4 Performance requirements
4.1 Functionality
Geo-magnetic principles of THDs detects horizontal component of geomagnetic field, and generates a ship's true heading signal for other devices.
In one type of the sensor which utilizes a magnetic compass, the performances and requirements of the compass shall be conformed to the ones referred to ISO 449 and the other type of the sensor shall fulfil the performance requirements concerning the marine electromagnetic compasses in ISO 11606.
4.2.1 All displays with the exception of the sensor, and all outputs of heading shall indicate true heading.
4.2.2 Manually entered values used for electronic correction shall be indicated by adequate means.
On the bottom part of the binnacle and/or the housing of the sensor system, a fore-and-aft mark shall be inscribed to facilitate installation in the fore-and-aft line of the ship. The units shall be installed on the fore-and-aft line of the ship. In magnetic compass type THDs, it shall be in the vertical plane passing through the centre of the compass card and the main lubber mark to within ± [0,5°].
The THD shall be provided true heading information to the other navigational aids within a transmission error of not greater than ± 0,2°.
Heading information shall provide with an output with accuracy as defined in 5.
At least one output shall be in accordance with the relevant international marine interface standard, IEC 61162 series.
Electrical wiring, such as that for the direct-current power supply and that for connecting the units, shall not produce any perceptible errors in the heading information.
The housing of the magnetic sensor system shall be non-magnetic.
An alarm shall be provided to indicate malfunctions of the THD or a failure of the power supply.
5.1 General
The THD shall meet at least the following accuracy at the output of the device under sea conditions as specified in IMO Resolution A.424(XI) or A.821(19) as applicable.
5.2 Accuracy of transmission data
The transmission error, including the resolution error, shall be less than ± 0,2°.
5.3 Static error (settle point error)
The static errors shall be less than ± 1,0°.
The dynamic error amplitude shall be less than ± 1,5°. The dynamic error frequency for test shall be less than 0,033 Hz equivalent to a period not shorter than 30s if the amplitude of the dynamic error exceeds ± 0,5°.
The follow-up error for the rates of turn shall be:
― less than ± 0,5°up to a rate of 10°/s; and
― less than ± 1,5°up to a rate of between 10°/s and 20°/s.
5.6 Settling time requirements to the directional system
In magnetic compass type sensors, the directional system shall always settle in the original direction. Following an initial deflection of the card of 90°from the magnetic meridian, the time taken to return finally to within 1°of the magnetic meridian, shall not exceed 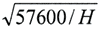 sec at a temperature of 20℃ ± 3℃, where H is the horizontal component of the magnetic flux density in microteslas (μT) at the place of testing.
5.7 Correcting the magnetic heading by magnetic variations
In order to get true headings, correcting the magnetic heading by magnetic variations shall be carried out within the errors of [ 0,5° ]. The means of correcting magnetic variation may be either manually or automatically performed.
The values used for electronic compensation should be indicated by adequate means and shall be stored such that values are automatically recovered on switch-on.
5.8 Adjusting of magnetic deviations and heeling error
It shall be possible to adjust the coefficients A, B, C, D so that the residual value of each coefficient is less than [ ±1°].
The binnacles shall contain the device for correcting the deviation due to the horizontal components of the ship's permanent magnetism. This device shall be capable of correcting a coefficient A up to ± 3°, coefficient B and C of up to at least (720/H)°, coefficient D of up to ± 7°, vertical component of the ship's magnetic field (producing the heeling error): up to ± 75 μT, H being as defined in 5.6.
5.8.2 Check by magnetic fields
In electromagnetic compass type THDs, each coefficient of residual deviations shall be obtained by the following equations.
where nN, nE, nS, nW are ship's northern magnetic field when the ship's heading is N, E, S and W respectively. The n' is the mean value of nN, nE, nS, nW. Coefficients A shall be negligible small in electromagnetic compass type THDs.
The compensating devices shall be protected against accidental alterations.
5.9 Means of adjusting the deviation by vertical soft iron of the ship
Means of adjusting the deviation by vertical soft iron of the ship should be provided.
5.10 Protection of correcting devices
Any correcting devices or parameters shall be protected against inadvertent operation.
5.11 The THD shall update a new heading at least once every 50 ms.
6.1 General
Type testing shall be carried out before the instruments covered come into regular service. For type testing, only new devices are acceptable.
The THD shall be tested for accuracy with the sensing part connected. If the sensing part is so designed as to be included in the transmitting part, the equipment shall be tested with altogether.
Unless otherwise stated in this standard, all tests shall be carried out according to the requirement of the IEC 60945.
Tests in a static magnetic field shall be carried out in an authorized test room.
Devices which have passed the type-tests and comply with the requirements shall be so certified in the language of the test authority and in English.
Copies of the certificate shall be issued on demand. They shall be explicitly marked ”copy”.
