<4> 知識依存型モジュラー修理(Knowledge−Based Modular Repair)
期間:1999年9月〜2002年6月、コスト総額:360万ドル(造船所120万ドル、NSRP ASE 120万ドル、NIST 120万ドル)
本プロジェクトは他産業で実施している技術や技法を船舶の修理や改造に導入しようとするもので、アトランティック・マリンと米国標準技術研究所(NIST:National Institute of Standards and Technology)によって実施され、他造船所は参加していない。
プロジェクトは2つのサブプロジェクトに分かれている。1つは修理船が入渠する前に船の改造区域の諸情報を得て、CADモデル化することができれば工程の短縮につながるとの見地から、現在他産業で使われている性能の良い測定機器を試すプロジェクトである。全ての作業に万能な測定機器は無いことが判明し、アトランティック・マリン(モービル)ではトータル・ステーション方式を、アトランティック・マリン(ジャックソンビル)では座標測定器(CMM:Coordinate Measuring Machine)が用いられた。
CMMによるパイプ・セクションの計測 出典:NSRP ASE
トータル・ステーション方式では赤外線やレーザー光が利用されている。本プロジェクトは2002年6月に終っているが、成果として外板を正確に計測し、データをCADモデル化してはめ込み部分を製造した。またLoica 1101 TCRA計測器の自動追尾機能が修理船にも適用出来ることが判明した。
他のサブプロジェクトは修理船への作業員や機材のアクセスを容易にする「フライイング・カーペット(空飛ぶ絨毯)」の適用である。ドックの側壁からケーブルで吊り下げられた「フライイング・カーペット」で船にアクセスしようとするもので、NISTはコンピューター・シミュレーション及び50フィートx5フィートの「フライイング・カーペット」の実物大模型を作り剛性やコントロールの試験を実施した。だだし実用化の可能性は報告されていない。
外板のはめ込み工事 出典:NSRP ASE
(拡大画面:80KB) |
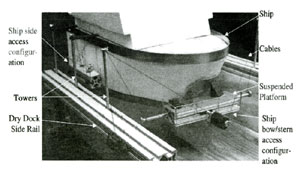 |
フライイング・カーペット 出典:NSRP ASE
<5> 革新的レーザー切断技術による先進構造接合法の開発(Advanced Structural Joining Methods)
期間:1999年8月〜2002年11月、コスト総額:650万ドル(造船所430万ドル、NSRP ASE 220万ドル)
ベンダー造船が中心のプロジェクトであるが他にキャタピラー、EWI、およびIPSCOスチールが参加している。ベンダー造船のモービル工場は本プロジェクトを実施して、米国で最初のレーザー切断機を導入し、建造コストとサイクルタイムを大幅に減らすことが出来た。ベンダー造船は本プロジェクトの契約後2週間にわたりレーザー・ベンチマーク調査団をヨーロッパの造船所に派遣し、レーザー切断機の導入に踏み切った。実際に導入したのは日本のTanaka LMVIIIレーザー切断機(150万ドル)とCNCプレス・ブレーキ(100万ドル)であった。レーザー切断は加工精度が良いので、接合に溶接を使用しないはめ込み式ジョイント(Tab & Slot)が可能である。ベンダー造船ではDDG−51の一部を同社で設計したはめ込み式構造とすることに海軍関係者が興味を持っていると言っているが、実際にはめ込み式が利用されたかどうか不明である。
出典:NSRP/NAVSEA
<6> 船舶構造のロボット溶接用制御プログラムの自動生成(AUTOGEN:Automatic Generation of Control Programs)
期間:1999年8月〜2002年11月、コスト総額:157万3,000ドル(造船所78万4,000ドル、NSRP ASE 78万9,000ドル)
インガルスとサンデイア研究所により実施され、他造船所は参加していない。AUTOGENはCADデータ、溶接のパラメーター表、生産計画情報から自動的にロボット溶接用制御プログラムを作り、従来人間が時間をかけてやっていた作業を短縮して、溶接ロボットの能力を充分に生産ラインの中に取込もうとするプロジェクトである。本プロジェクトは2002年11月までとなっているが、5ヶ月ほど早く完了した。2001年12月にはAUTOGENシステムの最初のデモンストレーションがサンデイア研究所で行われ大成功を収めた。本制御プログラム作成時問はコンピューター(Windows 2000)で8分以下である。
<7> 船舶コンポーネント工場(Ship Component Factory)
期間:1999年8月〜2001年3月、コスト総額:2,111万8,000ドル(造船所2,055万9,000ドル、NSRP ASE 55万9,000ドル)
