4.2 燃料油
1)ディーゼルエンジンの燃料油としては
(1)小型高速機関はほとんど軽油(JIS2号軽油相当)
(2)中小型の中高速機関はA重油(JIS1種2号重油相当)
(3)中型低速機関はA重油またはC重油(JIS3種2号重油相当)
(4)大型低速機関はC重油
2)燃料油の精製
燃料油の種類は原油の精製の過程で決まる。
2・184図に石油製品の製造過程の概念を示すが、原油から蒸留、分解、混合の過程を経て製品が作り出される。この製造過程の中で基本的な留分はガス、ガソリン、灯油、軽油、残渣油である。
A‐C重油はこの中の軽油と残渣油を適当に混合して所定の粘度に混合したものである。
2・184図 常圧蒸留装置
(拡大画面:18KB) |
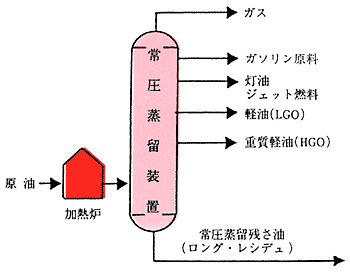 |
A重油はその90%以上が軽油分であるが
C重油は基材となる残査油の粘度と、軽油等の低粘度油との混合割合で必要な粘度が決まるので、その組み合わせは無数にある。
3)分解重油の製法と注意
前述の常圧蒸留装置(或いは減圧蒸留装置)では軽質留分の比率が少なく、50%程度は残渣油として残る。
一方近年は、ガソリン、軽油等の需要が増大しておりこの需要のバランスを確保するために残渣分から軽油分、軽油分からはガソリンを取り出している。これが分解法と呼ばれるもので、この分解法(流動接触分解=FCC、熱分解=ビスブレーキング)で作られた製品には頭に分解を付け分解重油と呼び、蒸留法による製品を直留重油とか頭に直留を付ける。
その製法は2・185図の通りで、直留に比べ精製のより下流にあるため各成分が濃縮された形で密度が高く、硫黄分、残炭分、そしてバナジュウム、ナトリウム等の有害配分の比率が高くなっていることが特徴である。
流動接触分解で作られた重油はFCC油と呼ばれ、触媒のシリカーアルミナが油中に残存してその硬い金属自身が燃料ポンプやピストンとシリンダライナの狭い間に入り物理的な摩耗を短時間の内に起こすので、C重油使用船では補給の際に注意が必要である。同様に分解軽油は直留軽油に比べると密度が高く着火、燃焼がしにくい特性をもっている。基本的には、分解重油は以上のような理由からボイラ用として使用され、船用としては使用しないことになっているが、外国では舶用機関に供給されたことがあり、国内では陸用のディーゼルエンジンに使用される可能性がある。
2・185図 接触分解装置とビスブレカを有する精製過程
(拡大画面:41KB) |
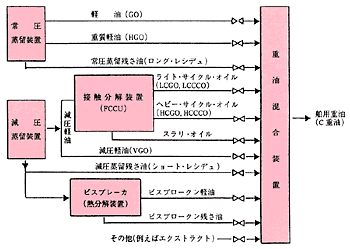 |
4)燃料油の性状
燃料油中には種々の成分が存在すると同時に、燃料油自身の性状は機関運転や船内設備に大きな影響を与える。2・15表にこれらの関係をまとめた。
2・15表 燃料油の成分、性状と機関への影響
性状 |
性状変化 |
機関への影響 |
機関 |
影響 |
比重(密度) |
高比重化 |
遠心清浄機 |
・清浄困難 スラッジおよび水分難困難 |
タンク |
・水分離困難 |
粘度 |
高粘度化 |
油加熱器 |
・加熱容量不足
・高温加熱による重油の分解 |
ポンプ |
・移送困難 |
遠心清浄機 |
・清浄困難 |
ディーゼル機関 |
・加熱不足による不整噴射
・燃焼不良による熱負荷増大 |
硫黄分 |
増加 |
ディーゼル機関 |
・低温腐食(シリンダライナ、燃料弁、過給器) |
残留炭素分 |
増加 |
ディーゼル機関 |
・燃焼不良
・汚れ、堆積物増加(燃焼室、排気系統) ・摩耗増加(シリンダライナ、ピストンリング) ・カーボンフラワ生成 |
アスファルテン |
増加 |
ディーゼル機関 |
・燃焼不良、燃焼悪化
・ライナ壁衝撃荷重増大 ・熱負荷増大 ・すす発生 ・スティック(燃料ポンプ、燃料弁) |
灰分 |
増加 |
ディーゼル機関 |
・堆積物増加(燃焼系、排気系)
・摩耗増加(シリンダライナ、ピストンリング) |
水分 |
増加 |
ディーゼル機関 |
・燃焼不良
・高・低温腐食 ・堆積物増加 |
バナジウム ナトリウム |
増加 |
ディーゼル機関 |
・高温腐食(燃焼室壁)
・堆積物増加(排気系、過給器) |
シリカ アルミュニウム |
増加 |
ディーゼル機関 |
・異常摩耗(ピストンリング、シリンダ・ライナ等) |
セタン価 CCAI |
低下 高 |
ディーゼル機関 |
・始動性不良
・燃焼性不良 |
混合安定性 |
低下 |
タンク |
・スラッジ堆積 |
遠心清浄機 |
・清浄困難 |
ストレーナ |
・閉塞 |
ディーゼル機関 |
・燃焼残査の増加 |
スラッジ |
増加 |
タンク |
・スラッジ堆積 |
遠心清浄機 |
・清浄困難 |
ストレーナ |
・閉塞 |
|
(1)比重・・・比重そのものは機関の運転には影響しないが、高比重の燃料油は遠心清浄機による水分分離が困難になる。
