Fig. 5 Regulation of 6L80MC Main Engine by the Variable Injection Timing Unit (VIT)
According to the VIT regulating principle, fuel injection advance angle is changed corresponding to the load changed.
Δθ1 is calculated from the fuel injection delay angle and the Main Engine speed at the rated conditopn. Δθ2is calculated from the ignition delay period. And the other, when the Main Engine is working in the non-rated condition, the cooling water's temperature is different, and the working condition of turbo charge also varies, except fuel injection system. When the load is low, it is also essential to build the model of emergency filter starting according to the real ship condition.
Δθ1 is fuel injection delay amgle:
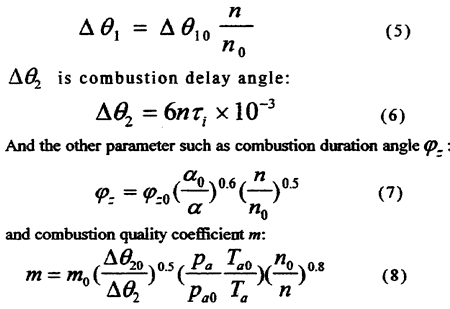
The condition of combustion process is controlled by these combustion dynamic parameters mentioned above, thus above the main engine can be modeled under non-rated condition. By the use of model, the calculation of thermal parameters of main engine was carried out on each working condition point. The calculated results were compared with the data of trial trip report, and the model of the main engine was unproved.
4. MAIN ENGINE FAULT SIMULATION
The faults of main engine are very complex. A single fault model could induce several kinds of fault symptom, and one abnormal symptom could also be resulted by one fault mode or more than one faults. These fault modes are attributed to diverse sub-system. As for the fault simulation for MERS, it has to have the functions such as: Fault setting, Fault simulating, Fault answering and Fault clearing. The abnormal change of engine parameters were investigated theoretically by the use of the Main Engine Simulator Model developed in the previous chapter, and experiment by the use of data provided by Ship Company and marine engineers experiment. According to this investigation, got the change of thermal parameters and symptoms due to fault model could by analyzed[2].
Thus above. the fault model was built by changing the initial condition of the Main Engine model under steady condition. The fault model can give the thermal parameters and symptoms under fault condition.
Here two fault modes as examples are shown.
4.1 One Cyl. Fuel Injection Timing Late
Fault modes : VIT malfunction; opening timing disorder of fuel pump, fuel pump worn, fuel injectors' spring malfunction etc.
Fault modeling: To Change the combustion advance angle as follows: θz = θg + Δθ1 + Δθ2 by the use of the simulation model under steady condition for Main Engine, the fault model can be established.
Conclusions: The fault simulation results are shown in Fig. 8 and Fig. 9.
4.2 Exhaust Valve leakage
Fault modes: Exhaust Valve body malfunctions, exhaust valve opening timing malfunction, exhaust valve spring malfunction etc.
Fault modeling: To change the exhaust valve curves, to extend the exhaust valve opening time, and to change exhaust gas flow. By use of the model under steady condition for Main Engine, fault model be established.
Conclusions: The fault simulation results are shown in Fig. 10 and Fig. 11.
We can see that simulated calculation result is really same as the experiments results of actual ship's technical book. Synthesizing the faults simulation, the SMSC200 can also require the second stage fault caused by error operation, called induced fault. In fault setting, the teaching panel is equipped for giving a fault training command, which is giving a fault code (the code is commonly accepted by all MERS System) and fault mode. Receiving the command, then the Main Engine model react properly, and load the fault model, and change the working condition. At one time, it is also required to the students to answer and do correct operation to clear fault.
Thus above, all the training procedure of fault simulation consists of five steps: setting, running, answering, clearing, and recording.
5. IMPORTANCE OPERATION RESULTS DATABASE OF ACTUAL SHIPS
In order to develop a more effective model of main engine, especially fault model, it is very important to obtain actual ships' operation results and fault data. About new type container ships, there are a few in operation data and fault data. The more comprehensive data could be collected, the better for modeling the fault situation. During this research, however, we have not enough data to check the modeling results. So, it would be desirable helpful to construct the database of actual ships' operation's predominance and the troubles and/or faults by the collection by shipping company, shipyard and research group.