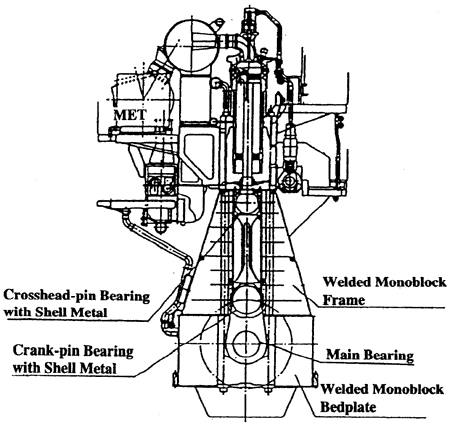
Fig. 1 Construction of UEC75/85LS II Engine
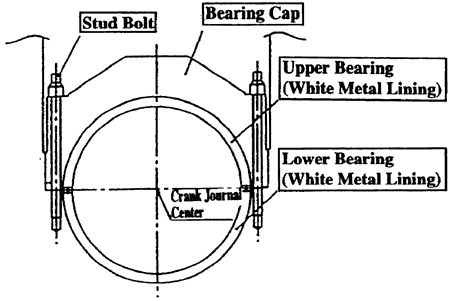
Fig. 2 Main Bearing Structure
Table 1 Main Dimension of The Main Bearing
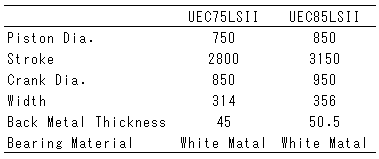
To evaluate the high oil film pressure more precisely, an original high response pressure sensor with minimized pressure leading hole volume has been developed. This sensor is installed on journal surface on rotating side and verified with a testing machine with 1/2 to 1/3 scale model bearing whose three-dimensional position and load can be controlled. This paper consists of the test result obtained as actual data of oil film pressure distribution and, its comparison with Elastohydro-dynamic Lubrication (EHD) analysis and inspection to prove generation of white metal damage by oil film pressure.
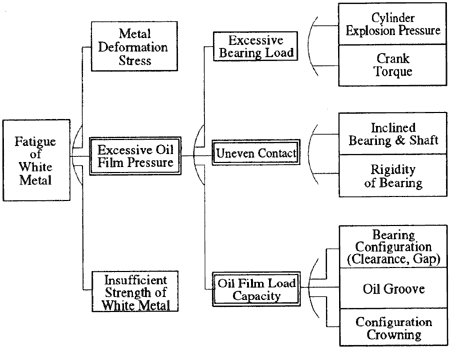
Fig. 3 Factors of Fatigue Failure in Main Bearring's White Metal
2. ELASTOHYDRODYNAMIC LUBRICATION ANALYSIS
Accurate estimation and evaluation of oil film pressure are indispensable to assure reliability of engines, because excessive pressure in main bearing causes white metal's fatigue failure when acting periodically under fluctuating load. This is the reason for developing highly accurate bearing characteristics evaluation method, using EHD theory for bearing with uneven contact and under fluctuating load. This method is applied to designing and evaluating main bearing of UEC engines. EHD analysis method enables oil film analysis in actual bearing clearance configuration by considering local influence of bearing surface defonnation, derived from coupling of oil film pressure and elastic deformation of bearing surface. Compared with existing method which assumes bearing as rigid body, estimation accuracy has been greately improved. It is also made possible to evaluate quantitative bearing characteristics.
The following is the basic equation for EHD analysis.
Tuo-dimensional incompressible Reynolds equation can be expressed as follows;

where, in addition to geometric clearance and uneven contact of shaft, elastic deformation [L]p is added to oil film thickness H.
This is an influence coefficient matrix (compliance matrix) which relates oil film pressure with deformation amount on bearing surface.
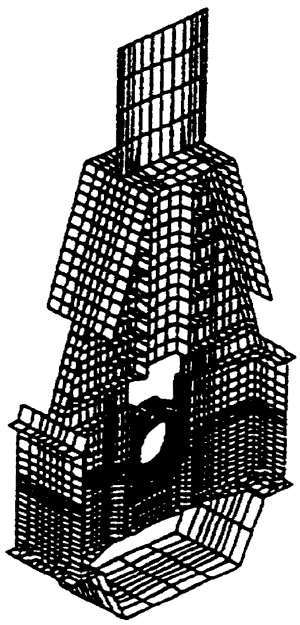
Fig. 4 FEM Model for Engine Frame
BACK CONTENTS NEXT