I−3−5 施設・設備
<1> 造船所表流水処理技術(Shipyard Storm Water MOP−UP)
期間:1999年6月〜2001年2月、コスト総額63万9,000ドル(造船所32万9,000ドル、NSRP ASE 31万ドル)
本プロジェクトはサンディエゴのBiopraxisが開発した重金属処理技術を造船所の表流水の処理に応用しようとするプロジェクトで、Biopraxisと分離装置担当のチェスター・エンジニアリングが中心となってテストを実施し、報告書を作成した。造船所としてはNASSCO、エレクトリック・ボート、トッド・パシフィック、インガルス、BIW、アトランティック・マリンが参加し、造船所表流水の提供等で支援している。
MOP−UP技術は自己の重量の数倍の溶解金属を吸収する非常に高率の良い吸収剤を使用している。従ってスラッジの量は他の技術に比べて非常に少ないのが特徴である。本技術は既にエネルギー省(DOE)の地下ミズプロジェクトでその優秀性が実証されている。DOEプロジェクトでは地下水中の重金属及び放射性核種がppb(parts per billion)、場合によってはppt(parts per trillion)のレベルまで除去されたと報告されている。本プロジェクトのスラッジ除去装置としてチェスターが選んだのは、ヨーロッパで飲料水や表流水処理用に開発され広く使われているActifloである。Actifloは起動後15分で定常運転の9,000万ガロン/日の処理量に達する。装置は小型でかつ運転コストも安い。本プロジェクトはMOP−UP技術とActiflo技術を組み合わせたものであり、最終報告書もBiopraxisとチェスターが分担して作成している。Biopraxisの部分では各造船所から提供された表流水の成分、処理結果、ライフサイクルコスト等、チェスターの部分には表流水の流れと特色、重金属、浮遊固体、油、グリースの分離技術、MOP−UP以外の表流水処理技術とコスト等について述べられている。
Actifloシステム
出典:NSRP
<2> 造船所表流水処理の実証(Treatment of Shipyard Storm Water)
期間:2000年4月〜2003年8月、コスト総額:101万3,000ドル(造船所50万7,000ドル、NSRP ASE 50万6,000ドル)
本プロジェクトは都市下水処理のような受動濾過システムを造船所の表流水処理に利用すること目的としたプロジェクトでNASSCOが中心となりHart Crowser及びストーム・ウォーター・マネージメントが参加している。造船所に限らず米国の工場は環境保護庁(EPA)の定める連邦汚染物質排出防止システム(NPDES:National Pollutant Discharge Elimination System)によって排水中の汚染物質濃度が厳しく規制され、その規制値は益々厳しくなっている。造船所の表流水も例外ではない。本プロジェクトでは2001年NASSCO工場内に処理システムが建設され、2001年にテストされた。テストではフィルターとして3種類の大きさの米粒大の有機媒体を種々の比率で混合し、何回もテストした。2001年9月には表流水中の銅の減少率は56〜77%、亜鉛の減少率は60〜86%の成績を収めた。プロジェクトチームでは本システムの建設コストは造船所内排水面積1エーカー当たり4〜6万ドルと試算している。2001年9月の初期テストの結果を踏まえプロジェクトチームではシステムの効率を上げる改良を実施中である。
(拡大画面:108KB) |
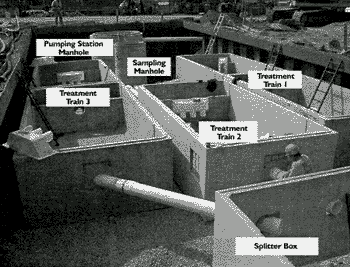 |
表流水濾過システム 出典:NSRP
<3> 船舶建造・修理業のための人間工学コンセンサス・ガイドラインの開発(Ergonomic Guideline)
期間:1999年9月〜2002年11月、コスト総額:83万4,000ドル(造船所28万4,000ドル、NIOSH 24万5,000ドル、NSRP ASE 30万5,000ドル)
