Table 1 Comparison of Propulsion System
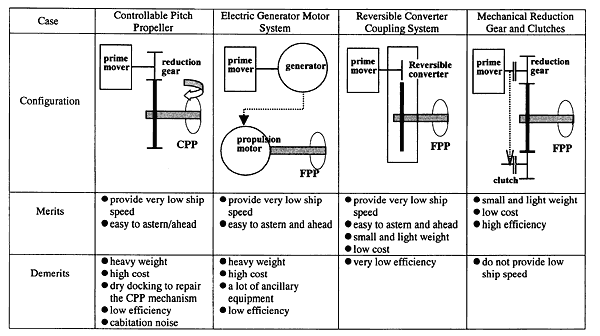
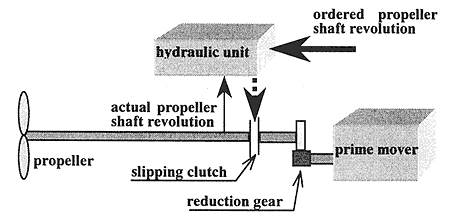
Fig.1 Schematic diagram of conventional slipping clutch
In the accelerating condition as well as steady sailing of ship, the propeller torque is obviously positive, this system is working well by means of slipping the clutch disk. However, in case of the decelerating condition, it is ordered to reduce the propeller revolution, then the pressure of clutch disk goes down until the propeller shaft revolution reaches the ordered one. The propeller torque is also reduced. Soon after, the torque turns to negative. At this moment, the propeller revolution can not reduce any more and just idling released from the prime mover. Although such coasting may be useful for the open sea as saving the fuel energy, it is dangerous particularly in congested harbor and restricted channel.
In order to improve such decelerating condition of ship, the following slipping clutch system is designed as shown in Fig. 2. In this system, two slipping clutches are installed in both forward and reverse revolution gears. No.1 clutch system works when the transmitting torque is positive. No.2 clutch system does when it is negative by the lower propeller revolution. Once the propeller revolution is ordered to reduce, the pressure of No.1 clutch disk goes down until the propeller torque turns to negative. After that, the No.2 clutch system begins to produce the negative torque instead of No.1 system.
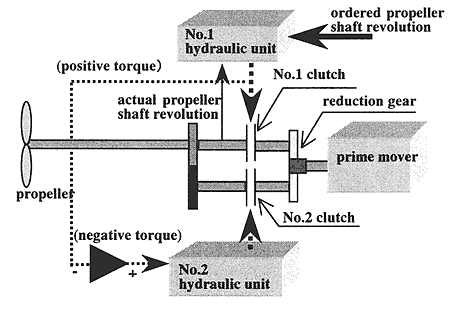
Fig.2 Push-Pull control slipping clutch
Then, the propeller revolution can reduce and reach the ordered one. If the propeller torque comes back to the positive side, the propeller revolution becomes lower than the ordered one. Then, the pressure turns to positive and No.1 clutch works instead of No.2 clutch. Since No.1 and No.2 clutch systems do not work simultaneously, the capacity of hydraulic units and cooling systems are not necessary the twice capacity.
Furthermore, this system can be used in the propeller reversing side without any modification. When ASTERN is ordered, the hydraulic pressure of No.1 clutch disk becomes negative and the clutch is released soon. Then the No.2 clutch system begins to work until the propeller revolution gets steady in reversing side.
The characteristics of the steady propeller-shaft revolution are schematically shown in Fig.3 comparing from the mechanical clutching system.
BACK CONTENTS NEXT