This cleaning process can detach hard dirt layers depending on the temperature and expansion coefficient differences between the base material and the dirt layer.
For the best possible effect, the water injection nozzles are integrated into the gas channels of the TPS..D/E turbocharger and the design of the nozzles hasbeen optimized based on temperature measurements in the nozzle ring blades. In such measurements average temperature drops of approx. 210 K were registered during the cleaning cycle in a TPS57 turbocharger.
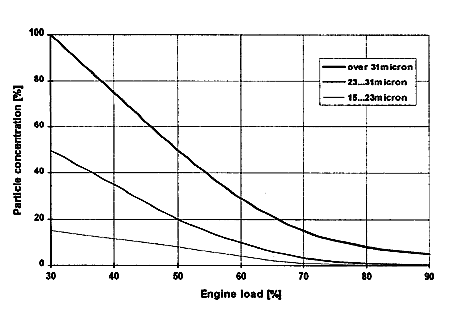
Fig 12: Typical particle concentration in exhaust gases vs. engine load on small medium speed diesel engines running on heavy fuel oil (ABB measurements)
Erosion is more often observed at low exhaust gas temperatures and low engine loads and can therefore typically be expected, for example, on auxiliary diesel engines running extended periods of time on part load. Under these conditions particle concentration measurements on different engine types have shown the strong increase of solid particles in the exhaust gases particularly of those larger than 30μm (Fig.12).
Erosion is created by the impact of the particles on the turbine components and particularly in turbochargers with radial or mixed-flow turbine, a concentration of erosion on the suction side of the nozzle ring blades can often be observed. Calculations of particle trajectories performed on older turbocharger types have shown that the reason for the erosion is the existence of particles which can be reflected several times between the turbine blades and the nozzle ring before they exit the turbine, thus increasing the particle erosion in this zone by a significant amount.
For the TPS..D/E turbocharger a special nozzle ring version has been designed for HFO applications. In this nozzle ring design a very hard coating layer is used in the critical zone increasing the expected lifetime by approx. 500%. With the protection in the form of a coating, the excellent ductility of the nozzle ring base material can be fully maintained, decreasing the risk of thermal cracking.
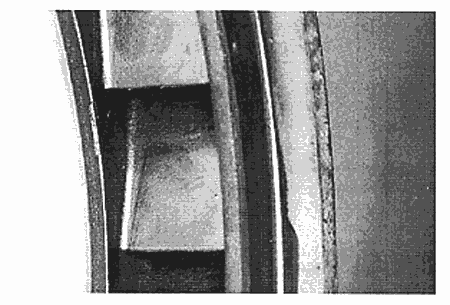
Fig 13: TPS48E nozzle ring (suction side) after 10,400hrs of operation on HFO engine
4.4.1 FIELD EXPERIENCE
Field experience for the TPS..D/E is available from auxiliary engine applications which are known to be very critical with regard to nozzle ring erosion but less susceptible to heavy contamination of the turbine components.
Inspections of such units have proven the effectiveness of the used nozzle ring coating material. In Fig.13 the suction side of a TPS48 nozzle ring after over 10,400 rhrs can be seen. No signs of erosion could be detected.
As expected, only small dirt layers of less than 0.5 mm have been registered on the nozzle ring and turbine wheel (Fig.14) of the same turbocharger. More inspections of units on other application types are planned for examining the effectiveness of turbine cleaning under field conditions.
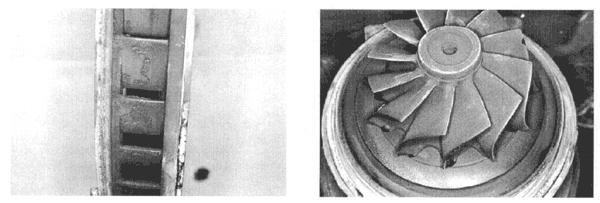
Fig 14: TPS48E nozzle ring (pressure side) and turbine wheel after 10,400hrs of operation on HFO engine
BACK CONTENTS NEXT