The latest top piston ring design is based on a "gas-tight" seal and controlled exhaust gas relief grooves to control the pressure drop across this ring. This allows operation with optimum pressure on the rings and thus optimum loading on the oil film (Fig. 3).
Figure 4 shows the combustion chamber temperatures measured on the testbed on an MAN B&W K98 engine with the above mentioned design features. It shows that at the top dead centre position of the top ting, the mean temperature on the liner surface is 216℃. In the 90 cm bore design engine at the same load, this temperature was measured at 240℃, which effectively means that the liner temperature has even been reduced, compared with the previous combustion chamber design.
Figure 4. MAN B&W K98 Engine Combustion Chamber Temperatures
When the engine is in actual operation, at sea or in a power station, higher temperatures may be experienced. Fouling due to fuel oil and lube oil based deposits, pressure drop in gas ways and operation under extreme ambient conditions can all result in an increase in component temperatures by up to 50℃.
The task for an oil company is to develop lube oils in close cooperation with engine designers to ensure that the oil performs acceptably in the engine designs on the market. A safety margin must be built into the oil design to cope with a further development of the engine in coming years and, more importantly, to allow for occasional local temperatures beyond design values. Even when the component temperatures remain unchanged at increased power outputs, as a result of effective design countermeasures, thermal loading in the combustion chamber will increase if more power is to be obtained with an unchanged, or improved, thermal efficiency of the engine.
The maximum temperature regime the cylinder oil must be able to cope with could be as high as 300℃, however, even though the successful efforts of the engine designers has meant that the mean temperature met by the cylinder lubricant has not changed dramatically.
3. PREVIOUS WEAR STUDIES
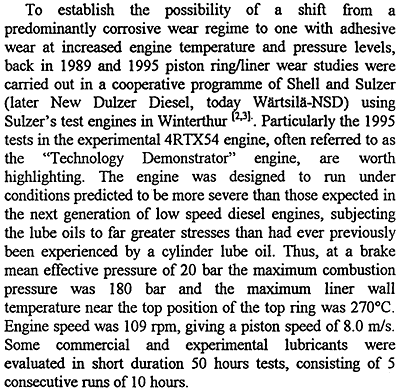
It was found that high alkalinity 100 BN oils were required to provide adequate wear protection with 3.5 %m sulphur heavy fuel. Close examination of the liner surfaces showed preferential corrosive liberation of the hard phase to be the prime wear mechanism and abrasion of the pearlite matrix by the liberated hard phase to be secondary. No sign of scuffing wear was ever experienced. Hence, from these observations it was concluded that corrosion is the likely predominant wear mechanism that will determine the wear rate in the next generation of engines, whereas adhesive wear will probably not be significant.
That cold corrosion indeed still plays a role in some of today's engines may be illustrated with the need for liner insulation ('Haramaki') and longer Teflon cooling bore inserts to reduce corrosive wear experienced in the first generation of WNSD RTA84T and RTA96C engines. This high wear is predominantly found in the mid-stroke region and at part load operation [4,5]
4. CORROSIVE WEAR
It came much as a surprise that cold corrosion was the predominant wear mechanism in the 4RTX54 study, since the often quoted "Shell Acid Dew Point Curves" tentatively predict an acid dew point of only approximately 180℃ with a 3.5%m sulphur fuel at a pressure of 180 bar [6,7]. These dew point curves, each valid at a certain pressure, show the temperature below which aqueous sulphuric acid condenses versus the sulphur content of the fuel (Fig. 5). They were defined on basis of a degree of SO2 conversion of 2.5% (see below), an air water vapour content of 5% and an air-to-fuel ratio of 35:1 (kg:kg).
In other words, with liner surface temperatures at 270℃ the acid components are expected to remain fully in the gas phase at 180 bar pressure. The small amounts of these components that eventually may diffuse into the oil layer protecting the liner surface will be readily neutralised by the excess overbased additives in the lube oil, hence providing maximum protection against corrosive attack. Only when the temperature of the liner gets below the acid dew point, condensation of acid is possible and the corrosive liquid phase, assumed to consist mainly of sulphuric acid and water, will pose a much more serious challenge to protection by the lubricating oil.