本プロジェクトは船舶建造・修理作業に人間工学的要素を盛り込もうとするプロジェクトで、NIOSH(国立職業安全衛生研究所)が中心となりMEMIC、バス・アイアン・ワークス、コンチネンタル・マリン、ハルター・マリン、インガルス、ジェフ・ボート、ピュージェット・サウンド海軍工廠、トッド・パシフィック、その他大学関係者が参加している。米国造船所の従業員に対する事故補償費は高額である。35才で扶養家族のいる標準労働者が職場事故で復帰不能になった場合平均180万ドル、扶養家族がいなくても160万ドルが支払われる。
2001年に海軍工廠関連で9,100万ドルの補償金が支払われ、この額は海軍全体では2億4,700万ドルに達している。事故は作業を一時的にストップさせ、全体のスケジュールを遅らせ、補償金によるコスト損失も大きい。事故を減らして補償金を減らすには、下記に示すような安全及び環境対策を造船作業全体のプロセスに組み込む必要がある。
・人間工学的要素の見直しと改善
・危険材料の使用減少
・危険廃棄物の産出減少
・作業場所での危険排出物への作業員の暴露減少
本プロジェクトは第1番目の人間工学的要素改善のガイドラインを作って事故を減らそうとするプロジェクトで、既にガイドラインが作られ造船所に配布されている。本ガイドラインは内容的にできが良く、職業安全衛生局OSHA(Occupational Safety and Health Administration)は当面本ガイドラインをOSHAガイドラインとして代用することを決め、また建設業等の類似産業も本ガイドラインを参考に各産業の人間工学ガイドライン作りを進めている。本ガイドラインに従って、多くの造船所が人間工学的改善を進めているが下記はその一例である。
・ジェフボートはプレート切断機の後部ピット中にテーブルを設置し前かがみ作業を減らした。
・ピュージェットサウンド海軍工廠ではドライドックの材料仕分け箱を傾斜形とし、取りやすくした。
・トッド・パシフィックでは作業長及び現場マネージメントに人間工学訓練を実施した。
<4> 溶接時のガス暴露(Welding Emissions)
期間:2000年6月〜2002年11月、コスト総額:210万ドル(造船所105万ドル、NSRP ASE 105万ドル)
本プロジェクトは前項で述べた事故及び補償金を減らす方法の第4番目、「作業場所での危険物排出への作業員の暴露減少」に該当するプロジェクトでエディソン溶接研究所(EWI)が中心となりアボンデール、インガルス、エレクトリック・ボート、ESAB Welding Products、ニューポートニューズ、バス・アイアン・ワークス、NASSCO、Lincoln Electric、NSWCCD、Kura Environmentalが参加している。溶接時に出るガスは基本的に作業者に有害であり、労働安全衛生局(OSHA)および米国政府/産業衛生学者コンファレンスから排出基準が出されている。米国の造船所がこれらの基準に合格しようとすると年間6億4,000万ドルの費用がかかるといわれている。
出典:NSRP/NAVSEA
本プロジェクトチームは発足と同時に第1段階作業として国内16造船所の作業実施方法の基礎調査を実施し、報告書を出している。第2段階では、より進んだ溶接プロセスと制御プロセスを開発し、それらを用いて暴露データを取得した。進んだ溶接プロセスとして開発されたのはパルスGMAW、低ヒューム・フラックス溶接棒、低C02シールドガス、金属コア溶接棒等であり、進んだ制御プロセスとして開発されたものにはヒューム抜き取りガン、ヒューム・ベンチレーション等がある。その他クロミウム排出の少ない材料の使用、機械化、環境ガイドラインの積極使用等について、チームメンバーが分担して作業した。その他の作業分担は下記である。
・既存の同じベンチレーションとガンによる排出テストがニューポートニューズ、バス・アイアン・ワークス、及びNSWCCDで行われたが、エディソン溶接研究所(EWI)が全てコーディネートした。
・NSWCCDは同研究所の設備を使って上記と同じベンチレーションとガンを使い、ヒューム発生率及び作業者暴露テストを実施した。
