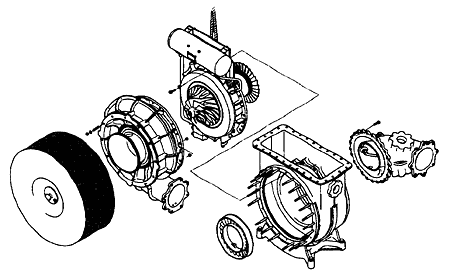
Fig.1: Modular concept of the TPL turbocharger series
The modular design of the TPL..-B turbocharger also offers good flexibility when mounting the turbocharger on the engine: A compact foot, optimised using FE - calculations, leads to compact support brackets. Inlet and outlet flange positions with increments of 15° are available. The air inlet can be realised either with a filter-silencer, which is usually preferred, or with a suction branch. The radial, insulated gas-inlet casing, although very compact, is optimised for minimal losses. The gas-outlet casing is in the form of a rectangular flange. These features and the complete exhaust gas system after the turbine ensure that the pressure recovery is excellent, with the benefit of both increased efficiency and low exhaust gas velocities. For greater convenience on two-stroke engines, TPL..-B turbochargers feature a lateral oil-inlet flange. Fig.2 shows a cross-section of the new turbocharger.
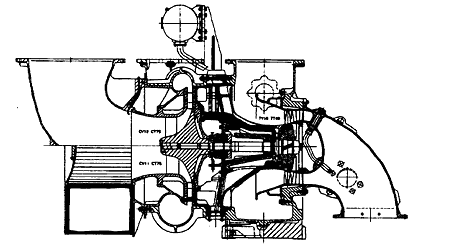
Fig. 2: TPL..-B turbocharger, cross-section
The TPL..-B is available in four frame sizes, dimensioned for optimised flow range adaptation to the two-stroke engine market. Thus, optimal solutions with regard to the size or number of turbochargers can be achieved for two-stroke engines.
Since two-stroke engines have a common lubrication system, which is driven by electric pumps rather than the engine itself, an emergency oil supply has to be provided to ensure that the turbocharger runs out safely in the event of the system shutting down. As an alternative, a high-tank can be installed in the vessel. To avoid having to provide additional equipment, the TPL..-B turbocharger can be equipped with an integrated emergency oil tank, mounted on top of the bearing casing, see Fig.2.
2.1 Components
2.1.1 Turbine
The TPL..-A turbine was designed to match all kind of turbocharging systems. Especially pulse charging, in combination with high-pressure ratios, requires a highly sophisticated design. The use of different flow solvers in combination with strength calculation programs, based on the finite element method, led to a turbine with lacing wire as shown in Fig.3 (left).
Based on the TPL.-A turbine a wide chord version without lacing wire was derived for the TPL.-B type. With a reduction of the blade number and scaling up of the turbine profile the pitch to chord ratio and therefore the well-proven Mach number distribution could remain almost unchanged while the losses caused by the lacing wire were omitted.
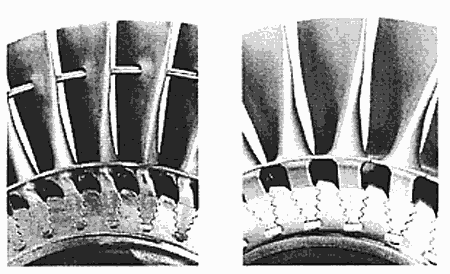
Fig.3: TPL..-A (left) and TPL..-B turbine (right)
Additionally the gas outlet casing was re-designed with a rectangular outlet flange. The outlet area being clearly larger than that of the TPL..-A. The bigger outlet area itself and the improved dynamic pressure recovery of the whole casing leads to a reduction of the gas velocity and thus to dynamic losses at the turbo charger outlet.
For TPL..-B five turbine wheels and more than twenty nozzle rings can be specified. Because of this hardware diversity, the desired turbocharger characteristic can be achieved for nearly every volume flow within the single frame sizes. The high efficiency level obtained by the referenced design changes yields a thermodynamic flexibility that enables the turbine characteristic to be shaped while ensuring excellent full load efficiency. Fig.4 demonstrates this with 3 examples of nozzle rings (TA) combined with one of the five available turbine wheels.
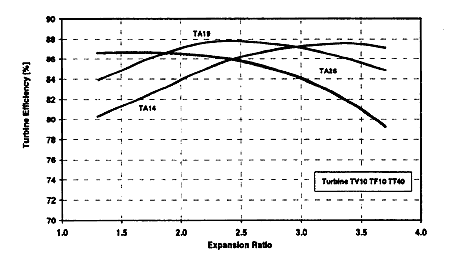
Fig.4: Measurements of TPL..-B turbine efficiency for different specifications
All modern large 2-stroke engines use a constant pressure charging system. Compared to a pulse charging systems, with narrow pipes and multiple gas inlet casings, the excitation of the turbine is significantly lower. Nevertheless high cycle fatigue failures of uncoupled turbines are also known on 2-stroke engines. Especially for lower modes the stress amplitudes could be significantly reduced with TPL..-B turbine, compared with a conventional constant pressure design. On the one hand, the stiffness of a wide chord blade is higher, shifting critical resonances out of the operating range. On the other hand the dynamic stress level for lower bending modes is reduced with reduced number of blades, following an equation of Traupel [1]. Blade vibration measurements with different nozzle rings and amplified excitation forces proved this concept and showed the stress level well below the ABB design limit as shown in Fig.5.
BACK CONTENTS NEXT