The above mentioned results are as follows. The part on the sliding surface reaches the extreme high temperature over transformation temperature by thermal energy with the occurrence of the scuffing damage. The white layer on the sliding surface occurred by martensitic transformation. That is, the part cementite Fe3C in the sliding surface vicinity dissolved again and was rapidly cooled, in this time, carbon was dissolved supersaturatedly. The structure of martensite which occurred by rapid heating and cooling is difficult to be corroded, and the hardness is high and the toughness lowers.
5. SUMMARY
Scuffing tests by the two rollers were carried out using the newly developed WRS (Wear Resisting Steel) without and with surface modification treatment. After scuffing tests, sliding surface, circumferential and axial cross section at (σh)s =80 % mainly were investigated, and the scuffing damage aspects were examined.
The results obtained are as follows.
1) The scuffing characteristics depend on the surface hardness. On WRS-370Hv, (pmax)s was higher and μs is lower than those on WRS-860Hv. (pmax)s of WRS-370Hv, WRS- 860Hv and SUJ2 were respectively 2.1 GPa, 1.5 GPa and 1.0 GPa, and the anti-scuffing characteristics of WRS was very good. As there is no self-lubricating on SUJ2, (pmax)s is low and μs becomes high for either (σh)s,. In addition, on SUJ2, (Tb)s is lower than WRS, and Λs becmes higher.
2) For (σh)s = 60 % μs of the Ni-P plating was /μs=0.08, for (σh)s =70 〜90% μs = 0.08, almost fixed. For (σh)s≧ 80 %, μs lowered from that of WRS without treatment. The sulphurizing specimen shows characteristics of the base material, since sulphurizing layer on the sliding surface disappeares at the initial load step of the scuffing test.
3) The average damage widths are proportional for (pmax)s. For (σh)s = 80 %, they were respectively 4.0 mm, 3.8 mm, 1.4 mm and 6.0 mm. Though damage width of the Ni-P plating was about 6.0 mm, the damage of the Ni-P plating layer was heterogeneous.
Table 1 Chemical Compositions of Specimen (wt%)

Table 2 Example of Mechanical and Physical Properties of WRS
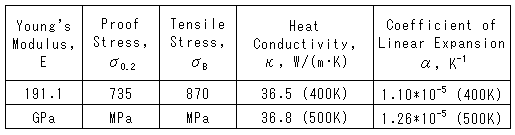
4) As large Hertzian stress affected on the Ni-P specimen, μs rose a little and the number of rotation increased at (σh)s = 60 %, the Ni-P plating might cause the rolling fatigue. The thin Ni-P plating was intermittently recognized, but white layer could not be recognized on sliding surface. The cracks existed in surface vicinity of base material.
On the other hand the white layer existed at 30〜50 μm thickness on surface of the Ni-P specimen at (σh)s = 80 %.
5) The white layer on the sliding surface seems to occur by martensitic transformation. According to XRD result of scuffing damage surface of the Ni-P plating specimen at (σh)s=60 % and 80 %, the main products were Fe, Fe3C and FeO, and the products which corresponded for other specifically did not come. The white layer is the composition equal to the base material. The hardness of the white layer were almost 510〜570 DH115, (Hv≧700).
Judging from heat treatment condition and composition and mechanical properties of the specimen, it is estimated that the position of 30〜50μm of the sliding surface becomes very much a high temperature over the transformation temperature (about 1073 K).
REFERENCE
1) Tetsugo Fukuda, Symposium / Keynote Lecture, (1998) p.192
2) Kenzo Miura, et. al, J. of Marine Engineering Society Japan, 35 (1996) p.389
3) Toshihiko Iwano, et. al, Machine Technology, 30 (1982) p.68
4) Akira Yoshida, Kenzo Miura, et. al, J. of Japan Society of Mechanical Engineering (C), 64 (1998) p.1041 etc.
Table 3 Properties of # 83 Turbine Oil
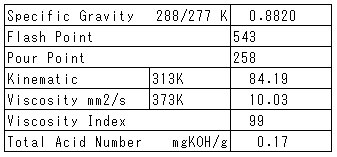
Table 4 List of Specific Sliding (σh)s, Maximum Hertzian Stress (pmax)s, Friction Coefficient μs in Scuffing Initiation
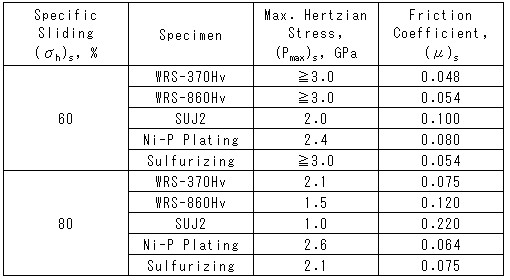
BACK CONTENTS NEXT