The thermodynamic behaviour is used to predict the flow compatibility and power balance under both steady-state and transient operating conditions. While the rotor dynamics as part of mechanical behaviour is simulated in order to analyse the performance of a gas turbine in transient modes. Transient modes represent the behaviour of a gas turbine while it is accelerating or decelerating. Most of the studies use convergence techniques to analyse the performance characteristics of individual components in a gas turbine system. The techniques involve the iteration approach to reduce the error until the independent variables such as flow rate, pressure, temperature, rotational speed and power reach equilibrium.
As a mobile vessel, a ship travels to different areas with different atmospheric conditions. The atmospheric conditions at sea vary with geographical location, season and time during certain period. Thus, the performance of a gas turbine varies with the areas where a ship operates. The effect of varying atmospheric conditions on marine gas turbine carried out by the authors some two years ago[4]. It was found that the specific heat of working fluid which is considered as one of the main parameters in a gas turbine simulation is mainly affected by the atmospheric conditions. The specific heat is usually assumed unchanged in a gas turbine cycle simulation. In fact, it varies with temperature, humidity and pressure of the atmospheric conditions.
2. MODELLING OF GAS TURBINE COMPONENTS
In this study, a single spool and simple cycle gas turbine with a separate power turbine is modelled in an attempt to analyse the dynamic performance. The power turbine is connected, through a reduction gear, to load. The model analyses the gas turbine on the basis of thermodynamic and mechanical simulation. It is also assumed that there are no heat and energy accumulations during transient periods in its components. The specific heat of working fluid is merely affected by the temperature and constituents of the working fluid mixture. The effect of pressure variation on specific heat is assumed relatively neglectable as a marine propulsion turbine always operates at sea level. Figure 1 illustrates the block diagram of the gas turbine described above.
2.1. Properties of the working fluid
The influence of atmospheric conditions is evaluated based on the variation of temperature and humidity of air as the working fluid in the gas turbine. The temperature and humidity of air vary dramatically throughout the cycle, which in turn change the specific heat capacity. The general analytic-polynomial expressions for specific heat capacity of dry air and water vapour used in this study are taken from by Mattingly and Turns [5][6]:
The value of an is defined as polynomial coefficients and it has different values according to the type of working fluids. In this study, the dry air index i = 7, and the polynomial coefficients are:
a0 = 1.0475
a1 = -3.8839 x 10-4
a2 = 8.8879 x 10-7
a3 = -1.6403 x 10-10
a4 = -6.6491 x 10-13
a5 = 6.0296 x 10-16
a6 = -2.0686 x 10-19
a7 = 2.5929 x 10-23
For water vapour, the index of constituents i = 4, and the polynomial coefficients are:
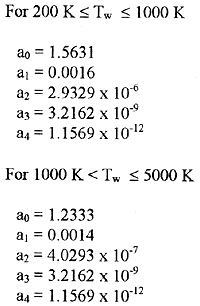
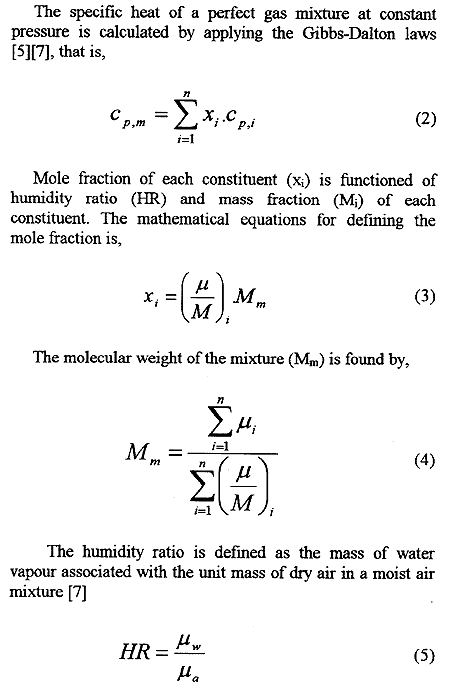
Detail derivation of above equation(s) can be found in Zhou and Jeferson [4].