SIMULATION-BASED DESIGN AND TESTING OF DYNAMICALLY POSITIONED MARINE VESSELS
Asgeir J. Sørensen, Department of Marine Technology, Norwegian University of Science and Technology, Trondheim, Norway
Egil Pedersen, Advanced Maritime Transport Technology Department, National Maritime Research Institute, Tokyo, Japan
Øyvind N. Smogeli, Department of Marine Technology, Norwegian University of Science and Technology, Trondheim, Norway
Abstract: Properly designed simulators are efficient tools in system design and analysis. In research and development of control systems, simulations are well established in the working procedures. However, use of simulators in verification and testing of target control systems is yet not much exploited in the marine industry. In automotive and aerospace industries, hardware-in-the-loop simulation is established as industry standard and incorporated in the design process. In this paper a new modular multi-disciplinary simulator based on Matlab/Simulink is presented. The simulator is named Marine Cybernetics Simulator (MCSim) and is used in the education of MSc and PhD candidates within the fields of hydrodynamics, structural mechanics, machinery systems, and marine control and navigation systems. Openness and modularity of software modules are prioritized design principles for systematic accumulation and reuse of knowledge, resulting in improved and more efficient learning and development processes. The simulator is targeted for various marine control applications and marine operations, including sea transportation and navigational safety, offshore exploration and exploitation of hydrocarbons, and fisheries and aquaculture industries.
1. INTRODUCTION
For years simulators have been used as tools in system design and analysis, both in academia and in the industry. At the Norwegian University of Science and Technology (NTNU) a new simulator based on Matlab/Simulink, Marine Cybernetics Simulator (MCSim), is under development at the Department of Marine Technology in cooperation with the Department of Engineering Cybernetics. MCSim is a modular system simulator integrating the disciplines hydrodynamics, structural mechanics, marine machinery. navigation and automatic control of marine vessels. The simulation environment may consist of a distributed network of dedicated computers simulating complex marine operations involving several systems and components. The main purpose of MCSim is to improve the accumulation and reuse of knowledge and thereby the quality of the education for MSc and PhD candidates. Industrial applications studied are sea transportation, offshore oil and gas operations, fishery and aquaculture.
In the testing of safety critical marine control systems for e.g. power management, dynamic positioning (DP), manoeuvring and transit operations of ships and floating offshore structures, utilization of a real-time simulation environment for hardware-in- the-loop simulation will be foreseen. The overall objective of the simulation-based design and testing is to improve safety and performance in marine operations and sea transportation. A failure mode and effect analysis (FMEA) module will be used to test the control system performance, alarm system and logics subject to varying environmental conditions and failure situations in the control system, navigation system, power plant, thrusters and sensor system.
This paper presents the design philosophy of the MCSim. The demonstration case is a dynamically positioned semi-submersible conducting drilling operation. The development of a position reference system based on measurements of riser angles in conjunction with a mathematical model is shown. Drilling is a safety critical marine operation, and the vessels are often classified according to DP Class 2 or 3. A DP vessel maintains its position (fixed location or pre-determined track) exclusively by means of active thrusters and propellers.
2. SIMULATOR SPECIFICATION AND REQUIREMENTS
2.1 Modularity
The simulator will be continuously developed by students and researchers, and will serve a diversity of applications. This necessitates a modular structure, in which each module is a self-contained unit with a well-defined interface and functionality. A simulator management group will ensure strict quality control of the officially available modules, which will be updated on a regular basis. The individual user may choose the modules necessary for the application in question, and develop new modules to interface with the simulator. These modules may later be added to the official release, and in time a large library of modules will become available. All modules should have a fully specified interface; enabling easy substitution of old modules and standardizing information flow between modules. The modularity also facilitates distributed simulations.
2.2 Simulator Structure
The core of the simulator is the process plant models, which give the necessary detailed description of the vessel dynamics and its surroundings. The other main parts of the simulator are the control systems interfaced with the sensor and actuator modules. The control systems may for instance be:
・Dynamic positioning (DP) system.
・Thruster assisted position-mooring system.
・Tracking controllers and autopilots.
・Local thrust controllers.
・Power management system.
・Crane control systems.
・Heave compensation systems.
A schematic of an example simulator structure, including a riser module with control feedback from riser angles is shown in Fig.1. An extensive vessel database is intended to be part of the simulator. The following vessel types will be included
・Supply ships.
・Tankers.
・FPSOs.
・Semi-submersibles.
・Fishing vessels.
・Cruise and passenger vessels.
The available data for each of the vessels should at least be:
・Main particulars.
・Transfer functions.
・Hydrodynamic coefficients.
・Thruster/power configurations and ratings.
・Sensor systems configurations.
Scaling algorithms for the vessel data will in time be included in the software, so that users easily may scale the data to fit other vessel sizes.
Fig.1 Example of simulator structure.
2.3 Openness
The purpose of the simulator is to give students and researchers the opportunity of performing time-domain simulations of a vessel with various control applications. This motivates making the simulator partly open-source. Three release levels may be relevant, see Table 1.
