NCF80A Exhaust Valve with High-Hardened Seat
1. Introduction
Service life elongation of exhaust valves has long been a major challenge to those trying to reduce engine maintenance costs. Especially for high power, heavy load engines now in use, conventional heat resistant steel is inadequate, and even stronger alloy which is exceptionally resistant to heat has been required for exhaust valve spindles.
2. Aim of Development
As a material that can meet this requirement, Nittan Valve Co., Ltd. has chosen NCF80A out of several conceivable candidates. Considering the functions required of different parts of an exhaust valve spindle, NCF80A is adequate in strength against high temperature and in resistance against thermal corrosion, but as it might prove somewhat insufficient in resistance to the possible biting of the seat face when heavier fuel is used, solution of the problem was at first attempted by padding with a similarly Ni-based material, such as Colmonoy 6.
Fig. 1. Hardness (Valve Face)
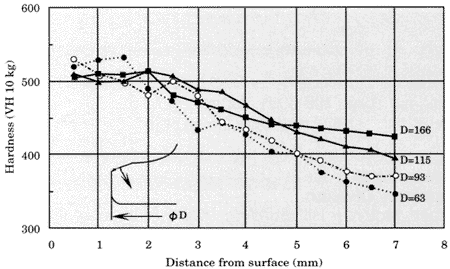
3. Operational Result, and Attempts for Improvement
A considerable number of such armoured valves were produced, but their performance could hardly be considered stable enough. Thus, while better ones posed no problem after operation for 6,000 hours or more, some others suffered a blow-by of the seat face in a very early phase of operation, i.e. in 1,000 hours or so. This was due to the instability of welding quality, which in turn was due to the difficulty to weld the armouring to NCF80A and the low melting point of the Ni-based armouring material.
To solve this problem, a way to harden the seat section without armouring was searched for with focus on the work hardening of this material itself. Thus it was intended to increase the hardness of the material, to the same level as would be reached by armouring, by subjecting the seat section to work deformation. This method was tested under many different working conditions and with various work shapes, resulting in successful hardening of the seat section to the level illustrated in Fig. 1 while preventing cracks from occurring in the seat face by virtue of the absence of armouring with a different metal.
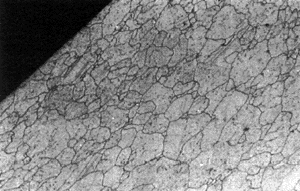
Microstructure of seat face subjected to work deformation
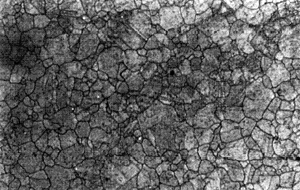
Internal microstructure subjected to work deformation
4. Performance Results
The NCF80A exhaust valve with a high-hardened seat thereby developed has since gone through various design improvements and, used in many medium speed engines of 160 to 570 mm in cylinder bore where the conditions are even more stringent, demonstrated satisfactory performance. In the case of a certain cogeneration engine, with conventional heat resistant steel armoured with Stellite 12, 50 percent of its exhaust valves had suffered a blow-by in 4,000 hours, but the exhaust valves proved virtually free from any blow-by even in 8,000 hours when NCF80A valves were used.
5. Summary
While some appreciate the NCF80A exhaust valve with a high-hardened seat as having solved all the problems of exhaust valves, others say NCF80A will prove still inadequate for even higher power, heavier load engines which are expected to emerge in the future. The manufacturer is trying to work out a material which will be even stronger against high temperature and more resistant to thermal corrosion than NCF80A.
Nittan Valve Co., Ltd.
Head Office
Address: 7-2, Yaesu 2-chome, Chuo-ku, Tokyo 104-0028
Tel: +81-3-3271-4821 Fax: +81-3-3273-5900
BACK CONTENTS NEXT