1. COMPRESSION RINGS
1.1 Design
Extensive ring development work has been performed to satisfy the aforementioned engine requirements; indeed, the complex interactions between the rings, the piston and the cylinder liner justify the 'systems approach'. The main emphasis in ring development has been directed towards improving shape [1], optimising the peripheral surface geometry [2], optimising the tribological system of the ring and cylinder liner by modifying the surface topography [3] and improving the wear coatings on the peripheral surface in combination with optimised cylinder materials.
Medium speed engines, in contrast with high-speed types, use only compression rings with rectangular crossection; to the authors' knowledge keystone rings are not used. Rectangular compression rings provide better sealing of the cylinder gas pressure and lower side face wear, which contribute to the long life expectancy of more than 20,000 hours for these engines.
1.2 Profile Geometry
Typical peripheral profiles currently in use almost without exception are shown in (Fig 2).
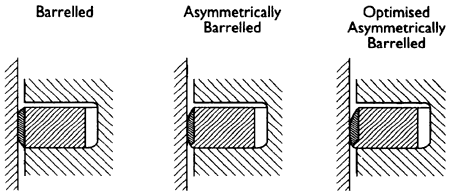
Fig. 2 Profiled Top Rings
The incorporation of symmetrically barrelled rings began in the 1970s, but nowadays asymmetric barrelling is being specified to an increasing extent. The advantages, as demonstrated in numerous theoretical calculations, lie in the improved formation of the oil film on the cylinder surface (Fig 3a)
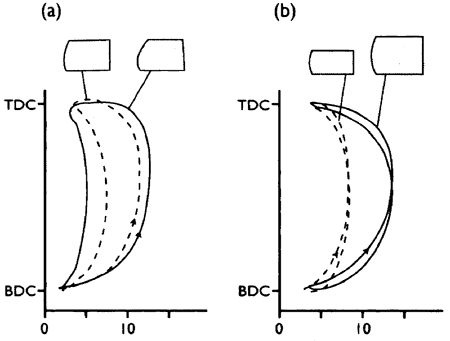
Fig. 3 Influence of Asymmetric Barrel and Ring Width on Oil Film Thickness
At the same time a certain relief of pressure at the running surface is achieved, which is in many cases imperative where high peak pressures are present. It may even be necessary to make use of pressure-relieved rings, but in such cases very careful adjustment of the axial clearance in the groove is necessary in order to guarantee a pressure build-up behind the ring. Otherwise collapse will occur, whereby the ring not only loses its sealing effect but also suffers scuffing and seizure.
Another important advantage is that after long running periods the upper corner of the running surface does not transport oil into the combustion chamber. (Fig 4)
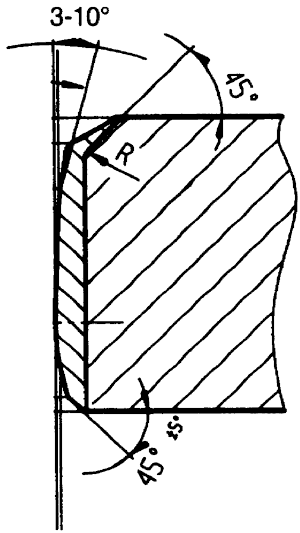
Fig. 4 Optimised Asymmetric Barrel Profile
1.3 Axial Width
The formation of the oil film on the cylinder surface is partly a function of the ring width; narrow rings produce a thinner oil film than rings of greater axial width (Fig 3b). Such behaviour is considered to be a possible explanation for the lower cylinder wear found at TDC when wider rings are used, particularly in high-speed engines, although it can be assumed that this oil covering mechanism is equally valid in medium speed engines and that the oil protection acts positively towards reducing corrosive wear.
The trend in ring axial width is shown in (Fig 5) in respect of engine development in recent years. Extremely narrow rings such as were preferred in the 1970s [4] are no longer used, their demise caused by the introduction of profiled peripheral surfaces (i. e. symmetrical or asymmetric barrel forms) which overcame running-in deficiencies and scuffing previously associated with wide rings. Wide and narrow rings are thus practically identical in their running-in behaviour.
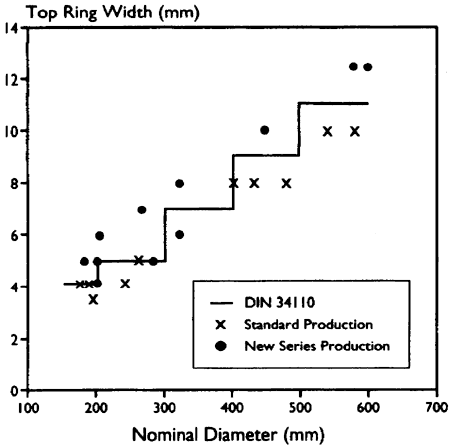
Fig. 5 Piston Ring Width for Medium Speed Four-Stroke Diesel Engines
BACK CONTENTS NEXT