Table 1. Release levels.
Release level |
Modules |
1) Open-Source: Open to everyone. |
All basic modules of the official release. |
2) Limited access: Open for students
and researchers. |
Advanced modules with classified material, preliminary modules. |
3) Restricted access:
License required |
Modules developed by business partners etc. |
|
An additional release level may be modules in which only a DLL is available as open-source, but the source code is of limited access.
2.4 Module Hierarchy
Depending on the development stage and required accuracy of the operation and application studied, a hierarchy in module complexity is allowed. For any application, several modules of varying technical complexity, built-in functionality and release levels may exist. These should all cover the same basic functionality and have the same interfaces, and may therefore easily be interchanged. An example may be two different riser modules; one simple finite element model written in MATLAB, open-source, computationally light and with limited validity, and one Fortran module based on the riser program RIFLEX [2], which requires a user license, is computationally demanding and gives more accurate results. In the latter case RIFLEX may be run on a separate computer interfaced to the MCSim computer. Fig.2 shows a module hierarchy example, where module complexity is plotted versus release level and application. Any module combination is allowed, which in this example gives 9 possible configurations of vessel, riser and environmental models.
Fig.2 Module hierarchy example.
The choice of configuration for a simulation will depend on the required accuracy of each module, the computer resources and the release levels available to the user. If, for example, riser response is the main focus, a complex riser and current model may be considered, whereas a simple vessel and wave model are sufficient. The various control applications may at early stages be simplified software versions written in Matlab or Simulink. Later, refined versions and target control systems may be interfaced to the simulator.
2.5 Hardware and Software Platform
The simulator is currently being developed in a MATLAB/Simulink environment on the Windows PC platform. Simulink was chosen for running the main simulation loop because of its flexibility towards several programming languages. Applications written in MATLAB, C, C++, Fortran and ADA may easily be linked to the simulation by use of S-functions. This is convenient for generating simulator modules from existing code, and makes development of new modules more user-friendly.
As the complete simulator may be computationally demanding to run, a distributed network of computers may be used for running different modules, leaving only the main simulation loop to run at the user's local computer. This puts high demands on the modularity and interfaces between modules.
3. SIMULATOR MODULES
Illustrations of a DP operated semi-submersible and its simulation modules are shown in Figs.3 and 4, respectively. Details of the models used are found in [1] and [5], and in the references therein. Here we will present some of importance to the simulation case presented later in the paper.
3.1 Hydrodynamics
Environment module: The environment module generates winds, waves and current. The wind is given by direction and velocity, and may be generated by a wind spectrum. The sea state is given by a set of harmonic wave components, which are generated from a two-dimensional wave spectrum (frequency and direction). Each harmonic wave component is given by its direction, frequency, amplitude and phase. The module generates two current outputs. Only the surface current is needed for a surface vessel, whereas the complete current profile is needed for submersed modules, like a riser or anchoring module. The current profile is time and spatial varying, and given by depth, direction and velocity.
Vessel module: The vessel model is divided in a wave-frequency (WF) and a low-frequency (LF) part. The WF motion may be given by transfer functions, and the LF dynamic model may be as shown in equation (1). The inputs are the environmental loads and the interaction forces from thrusters and the external connected systems, e.g. a drilling riser. The outputs are the vessel position and orientation vectors in an Earth-fixed frame of reference, and velocity and acceleration vectors in a body-fixed frame of reference.
Thruster and shaft module: The propeller thrust and torque are for this application given from conventional thrust and torque curves as function of advance number. It may also include advanced thrust loss models for extreme seas, in which case detailed information about waves, current and vessel motion is required. The shaft is modelled as a rotational mass, with propeller speed given from motor torque and propeller load torque.
3.2 Structural Mechanics
Riser module: The finite element model (FEM) of the riser mechanics takes the vessel motion and the depth and time varying current profile as input, and gives the riser displacement, top and bottom riser angles and the interaction force with the vessel as output.
3.3 Machinery Systems
Prime movers: This module includes models of diesel engines and gas turbines.
Power system module: The power system model gives the actuator motor dynamics, and for an azimuthing thruster also the azimuth dynamics. The motor dynamics are currently implemented as a simple 1st order model from commanded torque to motor torque.
Fig.3 DP Class 3 drilling rig.
Fig.4 Illustration of MCSim modules.
(Enlarged Image:52KB) |
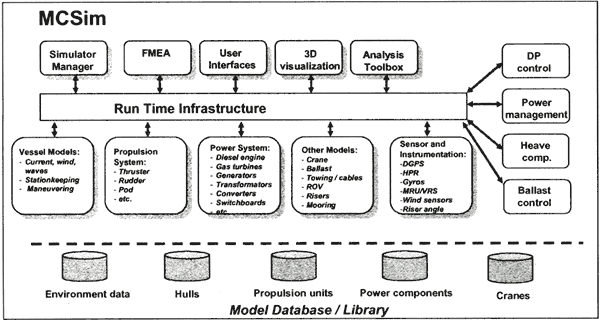 |
|