2)構造
点火装置は2・200図に示すようにイグニションコイルの一次側に流れる電流を、断続器で断続することによって二次側に高電圧を誘起し、この電圧をディストリビュータにより点火順序に従って、各シリンダに設けられたスパークプラグに配電してプラグの電極間で電気火花を発生させ、各シリンダ内の混合気に点火して燃焼させるための装置である。
(拡大画面:19KB) |
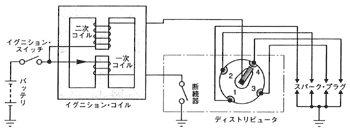 |
2・200図 点火装置
イグニションコイルの一次電流の断続には、ブレーカポイント又はトランジスタの断続器が用いられている。現在ではトランジスタの断続器が殆どであり、その種類にはディストリビュータのシャフトに設けられたシグナルロータ及びブレーカプレート上に設けられたピックアップコイルによって行うトランジスタ式と、クランク角センサや他のセンサを用いてコンピュータでパワートランジスタを制御するマイクロコンピュータ式とがある。
(1)イグニションコイル
イグニションコイルは、2・201図に示すように鉄心に一次コイルと二次コイルを巻いたものをケースに収め、固定及び絶縁のために周囲にエポキシ樹脂などを充填している。
一次コイルは、樹脂形成された一次ボビンに、直径0.5〜1.2mmの絶縁された銅線が150〜300回重ねて巻いてあり、二次ボビンの内側に配置されている。一方、二次コイルは二次ボビンに、直径0.05〜0.1mmの絶縁された銅線を15000〜30000回重ねて巻いてある。鉄心は薄い鉄板を重ね合わせたものであり、一次ボビンの内側に配置されている。
整備時には次の2点について点検する。
・高圧端子の焼損の点検
・イグニションコイルの抵抗の点検
2・201図 イグニション・コイル
(2)ディストリビュータ
ディストリビュータは2・202図に示すように次の機構で構成されている。
(1)イグニションコイルで発生した高電圧を、点火順序に従って各シリンダのスパークプラグに順次配分する配電機構
配電機構は、2・203図に示すようにキャップとロータで構成され、イグニションコイルで発生した高電圧を各スパークプラグへ配電するためのものである。イグニションコイルからの高電圧はキャップの中心電極からセンタカーボンを経てロータに移りロ一夕からキャップの外側電極へ、わずかなギャップを火花として飛び移り、ハイテンションコードを経てスパークプラグへ配電される。
2・202図 ディストリビュータ
2・203図 配電機構
(2)イグニションコイルの一次電流の断続を行うイグナイタヘ、信号を送るための点火信号発生機構
点火信号発生機構には、2・204図に示すようにシグナルロータ並びにマグネット及びピックアップコイルからなるシグナルジェネレータを内蔵する無接点式の断続機構が用いられている。マグネットからの磁束は、次の経路でピックアップコイルを通過するがシグナルロータが回転しないときは磁束も変化せず、ピックアップコイルには起電力が発生しない。
マグネット→シグナルロータ→ピックアップコイル→ブラケット→マグネット
2・204図 無接点式ディストリビュータ
(3)ディストリビュータシャフトを駆動する駆動機構
駆動機構は、ディストリビュータシャフトとシャフトの先端部に組み付けてあるギヤなどで構成されており、一般にカムシャフト、設けられたギヤによって4サイクルエンジンの場合、クランクシャフトの1/2の回転速度で駆動される。
整備時には次の4点について点検調整する。
・キャップの損傷の点検
・センタカーボンの摩耗の点検
・エアギャップの点検(2・204図に示す「a」)
・ピックアップコイルの点検
(3)ハイテンションコード
