DEVELOPMENT OF A HYDRATE-BASED NATURAL GAS TRANSPORTATION SYSTEM
Toru Iwasaki, Yuuichi Katoh, Takashi Arai, Kiyoshi Horiguchi and Kazuyoshi Matsuo
Mitsui Engineering and Shipbuilding Co., Ltd.
Ichihara, Chiba, JAPAN
iwasakir@mes.co.jp
ABSTRACT
Natural Gas hydrate can contain a lot of gas in it and its production, transport and storage can be made under milder thermal condition than that of LNG. Mitsui Engineering & Shipbuilding Co., Ltd., utilizing such characteristics of natural gas hydrate, is now developing an integrated system for its production, pelletizing, storage, ocean transporting, and gasification. This paper describes the results of our experiments with methane hydrate to verify each component technology such as production, pelletizing, storing and gasification technologies. Through various experiments with such component technologies, the feasibility of the transport system of natural gas hydrate has been confirmed.
INTRODUCTION
Natural gas usage continues to grow in response to the need to cope with global environmental issues while securing a convenient and stable source of energy. Currently, the long distance ocean transport of natural gas to consumer markets is achieved by an integrated Liquefied Natural Gas (hereinafter called LNG) system. However, this system needs huge capital investments for LNG production facilities, LNG carriers and so on, which are economic only with very large-scale gas fields. Accordingly, the development of a simpler, lower cost natural gas transportation system is strongly required to meet the growing worldwide demand for natural gas.
Natural Gas Hydrate (hereinafter called NGH) is a solid substance resembling ice, which sometimes clogs natural gas and crude oil pipelines. Although previously regarded as a nuisance, NGH has been found to have unique characteristics that make it a good candidate as a storage and transport medium for natural gas. In particular, it can be easily made at rather high temperatures compared with LNG and it can contain gas about 160 times its volume. Based upon these characteristics, Gudmundson, Norwegian University of Science and Technology et al published a paper in 1996 introducing a natural gas transportation system based on powdered NGH. The paper reported on the artificial production of NGH using natural gas and water and the storage and transportation of powdered NGH across the sea at a temperature of -15℃elsius. This system results in cost reduction of about 24% compared with the conventional LNG system, especially in terms of the capital investment required.
On the basis of the results reported in the above-mentioned paper, Mitsui Engineering & Shipbuilding Co., Ltd. (hereinafter called MES) is now developing its own high volume, long distance NGH-based natural gas transportation system. The development of the system's process component technology has now reached the stage of concept demonstration using a continuous process pilot plant. This paper introduces the results obtained with each component process such as production, pelletizing, storage and gasification of NGH, which together will compose one continuous system of NGH transportation.
CONCEPT OF AN NGH-BASED NATURAL GAS TRANSPORTATION SYSTEM
Figure 1 shows the NGH-based long distance, bulk natural gas transportation system now being developed by MES. The special feature of this system is the use of compressed powdered NGH pellets for transportation and storage of natural gas. In this system, powdered NGH with particle sizes of dozens of μm - several mm is pelletized into spheres of dozens of mm in diameter. Pelletizing increases both the bulk density of NGH and the packing efficiency during storage in comparison with powdered NGH. Pelletized NGH also has superior fluidity, and therefore its compaction and adhesion decrease, making its handling much easier and enabling time savings in handling for storage on land and in the cargo holds of ocean going carriers. Furthermore, the remarkable reduction in the specific surface area of the pelletized NGH (when compared with that of powdered NGH) is expected reduce the amount of gas dissociation during the storage. In the transportation system (Fig.1), the natural gas extracted from the gas field is processed to remove the interfused sour gas and later mixed with water to produce NGH. After dewatering, the NGH is pelletized by a pelletizer before being temporarily stored in a tank before being loaded into the storage tanks of a bulk carrier.
On reaching its destination, the pelletized NGH is unloaded and stored temporarily in a storage tank awaiting gasification and subsequent distribution to consumers. Residual dissociation water at the gasification is used as pellet carrier ballast water and is brought back to the loading port where it is used again used for producing NGH. By making each component process faster and more efficiently adapted to mass production, it will be cheaper to both build and operate and hence will enable the exploitation of smaller and currently uneconomic gas fields, thereby increasing the world's usable natural gas reserves.
