The evaporatcd fractions are collected in a buffer tank, and transported to a water shower scrubber. The gaseous fractions that pass through the shower are burned in the off-gas combustor. The polymer fuel in the mixing tank is then pumped at 0.99 l/min by piston-type pump to the main heater and heated to an appropriate injection temperature. After filtration by a 3 00-mesh filter, the polymer fuel is introduced into the injection pump and injected into the combustion chamber of the diesel engine. The diesel engine and fuel injection pump characteristics are listed in Table 2. The fuel line and fuel injection pump were covered with thermal insulating material. In order to control the temperature of the polymer fuel, the fuel was circulated through the fuel line and the injection pump. The temperature was kept below 150 ℃ as limited by the strength of the injection nozzle at elevated temperature. To enable adjustment of injection timing, an external fuel injection pump was used. Thus, mechanical losses were somewhat higher than those for the standard system. The cylinder pressure history and needle lift were recorded. Smoke number (Bosch) tests and exhaust gas analysis by a fourier transform infrared (FTIR) gas analyzer (HORIBA-MEXA-4000FT) were also performed.
Table 1 The properties of the employed plastics
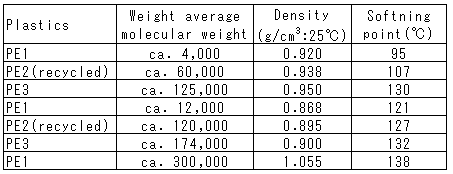
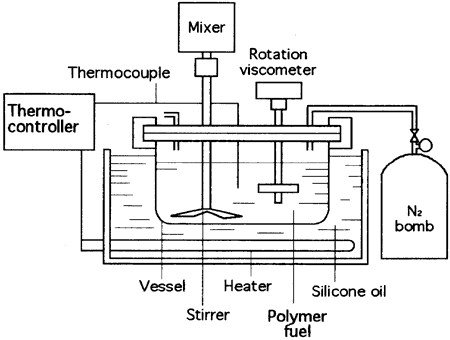
Fig. 1 Experimental apparatus
3. THE CHEMICAL AND PHYSICAL PROPERTIES OF THE NEW POLYMER FUELS
3.1 Viscosity of the Polymer fuels
In order to achieve adequate fuel injection performance, fuel viscosity should be between 1 and 30 cSt [4,5]. Fuel viscosity affects spray characteristics such as droplet size, penetration, and mixture formation, which have a significant influence on combustion and emission characteristics. Therefore, the viscosity of the fuels is very important in evaluating the applicability of polymer fuel as a diesel fuel.
Table 2 Characteristics of the diesel engine and the fuel injection pump
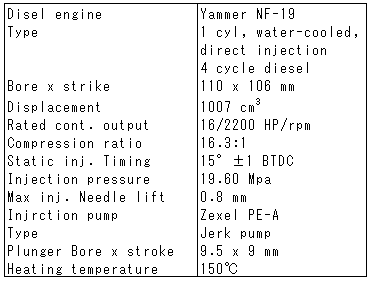
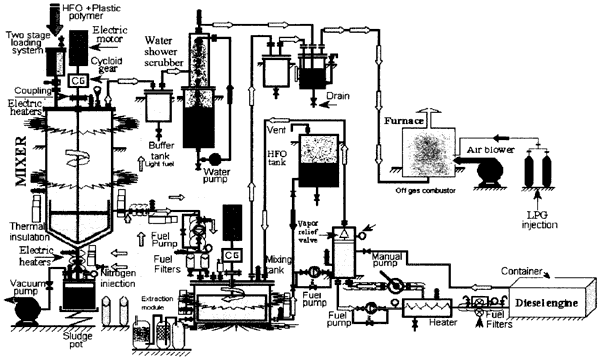
Fig. 2 The research facilities
BACK CONTENTS NEXT