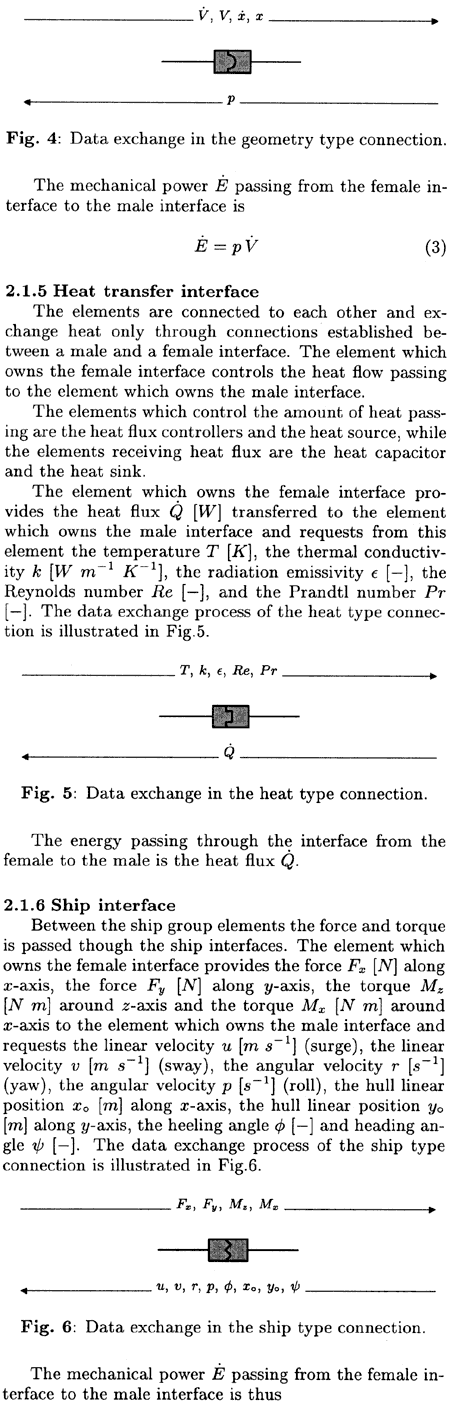

2.2 Groups of Elements
The elements are divided to groups based on their functionality. The available groups are:
・ the mechanical group of elements used to transfer the mechanical energy
・ the thermo-fluid group of elements used to model the Diesel engine using an emptying and filling method
・ the geometry group of elements used to provide the link between the mechanical and the thermo-fluid elements
・ the heat transfer group of elements used to model the engine heat transfer using a lumped heat capacity method
・ the ship group of elements used to model the hull dynamics and the propeller model, among others
Combining the elements together complex marine propulsion installations can be modeled with ease.
2.2.1 Mechanical group
The mechanical group of elements consists of propulsion elements which handle the transmission of mechanical power through torque. The mechanical elements introduced here are:
・ The stiff shaft which is the most important and useful of the mechanical elements. It acts as a calculator of the angular velocity and angular position of the system connected to it based on the total torque applied to the system and total polar moment of the system.
・ The elastic shaft which, as a result of his flexibility, produces torsional restoring torques, based on the deformation, which depends on the rigidity and dimensions of the shaft. The use of idealized stiff shafts together with idealized elastic shafts is a valid modeling approach of the behavior of a real system which exhibits elastic behavior.
・ The angle changer which is a simple element which changes the angular position between the input and the output.
・ The gearbox which changes the angular position and velocity between input and output.
・ The friction clutch which models a clutch where the torque is passed between two or more plates (of various shapes using friction.
・ The torque source which models a generic load (torque source) using an abstract general relationships.
・ The torque sink which models an idealized sub-system capable to absorb torque without a speed change. This element is useful for keeping constant angular velocity ignoring the torque and inertia of the load.
・ The energy loss which models the energy loss using a resisting torque, calculated as the sum of three terms: one proportional to the total torque transferred, one proportional to the angular velocity of the shaft and one constant. Using these terms, semi-empirical models describing the engine friction can be used with minimum modifications. Such models include the model of Mc Auly et al [3], the model of Winterbone and Tennant [4] and the model of Millington and Hartles [5]. The energy lost is rejected as heat to elements belonging to the heat transfer group.