(Enlarge: 31KB) |
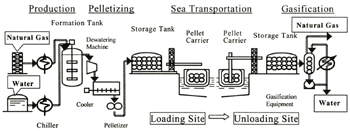 |
Figure 1. NGH-based Natural Gas Transportation System
EXPERIMENTAL STUDIES OF THE SYSTEM'S COMPONENT TECHNOLOGIES
The main components of the NGH pellet transport system technology shown in Figure 1 are: 1) NGH Formation Characteristics, 2) NGH Pelletizing Characteristics, 3) Pellet Storage Stability and 4) Gasification Characteristics. Experimental studies were carried out on each component technology to determine its applicability to a system using methane gas, the main component of natural gas. The results are described hereinafter.
NGH Formation Characteristics
Parameters affecting the formation rate of NGH are formation pressure, super-cooling (the difference between equilibrium temperature and formation temperature) and the contact surface area of gas and water. Of the three NGH formation methods currently used, i.e., the mixing, bubbling and spray methods, a method combining the mixing and bubbling methods was adopted as it can remove formation heat quickly, thereby enabling quick formation of NGH. This paper therefore describes the experimental results obtained with the combined method.
Figure 2 shows the formation tank used to produce the NGH. The tank is a pressure vessel of 10-liter capacity. Figure 3 shows the mixing and bubbling conditions inside the formation tank. Experimental parameters selected were mixing strength, bubbling gas volume and the super-cooling. NGH formation rate was calculated from methane gas flow rate assuming Hydrate Number is 6.2. Figure 4 shows an example of the experimental results which indicates that the amount of NGH formation increases proportionally with the increase in mixing Reynolds number and super-cooling. It is assumed that the increase in the contact surface area of water and gas is caused by the combination of the mixing and bubbling methods, and this, along with the removal of formation heat to maintain super cooling are the keys to the high speed production of NGH. Figure 4 also shows that the amount of NGH formation per initial filling water is about 1.2 kg/h/L, which implies that mass production of NGH with this system is quite feasible.
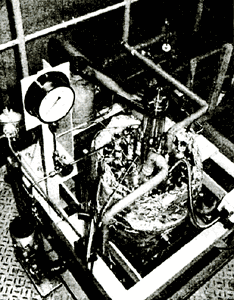
Figure 2. Formation tank
Figure 3. Mixing and bubbling conditions in Formation tank
Figure 4. Relation of NGH formation rate and super-cooling
NGH Pelletizing Characteristics
Figure 5 shows the continuous pelletizer, and Figure 6 shows NGH pellets of ψ20 mm made from powdered NGH. Of the three pelletizing methods currently in use, i.e. rolling, fluidized bed and compression molding, compression molding was chosen as it produces pellets with superior strength, which is important during prolonged and loading/unloading as well as producing pellets with a rounder shape. This is important for better fluidity, along with greater pellet homogeneity. Studies of the production method were also made, however, with a view to improving storage and transport efficiencies. As shown in Figure 6, it is confirmed that NGH can be pelletized under several MPa (max.) compression resulting in nearly perfectly round pellets. Separate pellet static collapse tests also confirmed that pellets made under the aforementioned conditions can bear about 0.21 MPa, which is the collapse pressure calculated by the static compression load from the ship's cargo hold top to its bottom and by the oscillation acceleration of the carrier ship. Slight adhesion between pellets was witnessed under loaded conditions typical of storage in a ship's hold, but it is judged that it can be avoided by controlling storage atmosphere properly.
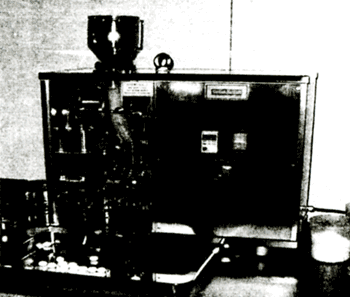
Figure 5. Continuous pelletizer
Figure 6. NGH pellets
|