EXPERIMENTAL STUDY ON AT-SEA JOINING METHOD FOR LARGE FLOATING STRUCTURE USING SMA
Kiyoshi Shingu1, Takashi Mizota1 and Yoshifumi Takaishi2
1Department of Oceanic Architecture and Engineering, Nihon University
Chiba, JAPAN
kshingu@shinguu2.cs.cst.nihon-u.ac.jp
2Nihon University
Tokyo, JAPAN
ABSTRACT
This study is on secondary drawing and fixing technique in construction of very large floating structures (VLFS) represented as the Mega-Float. In constructing a large floating structure, many units are made in dock separately and towed to the settle region one after another. Under the influence of waves at sea, the units are joined to become a VLFS. Existing methods of joining by secondary drawing and fixing include some problems. To solve these problems and improve safety and construction efficiency, a new technique of joining jig using shape memory alloys (SMAs) are proposed. SMAs have distinct characteristics of shape memory effect and superelasticity controllable by temperature. This paper reports the results of the joining experiment using floating body models. The joining jigs make it possible to combine two remote floating bodies by drawing each other against disturbance of waves, controlling stiffness and transformation of SMAs continuously by Joule heat of electric conduction in the alloys.
INTRODUCTION
In construction of a VLFS, the "at-sea joining" for connecting and integrating separate floating units at a specific sea site is one basic technique of central importance. In the Mega-Float studies validation experiments, which began in 1994, have been executed by Technological Research Association of Mega-Float where various proposals have been executed (1996, 1997, 1998, 1999). A number of units constituting a floating structure are made in docks separately and towed to a specific sea site. These towed units are then joined using proper techniques to avoid the influence of waves, and thereby constructing a large marine floating structure. This study intends to develop a new technique for the secondary drawing and fixing of units in the at-sea joining process. The current secondary drawing and fixing techniques widely used have a number of problems including one likely to have great impact forces on the floating units being rolled and pitched together by external forces such as waves. Finding an appropriate solution to these problems will contribute greatly to the safety and workability of the at-sea joining process. Therefore, we propose a new joining method using SMAs.
AT-SEA JOINING
Procedure for At-Sea Joining
In general, an at-sea joining of a large marine floating structure is executed in the following procedure (Shimamune et. al., 1998):
Building floating body units in a dock: Floating body units are built in advance at a dock.
↓
Towing of the dock-built floating body units: Dock-built floating body units are set afloat and then towed to a specified site at sea for installation.
↓
Primary drawing of floating body units: A floating body unit to be newly installed is pulled to the range within tens of centimeters from the final position of the floating body.
↓
Secondary drawing of floating body units: Towed floating body units are placed in contact with each other and then installed at the specified location.
↓
Cutoff and drain of water: Water is cutoff and drained from the floating body units.
↓
Fixing of floating body units: Floating body units are fixed together to enhance their stability.
↓
Welding of floating body units: Floating body units are welded.
It has been proven that in the above process flow, the primary drawing of floating body units can be executed basically in the same manner as the alongside pier procedures for bringing a ship to a quay. The process flow from the secondary drawing of floating body units to the fixing of floating body units is hereafter referred simply to as the "drawing and fixing" process.
Means for Drawing and Fixing
In general, when joining two independently oscillating floating body units together, external forces acting on the joint of these two floating body units can be divided into Fx, Fy, and Fz components of axial forces in the directions of X, Y, and Z, and into Mx, My, and Mz components of moments around each of the three axes, respectively as shown in Figure 1. However, in the drawing and fixing process where waves act as actual external forces, load Fz in the vertical direction, moment Mx in the abutting direction, and load Fy in the horizontal direction each play an important role. In order to join floating body units while enduring these external forces, it is necessary for the floating body units to have a joining jig that has a strength durable enough to withstand the braking force and its reaction force so as to converge the relative motions among the adjacent floating body units gradually, and finally to turn these floating body units into a fixed unit. This joining jig needs to have a guide-like function of converging the relative motions of the floating body units and finally guiding the units to their joining positions, a pressurizing function that applies a force necessary to deal with the guide-like function, and further a function that restrains minute fluctuations of the floating body units during the final stage of fixing.
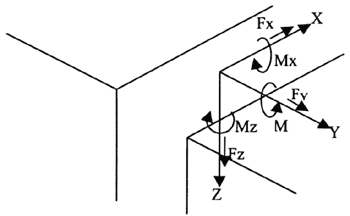
Figure 1. External forces applied to floating body units
AT-SEA JOINING USING SMAs
Fundamental characteristics of SMAs
A SMA can memorize its shapes by heat-treatment for about one hour at a temperature
ranging from 300℃ to 600℃. Once a SMA is heat-treated to higher than the Af point (Austen aging point,
around 120℃ in this study), no strain remains in it even when an external force is applied to it (the
elastic limit is in a range of 6-8%). Furthermore, at a temperature lower than the Mf point (Martenaging
point, around 30℃ in this study), when an external force is applied to a heat-treated SMA, apparent plastic
strain remains intact in it even after the external force is taken away from it. However, when a SMA is
heat-treated to a point higher than the Af point, keeping its apparent elastic strain as it is, the elastic
strain is eliminated, and the alloy can restore its original shape. Then, the elastic modulus of the alloy
varies continuously with temperature ( Industrial Material Center, 1991).
Procedure for At-Sea Joining using SMAs
After a floating body unit to be newly joined to the existing floating body unit at a prescribed site at sea is drawn to a position as near as tens of centimeters at the primary step, SMAs are attached to the new floating body unit at normal temperature (in the martensitic phase). Since the stiffness of the SMAs are slight, the use of the at-sea joining jigs affects fewer of the oscillations of those floating body units. Then, the temperature of the SMAs are raised, the deck of the new floating body unit is made to contact that of the existing floating body unit, the tops of two bodies abutted, water between the two bodies drained, and finally the bottoms abutted. After that, in order to enhance their stability within a few millimeters as required for welding, the temperature of the SMAs of two units is raised to fix the units together.
|