ハルター・マリンとオランダのコンサルタントグループのみにより実施され、他の造船所は参加していない。本プロジェクトは部材もブロックも外部の工場で製造され、造船所は組み立てるのみというコンセプトの実現可能性研究である。成果としては1999年第3四半期に研究が完成し、2000年第4四半期には設備設計が完了している。本プロジェクトの結論はNSRP内部で余り重要視されていない。
<8> 超高圧ウォーター・ブラスティング(Ultra−High Pressure Water Blasting)
期間:2000年4月〜2002年4月、コスト総額:57万ドル(造船所28万3,000ドル、NSRP ASE 28万7,000ドル)
アトランティック・マリンが中心となり、他にトッド・パシフィック、Munro & Associates、Dana M.Austin環境コンサルタントが参加している。超高圧とは25,000psi(1,758kg/cm2)以上の圧力を指している1。超高圧ウォーター・ブラスティング(UHPWB)の技術は既存の技術であり、すでに実用化されているが、本プロジェクトによりさらにコストを下げ、本プロセスの結果として出るストーム水による環境汚染を減らす方法を見出そうとするもので、むしろリーン生産方式の一部と考えてしかるべきプロジェクトである。
修理船の外板の塗装除去に伝統的に使われてきたグリッドによる乾式ブラスティングは環境上に問題があり、1980年代初期にはブラスティングと同時に真空機構で使用済みのグリッドを吸入する装置を直接船体に取り付けたり、1990年代に入ると船体の作業部分を覆ったりした。これらの技術は現在も使われている。1993年にワシントン州バンガーにある海軍修理工場で初めて水とグリッドの混合物を空気圧で吹き付けるスラリー・ブラスティングが利用された。一方NSRPは当時使われ始めていたUHPWBの広範な使用を目的としたプロジェクトを発足させ、1998年報告書を出している。この報告書によればUHPWBの生産性(平方フィート/時間/機械)は下記である。
出典:NSRP/NAVSEA
・スポット・ブラスティング及び掃除(手動ガン) |
146〜365 |
・選択ストリッピング(手動ガン) |
48〜115 |
・素地金属となるまでの処理(手動ガン) |
152 |
・素地金属となるまでの処理(クローズ・ループ機械) |
121〜146 |
・素地金属となるまでの処理(ロボット機械) |
162〜791 |
UHPWBの効率を上げるには自動あるいは半自動のロボット機械を使わなければならない。海軍では1997年及び1999年航空母艦の甲板の10〜12mm厚エポキシ/ポリアミド滑り止め塗装各20万平方フィートの処理にUHPWBを適用している。以上のような状況のなか、2000年4月にUHPWBの性能向上を目指したNSRP ASEの本プロジェクトが発足した。本プロジェクトでアトランティック・マリンは新しい機械を開発し、リーン製造方式を適用して効率を上げ、さらに排水中の金属除去の技術を比較して、電気パルスシステム(Electric−Pulse System)が最適であるとの結論に達している。アトランティック・マリンは本プロジェクトによりリーン製造方式を適用した駆逐艦と以前の駆逐艦を比較した結果下記の成果があったと報告している。
1 PSI:ポンド/平方インチ 1psi=約0.07kg/cm2
・全体的プロセスの生産性が38%以上向上した。
・作業中のブラスト・ガン使用率が24%から47%に向上した。
・セットアップ時間が半分に減った。
・待ち時間が42%から19%に減った。
・平方フィート当たりの工数が38%減った。
・ガロン当たりの廃水処理コストが94%減った。
<9> 厚板鋼セクション材のレーザー補助酸素切断(LASOX:Laser−Assisted Oxygen Cutting for Thick Steel Sections)
期間:2001年10月〜2003年9月、コスト総額:134万4,000ドル(造船所67万2,000ドル、NSRP ASE 67万2,000ドル)
ベンダー造船が中心となりキャタピラー、BOC Gases、アラバマ・レーザー・システム、エレクトリック・ボートが参加している。機器の開発はアラバマ・レーザーが担当した。レーザー補助酸素切断ではきれいな切り口が得られ、厚板のセクション材の切断が可能である。2002年プロジェクトチームはアラバマ・レーザーに集まりAlpha LASOXシステムのデモンストレーションに立ち会った。このシステムは本プロジェクトのために特別に開発されたLASOXヘッド・ノズルを備え1.5kWレーザーで25mm鋼板の切断に成功した。プロジェクトチームはさらにBeta LASOXシステムの開発に取り組んでいる。最終目標は6kWレーザーで100mmの板厚を切断することである。本開発が終了次第LASOXはベンダーで使用され、続いてキャタピラー、エレクトリック・ボートに導入される予定である。また米国内の造船所にはディスカウントで販売される。
出典:NSRP/NAVSEA
|