1. Introduction
The crosshead-pin bearing in a large marine two cycle diesel engine operates under extremely severe lubrication condition, since the load acting on the bearing never reverses and the sliding speed is low in addition to the limited oscillatory motion. The bearing can not form a thick oil film adequate to be free from the bearing damage such as the metal seizure. The conventional bearing arranges several axial oil grooves on the loaded surface to promote the oil film exchange. The arrangement of axial oil grooves causes the remarkable reduction of load carrying capacity but is inevitable to exchange the oil film.
The analytical studies on the lubrication mechanism of conventional type crosshead-pin bearing were conducted by Wakuri [1-2]. Calculation results showed that both the film thickness and its fluctuation during one cycle is very small. The film thickness is comparable to surface roughnesses of the journal and bearing, and the crosshead-pin bearing probably operates in the partial lubrication regime. Some factors influencing on the load carrying capacity were investigated [3-5]. The oil film exchanging ability is much affected by the ratio of oscillating angle to pitch angle of oil groove. The film thickness decreases with the decrease in the clearance ratio. Although the improvement of load carrying capacity is achieved by changing the bearing structure from the clearance type to the fitted type, that of oil film exchange can not be expected.
The several methods for improving the load carrying capacity have been proposed. A high pressure hydrostatic lubrication system has been used to increase the film thickness [6-7]. Wakuri studied the lubrication characteristics of an externally pressurized crosshead-pin bearing [8]. The device for causing the bearing load direction to reverse by use of preloaded spring was attempted [9]. The effect of added rotation on the crosshead-pin bearing performance was studied [10]. The offset type crosshead-pin bearing, which is composed of the main segment and the eccentric segment, is superior in the load carrying capacity and the ability of the oil film exchange to the conventional bearing [3-5][11-151-The lubrication mechanism of the elliptical type crosshead-pin bearing was analyzed [5][16-18]. Although some of methods mentioned above have been already put into practical use, the crosshead-pin bearing with axial oil grooves have been generally used.
Patir and Cheng [19-20] postulated an average flow model for the isotropic surfaces and the surfaces with directional patterns, and they introduced the average Reynolds equation which governs the mean hydrodynamic pressure in EHD contacts. Rohde [21] applied the average Reynolds equation to the analysis of piston ring friction in the partial lubrication regime. The asperity contact pressures were obtained by using the asperity interaction model of Greenwood and Tripp [22]. The average Reynolds equation has been widely employed to predict the mixed lubrication characteristics of piston ring pack, cam and follower [23], and journal bearing [2-4-26]. While the average flow model can be applied to any rough surface structure, the surface orientation is assumed to be isotropic in the model of Greenwood and Tripp. Lee and Ren [27] investigated the effects of the surface topography, material hardness and load on the deformation behaviour of the rough surfaces. They formulated the real contact area and the average gap as functions of surface pattem parameter, material hardness parameter and loading parameter. The formulae were utilized to relate the average gap to the asperity contact pressure in the analysis of journal bearing [25].
In the present study, the theoretical analysis on the mixed lubrication of the crosshead-pin bearing is conducted. The analysis uses the average flow model by Patir and Cheng and the rough surface contact model by Lee and Ren. The effects of surface roughness and surface orientation on the lubrication characteristics of the bearing are examined.
2. Basic theory.
2.1 Hydrodynamics fbr rough surfaces
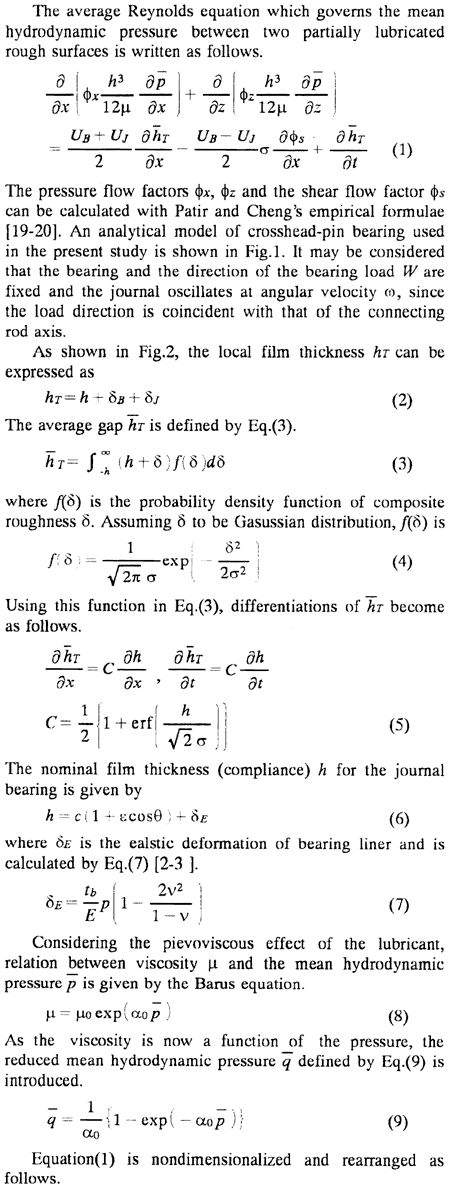