4. SERVICE TEST WITH IE SYSTEMS
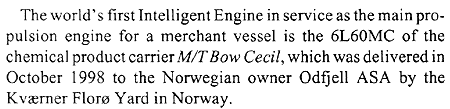
The engine was prepared for the IE systems during its production. The mechanical/hydraulic components of the IE systems were fitted to the engine during its installation in the vessel at the yard. These systems are installed on the upper platform of the engine, in parallel with the conventional camshaft. With this set-up, it is possible to change over completely from the conventional system to the IE system, or vice versa, within some three hours, so there is full redundancy. Fig. 8 illustrates the installation of the IE systems on the upper platform of the engine.
The ordinary camshaft system was used on the sea trial in accordance with the original contract between the parties, and it has also been used during the first operating period of the vessel. During this time, the auxiliary systems have been tested. So far, the following items have been completed:
4.1 Hydraulic oil conditioning system
The power medium employed for operating the fuel injection pumps and the exhaust valves is fine-filtered system oil from the engine, thus avoiding a separate hydraulic oil system with tanks, pumps and coolers, etc. The driving system utilises lube oil at a moderate working pressure (160-200 bar), but even so it is essential for ensuring a long lifetime of such hydraulic systems that the oil is clean. which requires ISO x/16/13.
However, the requirements for the engine system oil are not that strict nor are they needed for the engine itself; therefore, the oil for the IE systems requires extra filtration. For this purpose we use an automatic 6-micron filter located in the supply line to the IE system from the main lube oil pipe of the engine. From a system point of view, this acts as by-pass filtration and thus, over time, will fine-filter the whole oil charge of the engine obviously with the risk of clogging the filter.
Before deciding to use this system, we had tested it on our 4T50MX research engine with good results, confirming that filter clogging was not a problem and that the higher inlet pressure supplied to the hydraulic power supply unit (engine driven axial piston pumps) was indeed an advantage for these pumps. Subsequently, the filter system was fitted to a sister vessel to M/T Bow Cecil and service tested over a period of one year. The results were very satisfactory, again confirming that filter clogging was not a problem and that also the whole oil charge of the engine became significantly cleaner than before an added benefit for the engine.
The fine-filtering system has also been in operation on M/T Bow Cecil ever since the sea trial. The 'commissioning' of the filter during the sea trial is illustrated in Fig.9. The first operating hours during sea trial must be expected to deliver rather high amounts of particles (i.e. a high filter load). However, it can be seen that back-flushing of the filter is not triggered by the permissible pressure drop across the filter (max. 0.6 bar), but only by the timer, which is set to back-flush every hour. The subsequent service experience with the system has been very satisfactory - the only problem encountered was a 'cold soldering' on the print card for the filter control, which has been rectified by the supplier.
4.2 On-line cylinder pressure measuring system PMI, and CoCoS-EDS
These two systems were installed on the engine in August 1999 and are now being used by the crew as normal tools for monitoring the engine. After some minor teething troubles onboard, the PMI system is now working stable and reliably, providing on-line data on the working of' the cylinders to the CoCoS Engine Diagnosis System (EDS).
4.3 Electronic hardware and software
The development of the electronic control systems for fuel injection and exhaust valve actuation has been delayed due to the complexity of the software. The hardware has passed the required test (E10). Software approval is a two-step procedure: first, a SW development audit must be performed by the Classification Society in question (Det Norske Veritas). This has been done, and we have been approved for developing such software. The second step calls for a demonstration (on the 4T50MX research engine) of the functionality of the SW in the actual HW, for the purpose of proving that the complete system works as described in the design specification. This test will be performed in the summer this year.
4.4 Hydraulic power supply
The control software for the hydraulic power supply (engine and electrically driven hydraulic pumps) has been finalised and tested. The control system was successfully installed on board M/T Bow Cecil in April 2000.
4.5 Next steps for service tests on M/T Bow Cecil
Some of the mechanical hardware on board will have to be replaced to bring it up to date with the design of the 7S60ME-C engines (see below).