ハイテンションコードはイグニションコイルで発生した高電圧を、イグニションコイルからディストリビュータヘと、またディストリビュータからスパークプラグヘと伝えるものである。ハイテンションコードは、2・205図に示すように中心部の導体をゴムで絶縁し、保護している。導体としては図(1)のようにガラス繊維などに炭素を染みこませたものと、図(2)のように更に、その導体の周りをニクロム線で巻き付けたものがあり、それぞれ均一な抵抗を持たせている。
整備時には次の3点について点検する。
・絶縁体の劣化の点検
・外部被覆の損傷の点検
・抵抗値の点検
(拡大画面:21KB) |
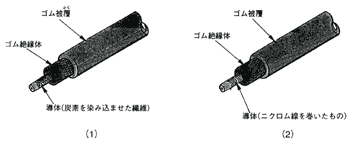 |
2・205図 ハイテンション・コードの種類
(4)スパークプラグ
スパークプラグは、2・206図に示すようにハウジング、絶縁碍子、電極などで構成されている。
電極はハウジング(プラグ本体)に取り付けられた(溶接された)接地電極とこれと絶縁された中心電極とで構成され、一般に両電極とも放電しやすく、放電による消耗も少なく腐食に強いニッケル合金が用いられている。また、中軸には鋼又は銅合金が使われている。
絶縁碍子は高温高圧に耐え、電気的な絶縁耐力が高く、化学的に安定し、熱伝導性が良く機械的強度が高いことが要求され、純度の高いアルミナ磁器で造られており、電極の支持と高電圧の漏電を防ぐ働きをしている
ハウジング(プラグ本体)は炭素鋼で造られ、絶縁碍子の支持及びプラグをエンジンに取り付けるためのもので、下部には接地電極が溶接されており、又、接地電極と中心電極との間には、スパークギャップ(火花すき間)を形成している。
(拡大画面:27KB) |
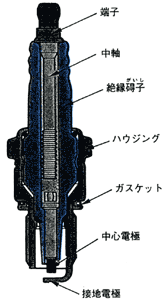 |
2・207図 スパーク・プラグ
スパークプラグは圧縮された混合気に点火して燃焼を起こさせるものであり、燃焼によって生じる高圧に耐え、気密を保持し、又電極部が常に適温に保たれるように、燃焼時に電極部が受けた熱を他へ放熱する必要がある。放熱しにくく電極部の温度が高くなり過ぎると、この部分が熱源となって、正規の火花放電による点火より前に混合気が燃焼し始め、過早着火を起こすことになり、出力低下、運転不調となる。逆に、放熱しすぎて電極部の温度が低すぎると、燃焼時に生じたカーボンが碍子に付着し“くすぶり”の現象となり絶縁不良を起こす。従って、この部分で高電圧がリークして電極部で放電が行われなくなり、不完全燃焼でエンジンの運転不調となる。スパークプラグの温度が400℃以上になると、スパークプラグ自体の温度で付着したカーボンを燃焼させてきれいにする作用がある。これを自己清浄作用という。
従って、エンジンの運転状態に応じて電極部の温度を適温に保つ必要があり、この適温の範囲は、一般に、500〜800℃位である。
スパークプラグが受ける熱は、エンジンの使用状態によって異なり、低速では電極部の温度は低く、高速になるほど温度は高くなっている。従って、常に電極部の温度を適温に保つようにするには、低速航行の多い船では、放熱しにくい熱特性を持ったスパークプラグを使い、高速航行の多い船では、放熱しやすい熱特性を持ったスパークブラグを使うと良い。このように、スパークプラグでは、放熱が重要な特性であり、スパークプラグが受けた熱をどれだけ放熱するかという度合いを表すものとして熱価(ヒートレンジ)という言葉が用いられている。放熱しにくく電極部が焼けやすいスパークプラグを低熱価型(ホットタイプ、焼け型)プラグといい、放熱しやすく電極部の焼けにくいスパークプラグを高熱価型(コールドタイプ、冷え型)プラグと呼んでいる。
高熱価型プラグと低熱価型プラグの構造的な相違は、2・208図に示すように碍子脚部(図中L寸法)の寸法である。高熱価型プラグは脚部が短く、この部分の受熱面積も少なく放熱経路も短くなって放熱しやすくなっている。低熱価型プラグは、逆に脚部が長く受熱面積も大きく放熱経路も長いので、放熱しにくくなっている。
2・208図 熱価による構造の違い
|