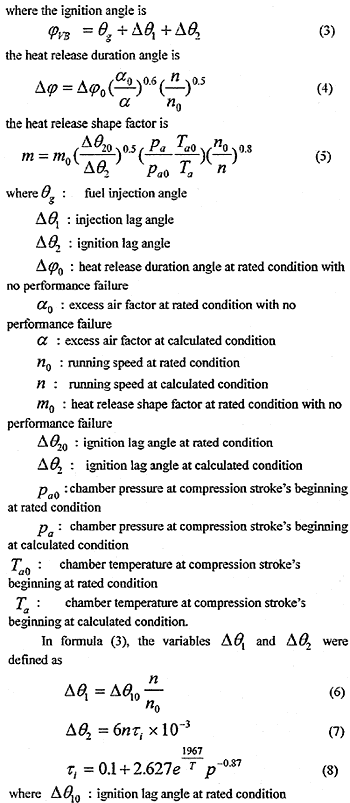
τi: ignition delay duration
T: chamber temperature at compression stroke's end
p : chamber pressure at compression stroke's end.
A three-zone scavenging mode, with fresh air, exhaust gas and mixing zones, was used. Turbocharger compressor and turbine experimental performance maps were included in digitized form and the code can interpolate within the data to find the operating point.
A large, medium speed; four-stroke, 6-cylinder fish-boat main diesel engine adapted with a turbocharger of VIR-201 type was chosen as reference to be simulated by the model. Previous calculation had formed good agreement of the model prediction with available experimental data[2]. By changing the appropriate input data and model coefficients 14 typical performance failures and 4 ship operation conditions were simulated on condition that running speed and engine load were kept unchanged. The selected input data and model coefficients of simulated failures refereed to the normal condition are shown in Table 1
3. SIMUIATED RESUIJTS
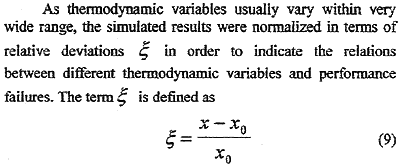
where the subscripts, x and x0, refer to the thermodynamic variable at normal and abnormal conditions. The calculated relative deviations at rated condition, where the engine speed is 450 r/min and effective power is 441.3 kW, and partial conditions where the engine speed is 315 r/min and effective power is 308.9 kW, are shown in Figure 1 and Figure 2 respectively. From Fig 1 and Fig.2 it is easy to find which variable is the most sensitive to some a failure and several interesting phenomena can be found after further analysis is described as below.
Blocked turbocharger exhaust casing (a) mainly makes decrease in temperature difference DTk and pressure difference of inter-cooler air DPk and slight rise in exhaust manifold temperature Tbt due to higher back-pressure of turbochahger. Blocked turbocharger filter (d) makes obvious decrease in pressures of compressor discharge air Pk, intake manifold air Ps, maximum combustion gas P=max max, inter-cooler air pressure difference gas exhaust DPk and obvious rise in gas exhaust manifold temperature Tbt due to bigger resistance of air flow and less air/fuel ratio inside chamber.
Poorly cooled cylinder liner (e) and piston cap (f) due to failures from cooling water system have very similar symptoms of obvious rising in compressor discharge temperature Tk, air intake manifold pressure Ps, air temperature difference of inter-cooler DTk, maximum combustion gas pressure P=max and metal temperature of liner or piston cap. This is because poor cooling water takes less heat and leaves more energy, but cylinder liner has a bigger influence due to its more cooling surface. Air-blocked inside cylinder jacket (n) reduces its cooling efficiency and hence induces increase in pressure difference DPk and temperature difference DTk of inter-cooler and decrease in fuel consumption ratio Ge. The symptoms of this failure are like that of poorly cooled cylinder liner due to the same reason.
High inlet cooling water temperature of inter-cooler (g) due to failures from cooling water system only induces the obvious decrease in air temperature difference of inter-cooler DTk and obvious increase in air intake manifold temperature Ts, and vice versa (h). Symptoms of fouled inter-cooler on air side (k) is similar to that of high inlet cooling water temperature failure except for the decrease in pressure difference of inter-cooler Dpk.