Cylinder head
A fully new cylinder head has been designed featuring larger intake and exhaust valves as well as corresponding ports. The flow characteristics of both inlet and exhaust ports have been quite improved, with respectively 37% and 59% equivalent flow areas gains.
Connecting rod
As the crankpin diameter had to be increased by 20 mm in order to raise the torsional natural frequencies of the crankshaft and to keep the connecting rod bearing load at low values, the former bevel cut connecting rod has been replaced by a so called "marine-type".
With the enlarged crankpin diameter, the specific pressure on the connecting rod big end bearing has been brought back to the level of the former PC2.5 engine (Fig.6). This, associated to the use of "Rillenlager" high load capacity bearing types, ensures a long trouble-free life time to the bearing shells.
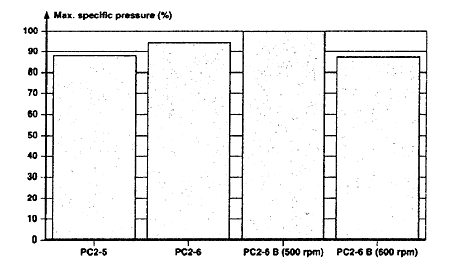
Fig.6 - Connecting rod bearings
Maximum specific pressure on big end bearing
Camshaft
The initial design used in PC engines, of one-piece shafts with shrunk-on cams and assembled bearing housings, has been completely changed in favour of one-cylinder camshaft pieces, with integrated cams, flange connected to separate bearing journals. The housing is of the "tunnel" type with bearings integrated in the crankcase.
The torsional stiffness of the camshaft has been multiplied by a factor of 2.7, thanks to its larger diameter.
This results in an improved situation regarding torsional vibrations amplitudes, which allows to avoid the use of an elastic drive of the camshaft on constant speed engines.
Furthermore bigger cams resulted in lower Hertz pressures and again in a still higher safety margin (Fig.7).
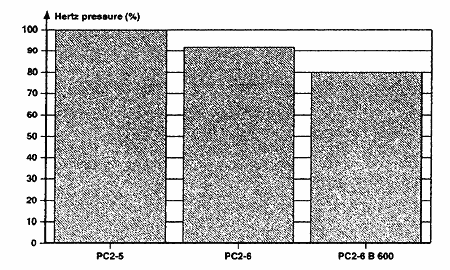
Fig.7 - Fuel injection cam
Hertz pressure at cam roller contact
Crankshaft
As for the crankpins, the main bearing journals were increased by 20 mm in order to get high torsional natural frequencies of the crankshaft and to reduce bearing loads.
Crankcase
The local modification made on the nodular cast iron crankcase, to incorporate the new camshaft bearing housings, resulted in a substantial increase of the crankcase stiffness in bending and torsional modes.
Piston
In order to cope with the new specific power rating, the design of the shaker cavity has been revised. This, associated with an increased oil flow achieved through lower flow resistance circuits, improved the piston cooling efficiency. The piston has also been reinforced in order to allow peak combustion pressures increased up to 185 bar.
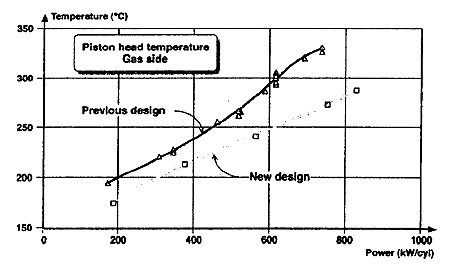
Fig.8 - PC2.6 B Pistons
Comparison of previous and new designs
Cylinder liner
A two-piece cylinder liner has been designed, in order to incorporate a bore-cooled anti-bore polishing ring (Fig.9).
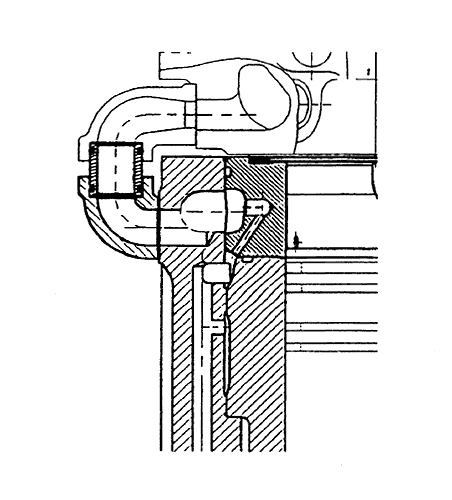
Fig .9 - PC2.6 B cylinder liner design
BACK CONTENTS NEXT