えた状態で形作られ、それから、表面の不純物を除去するために反転された。円筒部はチタンの薄板を冷間圧延し、その後、電子ビーム溶接で長さ方向に溶接することで製作された。リングは薄板から切り出し、機械加工を施した後、TIG溶接を行った。全ての溶接部はX線にて検査された。
4] 電力
最初の海上試運転においては鉛電池が使用されるように計画されていたが、本ビークルのミッションでは最長の航続距離が要求されるため、これに関連して、高性能のバッテリーが要求される。ビークルに中立浮力を与え、バッテリーを格納する耐圧部の寸法を決めるために、プロジェクトの初期段階からこれらの重量及び容積の推定が行なわれた。
単純化のために、前述の要求事項を満足しつつ、一定速度U=2m/sで、航続距離250kmのミッションが仮定された。
船体抵抗は下記で表される。
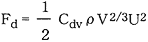
ここに、ρは水の密度、Cdv(=0.03)はGranville(1976)により得られる低抗係数、V(=2.2m3)はビークルの体積である。要求されるエネルギは下記の式で求められる。

ここに、Pは平均負荷電力(ペイロード+電子機器)で280Wと推定され、ηは推進システムの全効率で0.5と推定され、結果として、25kWhの高性能バッテリーが必要であることになった。
経済的理由で1次バッテリーは省略し、銀-亜鉛の2次バッテリーがコストと性能の面から選択された。製造者は32個の電池を直列につなぎ、48V、平均660Ah(電力)として32kWh相当)とすることを提案した。このパッケージの重量は約2000Nで、耐圧部の容積の半分を占め、十分納まることが分かった。