However, because small-capacity gas turbines use small blades, machining complex cooling structures inside them is very difficult, making it impossible to attain the cooling levels of large-capacity turbines. This makes it difficult to increase TIT in small-capacity gas turbines.
The SMGT's target TIT of 1,200℃ is 50〜100℃ higher than that of conventional gas turbines in the same output class. However, to ensure adequate cooling of the small blades, more R&D on the cooling structures inside the blades (Figure 12) is required.
In addition to cooled blade performance analysis, enlarged scale models of the blades' interior have been made in order to observe the flow of cooling air and help determine the ideal shape of the cooling passages (Figure 13). Tests have also been carried out to accurately measure their heat transfer characteristics of the fins located inside the cooling passages that promote heat transfer.
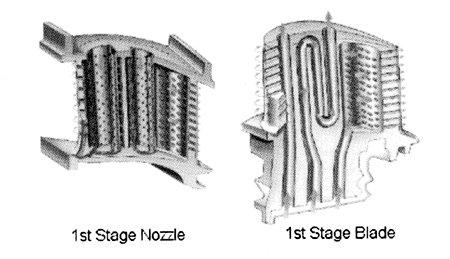
Figure 12 Conceptual drawing of cooled blades
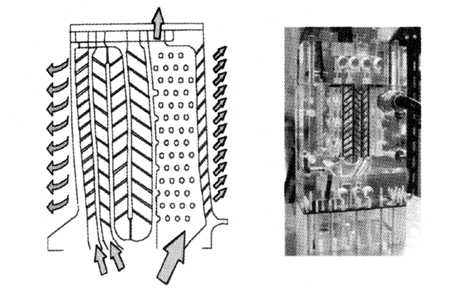
Figure 13 Observation of cooling air flow
Based on this analytical and test data, development of cooled blades is progressing. High-temperature cooling cascade tests are being carried out to measure blade surface temperatures and to evaluate cooling performance (Figure 14).
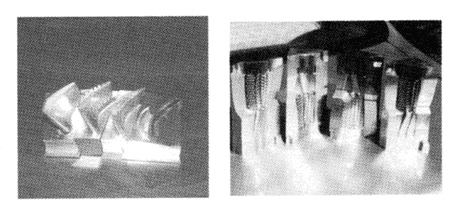
Figure 14 Tested models of cooled blade
5.5) Research on Improving Partial Load Efficiency
As stated in section 5., an effort is being made to improve thermal efficiency under partial load. For the power turbine, in addition to the usual fixed nozzle turbine, a power turbine with a variable nozzle for its first stage is also being developed.
In the case of regenerative cycle gas turbines, if the recuperator's inlet gas temperature can be maintained at the rated level, thermal efficiency under partial load can be improved. (Figure 15) For this, a reduction in load (partial load) should be accomplished by reducing gas flow rate. A variable nozzle makes it possible. By changing the nozzle mounting angle, the minimum area between the blades (throat area) changes, allowing the gas flow rate to be changed.
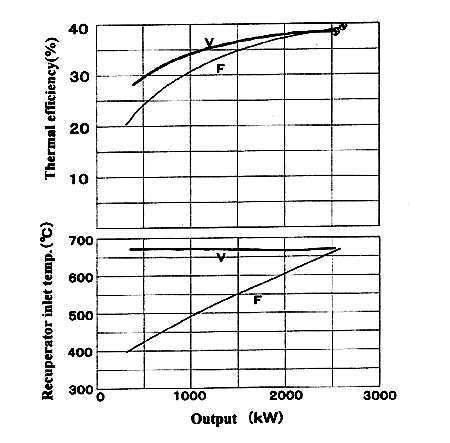
Figure 15 Estimated results for partial load performance
However, in addition to the structural problems associated with variable mechanisms in a high-temperature area, there is a performance loss due to blade tip clearance leakage associated with variable nozzles, something not associated with fixed nozzle turbines.
BACK CONTENTS NEXT