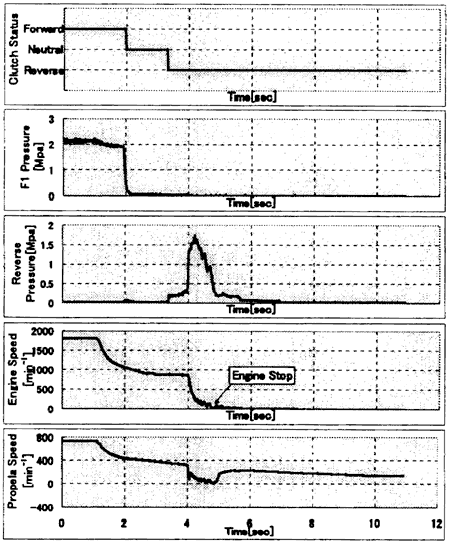
Fig. 8 Crash Astern (Not Controlled)
We used the Low gear to quickly obtain the maximum boat speed and shifted to High gear at automatic shift. Then, the time to reach the maximum boat speed had been reduced to 35 seconds without intermittent power transmission, decreased by 30%, although 50 seconds were required in the condition of fixed high gear. The performance results were approximately the same as we expected. The proper shift timing to improve acceleration and the control of hydraulic pressure to reduce shift shock can be implemented by utilizing electrical control.
(2) Improvement in deceleration property in crash astern
Generally, crash astern is performed by switching the clutch from forward acceleration to backward acceleration at the practical maximum revolutions. However, in this test, engine revolutions have been reduced to idling revolutions at a time of crash astern, following users' operation patterns of the ship used. The hydraulic pressure of the forward/backward clutch operations is controlled by driving the electromagnetic proportional valve of the controller shown in Fig.5.
As for the effects when hydraulic pressure is electrically controlled at a time of crash astern, changes in engine revolutions and the hydraulic pressure of clutch operations are to be compared with those of conventional systems.
In the conventional system in which hydraulic pressure is not controlled (Fig.8), the hydraulic pressure of backward operation rises abruptly along with crash astern. As a result, excessive propeller driving torque is generated, bringing the possibility of engine stall.
If hydraulic pressures are electrically controlled to obtain values shown in formulas (4) and (5), the abrupt rise of the hydraulic pressure of backward acceleration is suppressed, and clutch transmission torque does not exceed engine stall torque. Hydraulic pressure rise is controlled after engine revolutions become stable, thus preventing engine stall (Fig.9)
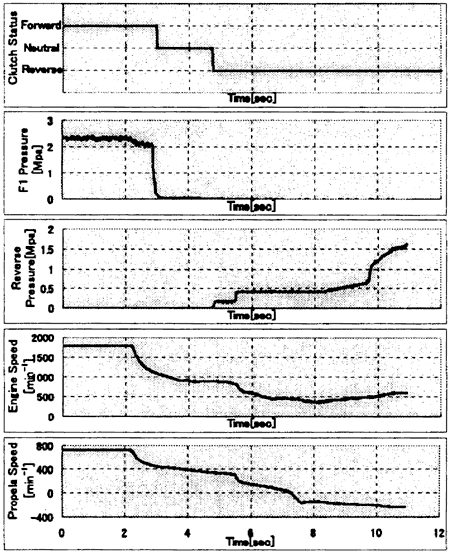
Fig. 9 Crash Astern (Controlled)
4. VALUE ADDED FUNCTION FOR COMMERCIALIZATION
To ensure performance in the test results and to implement commercialization as well, we have added functions and carried out tests as shown below for the purpose of safety and reliability.
4.1 Fail-safe function
As shown in Fig.10, even if troubles occur in the controller system, etc, the clutch operation hydraulic pressure will automatically be raised up to the maximum hydraulic pressure, slip operation will stop, and the reduction gear ratio will be forced to turn to High gear. We have provided fail-safe functions and performed operation, to ensure that no trouble occurs during normal sailing.
1] Power supply to the system shuts down.
2] A sensor indicates abnormal values.
3] Engine revolutions increase to the slip prohibition area.
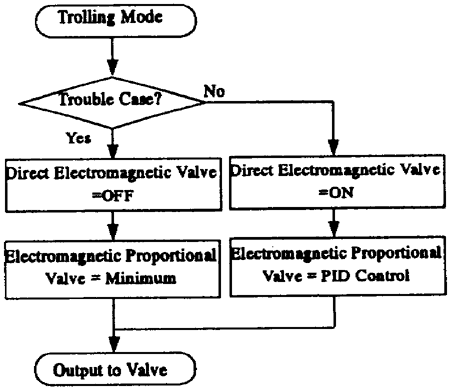
Fig. 10 Fail-Safe Sequence
5. CONCLUSION
By introducing electrically controlled techniques into marine transmission, we have established a means of sufficiently transmitting engine output torque to the propeller. That is, at the time of automatic gear shift and crash astern, engines can supply power to the propeller without engine stall, and acceleration and deceleration properties of ships are improved as shown below;
1] Controlling automatic gear shift and hydraulic pressure allows the implementation of acceleration without shift shock, improving acceleration time by 30%.
2] The optimum hydraulic control that can suppress the abrupt rise of hydraulic pressure of backward acceleration allows the deceleration implementation without engine stall, resulting in crash astern operation up to the engine rated revolutions.
6. REFERENCES
[1] Tamori Nainenkikan., Vol.26, No.333 (1987-7)
[2] Kobayashi Gyosenkikan., Vol.62, No.715 (1986-5)
[3] Harada M.E.S.J., Vol.32, No.4 (1997-4)
[4] Tamori M.E.S.J., Vol.34, No.2 (1999-2)
BACK CONTENTS NEXT