Combustion process was analyzed theoretically by using the authors' two-zone model [8, 9] consisting of the burned gas temperature analysis, the NOx formation analysis and the soot formation analysis. The rates of NO formation, soot formation and soot oxidation were analyzed based on the measured combustion pressure time history, the measured NOx concentration and the measured smoke density. The changes due to nozzle orifice size in the soot particle size and the number of soot particles were estimated through the analysis of the excess air ratio of the burned zone.
2. EXPERIMENTAL APPARATUS
The test engine shown in Fig.1 was a four-cylinder high-speed turbocharged direct injection diesel engine with intercooler for automobiles, which was the type 4D31-T manufactured by Mitsubishi Motor Corporation; 100 mm bore, 105 mm stroke, compression ratio of 16 and a maximum output of 95.6 kW (130 PS)/3,500 rpm. The special VE-type fuel injection pump was used to adjust the fuel injection timing arbitrarily and easily. The test injector shown in Fig.2 was the two-spring injector currently used widely. The five kinds of standard multi-hole nozzle having five holes were used in the test: orifice size was varied from 0.26 mm to 0.24, 0.22, 0.20 and 0.18 mm, and the opening pressure of the needle valve was set at 21 MPa.
The test engine was operated at a constant speed of 1,750 ± 5 rpm under two kinds of mean effective pressure condition; Pme = 0.40 and 0.83 MPa, and three kinds of fuel injection timing "θinj" of 5°BTDC, TDC and 5°ATDC. The inlet suction air temperature at the engine inlet downstream of turbo-blower was regulated at 45 ± 0.5℃ by controlling the water flow rate of intercooler. The suction air pressure at the inlet of turbocharger was also adjusted and fixed at the standard atmospheric condition by using the motor-driven blower. The test fuel was an ordinary gas oil with a cetane index of 57.
The time histories of combustion pressure, fuel nozzle pressure and the needle valve lift were measured using the respective sensors, and their signals were sampled every one-fourth degree of crank angle simultaneously by means of the four-channel combustion analyzer CB-467 manufactured by Ono Sokki Co. Ltd. The measured time histories of the experimental results are the averaged values repeated over continuous 350 engine cycles. Their data were transmitted to the personal computer and recorded on floppy disks.
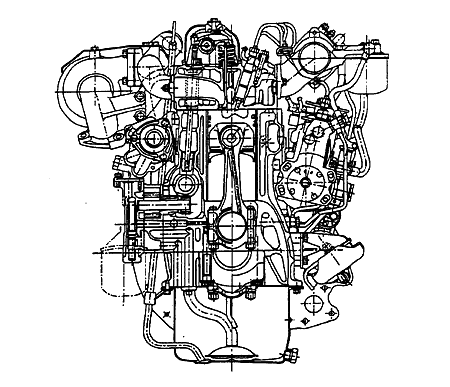
Fig.1 Section of test engine
3. EXPERIMENTAL RESULTS AND DISCUSSIONS
3.1 Effect of Orifice Size on Combustion History
Figures 3(a) and (b) show changes in time histories of the injection pressure "PN", the in-cylinder pressure "P", the apparent heat release rate "dQ/dθ" and the needle valve lift "Lift" measured at the low and high loads respectively under the condition of θinj = TDC. The parameter is the size of nozzle orifice which is varied from 0.26 to 0.18 mm every 0.02 mm. The initial injection rate must be suppressed by the two-spring injector judging from the fact that the lift curves in Fig.3 show a slow rate of lifting at the upper half of the maximum lift except for the case of 0.18 mm orifice. However, there was little difference in both initial combustion and engine performance between the two-spring injector and the conventional single-spring one. As the orifice size decreases, the injection duration and the maximum injection pressure increase in both low and high loads. The longer injection duration results in the longer combustion duration in the high load case, however, almost no increase in the combustion duration in the low load case. The heat release curve varies markedly between the case of 0.22 mm and that of 0.20 mm in both low and high loads. Especially in the cases of 0.20 and 0.18 mm, the maximum heat release rate becomes lower clearly compared with the other cases because of the smaller initial injection rate resulting from the smaller orifice size. Furthermore, as the orifice size is decreased in the high load case, the in-cylinder pressure in the compression stroke becomes higher due to the higher boost pressure by the turbocharger based on the higher exhaust gas temperature.
3.2 Effect of Orifice Size on Engine Performance
Figures 4(a) and (b) show the effect of orifice size on the maximum injection pressure "PNmax", the exhaust gas temperature "Te" , exhaust emissions "THC", "NOx", "Smoke" and fuel consumption "be" under the fuel injection timing of θinj = TDC . Smoke density shows the minimum at the orifice size of 0.22 mm in both low and high loads, and the fuel consumption also indicates the minimum at 0.20 or 0.22 mm.