THE EVALUATION OF INSTALLATION OF DPS IN TANDEM OFFLOADING FPSO
Ikuo Yamamoto and Masami Matsuura (Mitsubishi Heavy Industries, Ltd., Japan)
Hiroaki Hirayama, Yoshifumi Suehiro, and Masaru Ihara (Japan National Oil Corporation, Japan)
Eiichi Kobayashi (Kobe University of Mercantile Marine, Japan)
Abstract: An integrated simulator to conduct a total simulation of an offshore oil production system is developed based on discrete event modeling technology. In the paper, an overview of the developed simulator is described, and it is shown that the evaluation of installation of DPS in tandem offloading FPSO is successfully conducted and specification of designing offshore oil production system can be determined. Analysis of real offshore oil system by the simulator is conducted, and its effectiveness is confirmed.
1. INTRODUCTION
An integrated simulator of an offshore oil field becomes much important to make a production and transportation plan considering cost before construction of real offshore oil production system. The authors have developed a simulator named SIMOP (SIMulation program of Offshore oil Production), which can simulate behavior of conditions of an overall system consisted of offshore oil production well, floating structure, production facility, sea transportation vessel (tanker), shipment facility, and land equipment considering weather condition.
Firstly, an overview of SIMOP is described in the chapter 2. Secondly, the effects on total operation performance resulting from adoption of dynamic positioning system (DPS) for a tandem offloading system are evaluated by something simulation for the northern area of the North Sea, the area offshore of Borneo and the area offshore of the Pearl River Basin in the chapter 3. Finally, a real application case of SIMOP in the North Sea for fixed tower is described in the chapter4.
2. OFFSHORE OIL PRODUCTION SIMULATOR SIMOP
Fig.1 shows a whole screen of the developed simulator. It consists of a weather module, an oil production well module, a production facility module, a sending off equipment module, a transportation equipment module, a land equipment module, and a simulation time module, which are connected by discrete event modeling method verified in comparison with real systems [1], [2], [3].
The weather module has weather rank generation statistical data of 5O offshore oil regions in the Atlantic, Indian, Pacific and other oceans. Fig.2 shows an example of the input screen of the weather module.
The production well module has the following functions:
Determination of oil production amount
・The oil production amount of each every time is determined by the production period of the production well from the amount of the daily output, and transported to the production facility continuously.
・The investment is calculated from the operation expense of the oil field development cost (initial development) and to the entire oil field equipment.
The production facility module has the following functions:
Machinery determination
・According to selection of the offshore platform type (Fixed/Tower, Ship SPM, Semi Sub, Tension Leg), specification of offshore platform and its machinery (ex. water cut from crude oil) are determined and calculated.
・When the weather condition reaches the save limit level of the production facility, the production is stopped during the required time for saving and returning automatically.
Calculation of operational cost
・The production operational costs are calculated for every period input in the production well.
Fig.1 Whole screen of simulator
(Enlarged Image:172KB) |
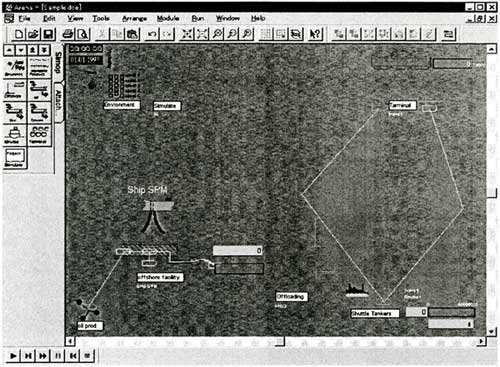 |
Fig.2 An example of weather module input screen.
The sending off module has the following function.
・The sending off equipment method (Side by side method, Tandem method) are specified (incl. stop and re-start of operation) and calculated automatically according to the weather condition and the FSO/FPSO selection.
・The oil which has been sent from the production facility is accumulated in the storage tank, and sent off to the sea vessel (tanker) when it arrives.
・Production is stopped automatically when it becomes fullness of tank capacity.
・The speed of carrying oil sent off to the tanker is determined by the berthing method of the sea vessel.
Fig.3 Screen of simulator of two land equipment case.
(Enlarged Image:173KB) |
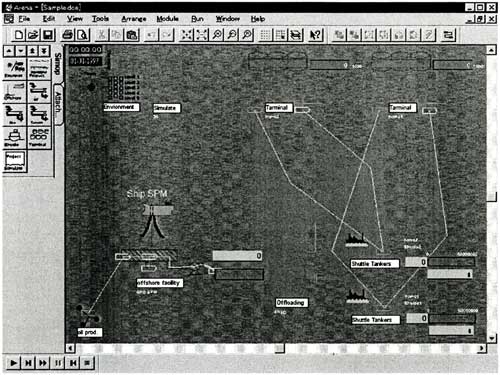 |
The transportation equipment module has the following function.
・The specification of the sea vessel from the sending off equipment to the land facility (ex. number, size, speed of the sea vessel) is determined considering weather condition and the state of the storage tank.
・The transportation costs are calculated for every period. Also, it can consider the Clarkson chart.
The land equipment module has the following function.
・The oil is received from tanker and stored. The simulator can cope with the plural land equipments. Fig.3 shows the simulation case of two land equipment.
Table 1 Output data of simulator
The simulated time and the unit quantity (barrel) of the crude oil sent from the production well to the production facility are set up in the simulation time module.
In the simulator, tanker operating control algorithm is developed by two layers hierarchy control and agent net based theory. The control algorithm is effective to give tankers the optimal timing of maneuvering from land equipment to storage tank considering update state of storage tank (oil level) and maneuvering of other tankers.
The simulator can give not only the time series of animation, but also the numerical calculated output data shown in Table 1. Various results to design the practical offshore oil production system can be gotten.
|