・エレクトリック・ボートはER100SI、ER308、ER309、ER625及び合金276溶接棒を使ってパルスGMAWヒューム暴露データを集めた。
・ニューポートニューズは溶接棒3社と協力してアルゴン/5%C02ガスで作動する低ヒュームフラックス・ワイヤーを開発中である。
<5> 5Sの造船所への適用と訓練(5S)
期間:200年3月〜2001年9月、コスト総額:122万8,000ドル(造船所77万2,000ドル、NSRP ASE 45万6,000ドル
本プロジェクトはトヨタのジャスト・イン・タイム(JIT)生産方式で強調された5S(整理、整頓、清掃、清潔、躾)をリーン製造方式に適用するに際し、米国流に語呂合わせして持ち込み、生産性向上に役立たせようとするプロジェクトである。トッド・パシフィックとアトランティック・マリンが中心となり、他にV2Rコンサルタントが参加している。造船所の現場で生産性向上のための第一歩とも言うべき整理(Sort)、整頓(Straighten)、清掃(Shine)、清潔(Standardize)、躾(Sustain)が生産性の向上に繋がることが眼に見えている。
上記5Sのうち、清潔は整理、整頓、清掃の行為で得られる結果であり英語では苦労してStandardizeと訳しているが、Sort、Straighten、Shineを維持しモニターするためのルールを作ろうと言う意味である。躾をSustainと訳したのは社員に訓練を通じて整理、整頓、清掃を根づかせようとする意図を表わしている。NSRP ASEでは上記語呂合わせが使用されているが、Straightenの代わりにSimplificationあるいはStabilizing、Shineの代わりにSystematic Cleaning等の単語で置き換えている産業もある。
トッド・パシフィックでは造船所内の8工場に各8万ドル、合計64万ドルの費用をかけて5S体制を確立し、初年度各工場当たり15万ドル、合計120万ドルが節約されたと報告している。同じようなレベルの利得がアトランティック・マリンからも報告されており、初年度に関しては5Sの適用による生産性の向上は両造船所とも30%と見積られ、長期的に見ても5Sの適用だけで持続的に10%の生産性向上が確実とみられている。5Sの最大の利得は造船所従業員の意識改革に役立つことである。両造船所の経験を基にして5Sを具体的に実施するためのガイドラインがV2Rコンサルタントから出されており、いずれの米国造船所も5Sを適用出来る体制になっている。
<1> 横断的仮想リソース・センター(Crosscut Resource Center)
期間:1999年7月〜2002年11月、コスト総額:178万ドル(造船所84万5,000ドル、NSRP ASE 93万5,000ドル)
本プロジェクトは造船業に従事する個人及び組織についての情報をオンラインで流し、重複投資を避け、人的及び組織資源の有効活用を図ることを目的としている。造船所として、エレクトリック・ボート、アボンデール、バス・アイアン・ワークス、カスケード・ジェネラル、トッド・パシフィック、ジェフボートが参加し、その他ミシガン大学運輸研究所、ペンシルバニア大学先進技術研究所が加わっている。本プロジェクトでオンライン化が試みられた情報分野は、教育及び訓練、組織変更、人的資源及び技術移転である。11の分野のオンラインサービスが可能となっている。4
11の分野は下記である。なお、本プロジェクトはMARITECHの造船情報インフラストラクチャー・プロジェクトSHIIP(Shipbuilding Information Infrastructure Project)で得られた成果を発展させたものである。
・クロスカット・コンタクト及びコミュニテイ
・クロスカット・リンク
・出版目録及び抜粋
・プロジェクトの結果
・提案者及びマネジャー・ガイド
・リクルート機関
・産学モデル
・訓練コース・ライブラリー
・バーチュアル・チーム編成
・バーチュアル・ワークショップ
・教育交換
|