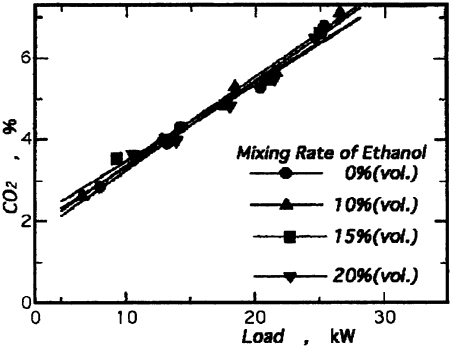
Fig. 7 CO2 Density of Exhaust Gas
Figure 8 shows the pressure history at the same load condition. It is obtained that the ignition lag becomes larger in increasing with ethanol mixing rate. The high latent heat of evaporation of ethanol consumes the heat of chamber, thus the ignition lag becoming larger.
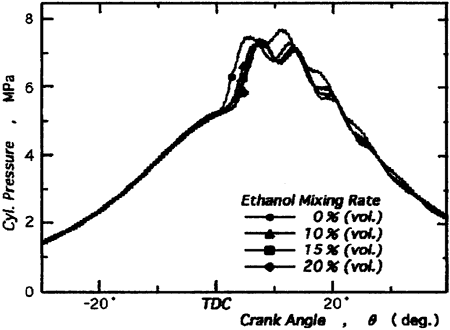
Fig. 8 Combustion Pressure
The thermal efficiency in cases of the mixed fuel with diesel fuel oil and rape-seed oil is shown in Fig.9. It is deduced that the thermal efficiency can be kept constant with addition of 50% (vol.) rape-seed oil to pure diesel fuel oil. In addition of ethanol to the mixed fuel, the thermal efficiency decrease about 2%. Increasing in ethanol blending rate up to 20% (vol.), it is given almost the same declination level of thermal efficiency at 2%.
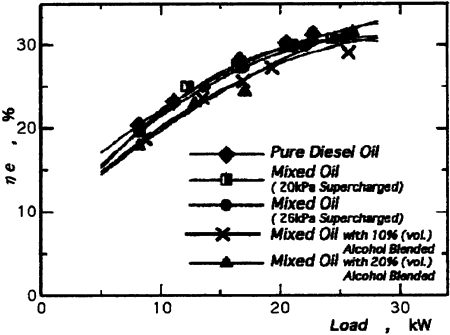
Fig. 9 Effective Thermal Efficiency
NOx density in exhaust emission of the same blending cases with Fig. 9 is shown in Fig. 10. In case of 50% (vol.) rape-seed oil mixed fuel, there is no apparent effect of super-charging of intake air. In comparison with pore diesel fuel oil case, the mixed fuel oil shows higher NOx emission. Ignition lag becomes shorter in case of mixed fuel oil as shown in the pressure history of Fig. 14. It is thought that the component in the rape-seed oil makes shorter ignition delay as well as the spray characteristics due to the change in the kinetic viscosity of fuel oils.
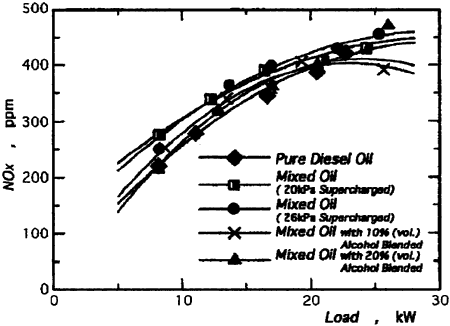
Fig. 10 NOx Density of Exhaust Gas
Figure 11 shows the corrected NOx concentration at 13% O2 in exhaust gas. In this figure, the case of mixed fuel oil with super-charging at 26kPa indicates higher NOx emission compared with others. It is caused by the higher value of air excess ratio in the intake air. As the same tendency with the diesel / ethanol blended fuel cases, NOx density shows slight difference at higher load owing to the relative decreasing in air excess ratio within these load conditions.
BACK CONTENTS NEXT