Acceptance of type-test certificates between countries will be a matter for mutual agreement.
The THD shall be tested for accuracy with the sensing part connected. If the sensing part is so designed that it is included in the transmitting part, the equipment shall be tested all parts.
6.2 Transmission error tests
On a rotating test stand, bring the heading mark of the THD until the output shows 000,0, then rotate the stand slowly ten degrees. The readings of the transmission output shall meet the requirements of 5.2. During the readings of the output of the transmission part shall fulfil the requirements of 5.2.
6.3 Fore-and-aft mark tests
In magnetic compass type THDs, the examination may be carried out on a rotating test stand with the aid of a plumb line and with the compass in the binnacle.
In electromagnetic compass type THDs, the examination shall be verified by visual inspection or electrical measurements.
The results shall fulfil the requirements specified in 4.3.
6.4 Heading information tests
This test can be carried out as the same way of the test of static error mentioned in 6.5 checking the readings of the output heading. The results shall fulfil the requirements specified in 4.4.
6.5.1 In a magnetic compass type THD
The static error applies to the compass without fluxgate sensors. The fluxgate of a THD shall be placed so that the influence on the card heading shall not exceed 1,0° on any heading.
The examination may be carried out on a compass test stand. After having brought the rotation centre of the compass card into the rotation axis of the test stand, the static error can be read at the card graduation by means of a telescope or any other appropriate means, when the vertical plane of the sight passing through the rotation axis has been aligned with the magnetic meridian in advance. This measurement shall be carried out on at least four equidistant headings.
The static error shall be within ± 1,0°.
NOTE If the test is undertaken in the compass bowl, it should be noted that the resulting value then includes the deviation due to any magnetic material in the compass and/or in the fluxgate sensor.
6.5.2 In an electromagnetic compass type THD
After having brought the fore-and-aft line of the sensor housing into the line passing through the centre of the test stand and the zero line orientated north, the static error can be read comparing the output heading with the rotation angle. This measurement shall be carried out on at least four equidistant headings. The test results shall conform with the requirements of the 5.3.
Set up the magnetic sensor on a test platform, and rotate the platform at a rate of 20°/s. The readings of the heading output shall fulfil the requirements specified in 5.5.
The card, if fitted, is deflected 90°, held there for at least 10s and then released. The time, in seconds, taken to return finally to within 1° of the magnetic meridian shall not exceed the value required in 5.6. This is repeated on the other side of the meridian and the mean is taken.
6.8 Tests of correcting the magnetic heading by magnetic variations
After indicating the magnetic heading on the display, when a few values of magnetic variations are manually or automatically input to the system, all the true headings indicated shall be within the accuracy of the requirement of 5.7. In the system containing a positioning system, after bringing the system in a position of which magnetic field is not disturbed, turn the system so as that the direction of the fore-and-aft mark from the centre aligns a distant object of which true bearing is known, the true heading indication coincidence shall be within the accuracy of the requirement of 5.7 as well.
6.9 Tests of adjusting magnetic deviations
The sensing part is placed on the test stand and aligned on north or south. An external magnetic force sufficiently far away to create a reasonable even field in the vicinity of the directional element is applied until a deviation of (720/H)° is obtained. This deviation is then corrected by the magnets. The resulting deviation shall not exceed the values as required in 5.8.1. Repeat on east and/or west.
The amount of deviation of D that can be corrected can be checked by placing the compass and binnacle on a test stand on a quadrennial course with and without the correctors in position. In the electromagnetic compass type sensor, the maximum amount of D in 5.8.1 which is to be corrected is measured in the quadrennial course with and without the switch of correction of coefficient D in the maximum values. The result shall fulfil the requirement of 5.8.1.
6.10 Tests of the means of adjusting the deviation by vertical soft iron
When the THD is provided with Flinders's bars, they shall be checked visually.
Mount the sensing part on a test stand, then the motion tests shall be carried out with the following nominal simple harmonic table motions. And record the heading.
― roll axis: Peak amplitude 20°± 2°, period 6s ± 1s,
― pitch axis: Peak amplitude 10°± 2°, period 10s ± 1s,
― yaw axis: Peak amplitude 5°± 1, period being 15 ± 1s.
At the end of the period of [5] minutes duration tests, the mean values of the recorded heading shall be within ± 1,5° of the original heading. The result shall fulfil the requirement of 5.4.
Observe the heading output rate and ensure it is a minimum of 50 ms.
7 Marking and identification check
Each unit of the THDs shall be marked with the following:
― the identification of the manufacturer;
― the equipment type number or identification of the model which was type tested;
― the serial number of the unit;
― the year of manufacture(not necessary if the year of manufacture can be read by the serial number);
The presence of the markings on the unit of the THDs specified as above shall be checked by visual inspection.
|