(2)粘度・・・ディーゼル機関は良好な燃焼を得るため、適切な粘度の燃料油を使用することが必要で、C重油を使用する場合は加熱をしている。
(3)硫黄分・・・燃料油中の硫黄分は燃焼により亜硫酸ガスとなり、水と化合して硫酸となって各部に腐食を起こす。
(4)残留炭素分・・・多いと燃焼が出来ず燃焼室内に堆積物を増加させる。
(5)アスファルテン・・・難燃焼性があるため触火面の近くで燃え、温度上昇をさせる。また増加することにより熱安定性、混合安定性が低下し油中にスラッジを生じ易い。
(6)灰分・・・燃焼しないため堆積物や摩耗の原因となる。
(7)水分・・・燃焼不良や堆積物の原因となる。
(8)バナジュウム、ナトリウム・・・高温腐食の原因となる。
(9)着火性(セタン価、セタン指数)・・・機関の始動や円滑な運転に必要。
(10)混合安定性・・・分解油と直留油を混合すると、混合比によってスラッジが多量に発生することがある。
近年では海水でエンジンを直接冷却することは、少なくなってきた。ここでは清水冷却についてのみ注意事項を述べる。
1)冷却水の選定基準
清水であっても機関に使用される清水の選定には注意を要する。冷却水の水質基準を2・16表に示す。
2・16表 清水冷却の水質基準
No |
項目 |
単位 |
推奨値 |
1 |
濁度 |
|
10 |
2 |
PH(25℃) |
|
6−8.5 |
3 |
電気伝導度 |
μΩ/cm |
<400 |
4 |
Mアルカリ度(CaCO3) |
ppm |
<150 |
5 |
全硬度(CaCO3) |
ppm |
<100 |
6 |
塩素イオン(C1-) |
ppm |
<100 |
7 |
硫酸イオン(SO42-) |
ppm |
<100 |
8 |
アンモニアイオン(NH4+) |
ppm |
<10 |
9 |
硫黄イオン(SO2-) |
ppm |
−− |
10 |
硫化水素(H2S) |
ppm |
<10 |
11 |
全鉄(Fe) |
ppm |
<1.0 |
12 |
シリカ(SiO2) |
ppm |
<50 |
13 |
全蒸発残留物 |
ppm |
<400 |
14 |
マンガン |
ppm |
<0.2 |
|
(1)冷却水中に溶けている物質によっては腐食、スケール、あるいはスイラム(藻)障害を生ずる。
(2)腐食傷害は各種塩化物によることが多く、塩素イオンがその代表的なものである。
(3)その他腐食性を判断する要素としては、pH、電気伝導度、Mアルカリ度、アンモニア度を調べる必要がある。
(4)スケール障害はカルシュウム、マグネシュウムに起因することが多く、冷却器の冷却効果の低下や、高温部の亀裂の原因となる。
(5)アンモニア分は冷却器のアルブラック管を腐食させるので注意を要する。
(6)シリカ、マンガン、全鉄等も硬質スケールの原因となる。
2)冷却水防錆剤
シリンダライナの外周部やシリンダジャケットの冷却部にみられる損傷は、一般にキャビテーションまたは電気化学的腐食によるものといわれている。
この腐食を防止するために、冷却水に防錆剤(インヒビタ)を適量投入することで金属表面に強い安定した保護被服膜を形成させる。
通常使用される防錆剤としては
(イ)亜硝酸塩系・・・毒性は少ないが排水の投棄の際はpH及びCOD値規制の対象となる。一番良く使用されている。
(ロ)珪酸塩系・・・毒性はまったく無く、排水の投棄は同上の注意が必要。
(ハ)酵素系・・・毒性がまったく無く、そのまま投棄できる。
防錆剤の使用に当っては、次のような注意が必要である。
(イ)防錆剤の投入法、濃度管理、廃液処理等は各メーカで差があるので、使用に際しては各メーカの指示に従うこと。
(ロ)冷却水に不凍液が投入してあると互いに影響し合う場合があるのでメーカの指示によること。
(ハ)濃度が適正でないと効果が発輝できないので各メーカの基準値に従うこと。
(ニ)濃度基準値の測定は各メーカ指定の濃度測定器を使用すること。
(ホ)冷却水中に塩分(海水混入)があると効果がでないので、投入前に塩分測定をする。
注記:COD値
廃水を清水(海水)中に添加すると、水中の酸素を還元し酸欠状態となる。
これを避けるために必要な酸素量をCOD−( )PPMとして表示する。このCOD値を満足させる方法としては、水での希釈、空気を吹き込む、酸化剤を投入するなどの方法がある。
3)腐食を発生させない注意
冷却水への空気の混入は溶存酸素の含有量を増加させ腐食を助長させることになるため次のことに注意する。
(1)空気の溜まる恐れのある場所(特に冷却水管系の最も高いところ)には必ず空気抜きを設ける。
(2)清水膨張タンクには必要なヘッド(機関冷却水出口位置から3m以上)をもたせ、冷却水圧力を上げて気化現象を押さえる。
(3)清水膨張タンク内には冷却水の動揺防止のために適当な仕切を設ける。
|