In the Figure, sudden drop of weight and very low heat release are observed at around 500K and around 600K respectively. This is the typical characteristic of so called Dumb-bell fuel.
Smooth burning shift from volatile component to residual component is essential to good combustion of marine fuel oil. Sudden weight drop and low heat release in above case suggest bad balance of component and long ignition delay. Long frame existed for a long time and reached to the surface of cylinder liner. As a result, oil film on the liner surface was ruined.
In this case, we made clear the relationship between problem and fuel oil quality. However, it must be stressed that it is often very difficult to define the cause of combustion troubles by means of normal analysis. It is desired to develop the effective combustion quality analyzing method.
3. ON-BOARD PRE-TREATMENT SYSTEM
It was investigated how the quality of the fuel oil is altered through the pre-treatment system by 14 vessels in 1998-99. Figure 7 shows a typical onboard pre-treatment system of fuel oil. The system consists of tanks, purifier, filters etc, and dual pressure system is adopted. Specimens were sampled from 8 points in the system and 20 items each were analyzed. All vessels used 380 mm2/s (@ 50 degree C) of Kinematic Viscosity oil and flow rate* of purifiers were ranged from 24 to 79%.
* Flow rate; Recommended rate of purifier manufactures for 380 mm2/s (@50℃) is 100%
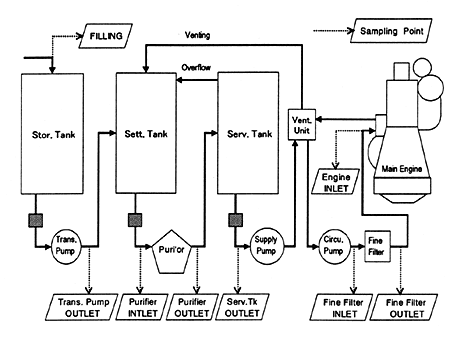
Fig.7 Fuel oil Pre-treatment system
3.1 CHANGE OF CONCENTRATIONS
Figure 8 shows the change of concentrations though the system. Water, Sediment, Aluminum and Silicon (Al+Si: FCC catalyst), Iron, etc. were removed somewhat well by purifier. Density. MCR, Sulfur, Vanadium etc. are not improved. And Density and Viscosity had a tendency to increase a little in heating circulating system.
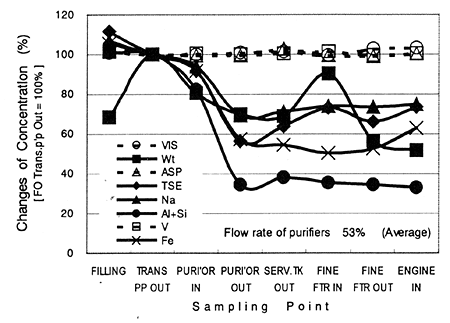
Fig.8 Changes in Pre-treatment System
3.2 SEPARATION EFFICIENCY OF Al+Si
Figure 9 shows the relationship between flow rate of purifier and separation efficiency of Al+Si. The range of concentration of Al+Si at purifier inlet is from 11 to 57 mg/kg, and average is 23 mg/kg.
(The size of FCC catalyst is not considered.)
The separation efficiency of purifier increases with the decreasing of flow rate. Average of efficiency is around 65% when 50% of flow rate, and 80% when 25 to 30% flow rate. And it is estimated that the separation efficiency is about 50% when 100% of recommended flow rate.
The recommendations of upper limit of Al+Si by engine manufactures (low speed engines) are from 7 to 15 mg/kg at engine inlet. And the average of Al+Si in normal fuel oil is around 20 mg/kg. Therefore, manufacturer's recommended capacity for purifiers is workable for the normal fuel oil (around 20 mg/kg of Al+Si). And for the fuel oil with 80 mg/kg of Al+Si, which is maximum value of ISO RM, manufactures' recommended capacity is insufficient.
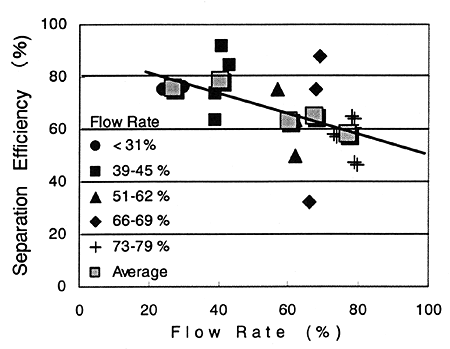
Fig.9 Separation Efficiency of Purifier
BACK CONTENTS NEXT