I−3−1 造船生産工程管理
<1> ワールドクラス製造モデル(World Class Manufacturing Model)
期間:1999年9月〜2001年1月、コスト総額:263万ドル(造船所124万ドル、NSRP ASE 139万ドル)
米国造船所にリーン製造方式を確立することを目的としたプロジェクトである。NASSCOが中心となっているが、その他バス・アイアン・ワークス、ニューポートニューズ、エレクトリック・ボート、トッド・パシフィック、iRobotics、ファー・イースト・マリン・インターナショナル、日本技術マネージメント・プログラム、エンジニアリング・コンサルティング会社であるMunro & Associates、米国標準技術研究所(NIST)、ワシントン大学、ミシガン大学が参加している。本報告書第I部で紹介するプロジェクトは大なり小なり本プロジェクトと関係があり、I−4章においてそれらの関係について述べる。
リーン製造方式の元祖はトヨタ自動車のジャスト・イン・タイム(JIT)製造方式である。1900年代初頭以来の規模の経済(スケール・メリット)にのみ裏打ちされたフォードの大量流れ生産方式の欠点を正す方式として、1960年代初期にトヨタで採用されたこの方式は、高品質、低コスト、短リードタイム、柔軟性を得る生産方式として1980年代米国製造業界で注目を集めた。リーン製造方式の基本は注文から引き渡しまでの時間を各段階の無駄(Waste)を徹底的に省くことによって短縮しようとするものである。元来大量生産の製品に適した方法であるが、その考え方は造船業にも一部を除き適用可能である、
図I−5は造船のブロック・製造時の価値付加時間(黒)、無駄(灰色)とリーン製造方式との関係を示したものである。
リーン製造方式では価値付加時間の一部も機器のロボット化や自動化を導入して短縮するが、短縮の大部分は無駄の部分の短縮である。トヨタの掲げる無駄は下記7点である。
・部品の必要以上の過剰生産――必要時に必要な量を生産する。
・欠陥部品の製造――欠陥の修正のため生産の流れが止まる。
・インベントリーの不適切――ストックヤード等無駄な投資の誘発。
・製品に価値を与えない動作――必要な工具を探す動作等。
・過剰品質――真の価値の付与に留める。
・輸送――製品の移動は顧客には何等の価値も生まない。
・待ち時間――材料や作業員の待ち時間。
本プロジェクトではまず日本の3造船所及び米国の2造船所にベンチマーク調査団が派遣され、リーン製造方式の具体的定着状況が調査された。またNASSCOの3個所の鋼材加工ラインで作業のタイム・スタデイが実施され、ベンチマーキングの結果に加えられた。さらに本プロジェクト・チームはリーン製造方式に基づく造船所の模型を完成した。これらの成果は下記3報告書にまとめられ関係者に配布されている。
図I−5
(拡大画面:94KB) |
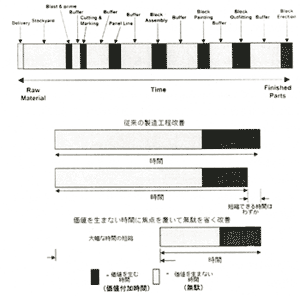 |
・リーン製造原理ガイド(Lean Manufacturing Principles Guide)
・リーン造船へ脱皮するためのQ&A(Why Change to Lean Shipbuilding)
・人間工学/安全/健康/環境のための設計ガイド(Ergonomics/Safety/Health/Environmental Methodology Design Guide)
リーン製造方式を適用してワールドクラス造船所となるための要件としてプロジェクト・チームが理解したのは以下の点である。
・製品の標準化、プロセスの簡易化、製造コントロールと管理技術の改善。
・自動化レベルの向上
・社会・ビジネス環境の中に組み込まれた計画の実行。
プロジェクト・チームは上記報告書の中で従来の米国の造船所は図I−6上段に示すように工程間の無駄の多いバッチ建造方式であるが、リーン製造方式を導入して下段に示すようなワン・ピース流れ建造方式として無駄を減らし、ストックヤード等も減らそうと結論づけている。
(図I−6)
(拡大画面:102KB) |
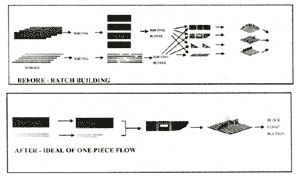 |
NSRPの造船生産工程管理パネルで無駄を減らす方法として重要視されているのは工作精度である。工作精度を上げて手直し、即ち無駄を減らそうということであるが工作精度に関するプロジェクトについては第II部で述べるNSRP独自プロジェクトや海軍のSBIRプロジェクトで実施されている。
2001年インガルスはパイプ工場の一部をリーン製造方式のモデルラインに変更し、コンサルタントを雇って従業員に日本流の改善教育を実施した。新ラインの成果として下記が報告されている。
・プロセス中の作業量が74%減少。
・リードタイム75%減少。
・工場床面積17%減少。
・作業員の作業中歩行距離90%減少。
・5S関連の大幅な改善(I−3−5節)。
インガルスではその後パイプ工場のみならず自社工場の他の部分や同系列のアボンデールにもリーン製造方式を広めている。なお、本プロジェクトに引き続いて下記プロジェクトが契約された。
<2> 米国新造、オーバーホール及び修理造船所のリーン・エンタープライズ・モデル(Lean Enterprise Model)
期間:2001年7月〜2003年12月、コスト総額750万ドル(造船所370万ドル、NSRP ASE 380万ドル)
リーン製造方式の考え方を下記4種の市場も規模も異なる造船所に適用し、具体的モデルを作成することを目的としている。下記の造船所の他、V2Rコンサルタント、Optipris、P.Jaquith & Associates、Maloneコンサルタントが参加し、さらにペンシルバニア大学もアドバイザーとして参加している。
・商船新造―アトランティック・マリン(モービル工場及びジャクソンビル工場)生産全域に適用
・艦艇新造―バース・アイアン・ワークス、鋼材組立及び艤装組立工場に適用
・艦艇/商船オーバーホール及び修理(民間)―トッドパシフィック、アトランティック・マリン(モービル及びジャックソンビル)
・艦艇オーバーホール/修理(海軍工廠)―ピュージェット・サウンド海軍工廠、USS ネバダに適用
<3>線状加熱法による船舶鋼板構造の複雑な形状組成のための分析ツール(Line Heating)
期間:1999年7月〜2002年1月、コスト総額:44万ドル(造船所22万ドル、NSRP ASE 22万ドル)
線状加熱法にコンピューター・アルゴリズムを導入して特定形状を作り出すための分析予測手法開発を目的としているが、アトランテイック・マリンとEWI(Edison Welding Institute)により実施され、他の造船所は参加していない。本プロジェクトでは酸素燃料トーチ及び保持装置等のハードウエア、最終形状予測のためのソフトウエアを組み込んだ半自動線状加熱システムが開発され、造船所でテストされた。さらにキャリブレーション実験及び有限要素法モデル手法との比較が行われた。従来熟練作業員が試行錯誤(trial and error)で行なっていた作業方式や、NSRPの独自プロジェクトとして開発された有限要素法モデル手法に比べ、本プロジェクトの方法は格段に作業スピードを増すものである。試行錯誤で数日かかった作業は本プロジェクトの方法で数時間に短縮されたが、最初の目標は20分であり、まだそのレベルに達していなので開発の余地が残っている。今後はONR ManTechプロジェクトの中で「CNC熱鋼板成形」(CNC Thermal Plate Forming)として継続される。
|