TS-12
Three Dimensional Combustion Simulation for Low Speed 2 Stroke Diesel Engine
Hiroyuki Endo*, Yuji Oda*, Masahiko Okabe** and Osamu Motomura**
ABSTRACT
Reducing heat flux from high temperature combustion flame to the walls of exhaust valves, cylinder covers and pistons is essential to increased power output of diesel engines, and the authors have developed CFD analysis that can estimate the heat flux from the gas to the cylinder walls. The simulation code was based on the KIVA3 code, and the sub-model for fuel spray breakup was modified and evaluated using experimental data for fuel spray motion under high atmospheric pressure conditions. Ignition delay was estimated using an empirical approach, while the rate of combustion was calculated using both the rate of turbulent mixing and the rate of chemical reaction, and convection heat transfer was predicted by means of a turbulent heat transfer model based on the k-ε turbulent model. Test calculations were carried out for a low speed 2 stroke diesel engine, demonstrating that the developed simulation code is capable of estimating not only combustion characteristics in the cylinder but also the heat flux on the cylinder wall, and can be used as an effective tool to improve the performance and reliability of low speed 2-stroke diesel engines.
Key Words: Diesel Engine, Combustion, Modeling, Simulation, Heat flux, Heat transfer
1. INTRODUCTION
As competition has intensified in terms of high output for low speed 2-stroke diesel engines, heat flux in the combustion chamber has tended to increase, and the development of heat flux prediction tools is needed in order to increase development efficiency. Accordingly, the research reported here was directed at time-wise and special estimation of the heat flux distribution in the combustion chamber of a low speed 2-stroke diesel engine by means of prediction based on quantitative analysis of processes such as flow, spray behavior, fuel evaporation, the mixing of air and fuel, self ignition, combustion, and heat transfer from the high temperature gas to the walls. Although computational precision is still insufficient, it has become possible to predict the relationship between combustion system specifications and combustion chamber heat flux, and it is clear that this can be applied in the improvement of the performance and reliability of low speed 2-stroke diesel engines.
2. CALCULATION METHOD
Below is presented an overview of the calculation method that has been developed, which is based on the KIVA3[1] combustion flow analysis code created at the Los Alamos National Laboratory for internal combustion engine use. In addition, high precision models were introduced for spray breakup, ignition and combustion, and heat transfer. Only the portions that differ from the KIVA3 code are explained here.
2-1. THE GOVERNING EQUATION
The governing equation is basically the same as in KIVA3, but the following transportation equation with respect to the Livengood-Wu integration K value in order to estimate self ignition:
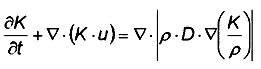
where, K: Livengood-Wu integration value
u: speed
ρ: density
Also, the RNG k-ε model,[3] used in the KIVA3V, [2] is introduced as the turbulence model.
2-2. SPRAY MODEL
The model for spray breakup is based on Reitz's wave breakup model, [4] with an improvement using Hiroyasu's experimental function [5] to prevent spray breakup within the breakup distance. With respect to free spray under high pressure conditions, the results of comparison between computational results and photographs showing actual measurement are presented in Fig.1. It can accordingly be seen that the spray, breakup model simulates actual measurements to a certain extent.
* Nagasaki R&D Center,
Mitsubishi Heavy Industries, Ltd.
5-717-1, Fukahori-machi, Nagasaki 851-0392 JAPAN
FAX: +81-95-834-2445
** Diesel Department, Kobe Shipyard & Machinery Works,
Mitsubishi Heavy Industries, Ltd.